Cement manufacturing facilities encompass distinct components whose roles are integral to the production process. Among such components, the liner types employed within the plant possess critical importance, influencing efficiency and production. Liners are pivotal, covering equipment like the rotary kilns, grinding mills, and preheaters, providing protection and enhancing performance. Selecting the appropriate liner type demands a profound grasp of their characteristics and functionality, tailored to specific plant requirements.
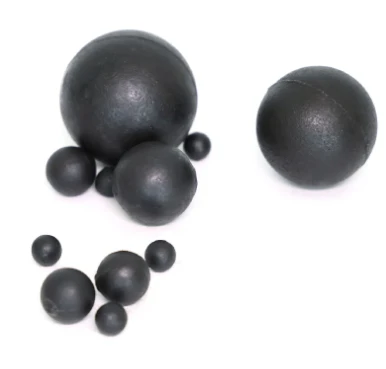
The diversity of liners in cement facilities can be categorized into various types including ceramic liners, rubber liners, and steel liners, each having unique attributes.
Ceramic liners are renowned for their exceptional resistance to wear and heat, making them a suitable choice for areas subjected to intense abrasion and temperature. Their longevity reduces maintenance frequency, thus offering cost-effectiveness despite an initial investment. Ceramic liners' high thermal resistance makes them adaptable for kilns and preheater areas in the cement plant, where extreme conditions prevail. Notably, advances in ceramic technology allow for customization, catering to unique plant configurations and specific operational challenges.
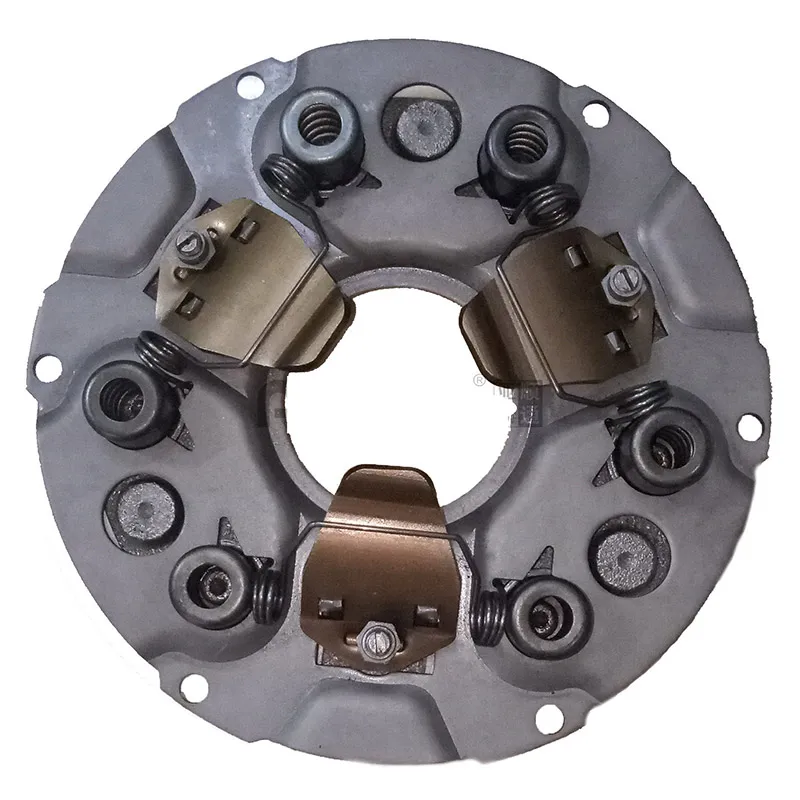
Rubber liners, on the other hand, offer unparalleled versatility and shock absorption. Their properties make them favorable in grinding applications, where impact and abrasion are significant. Rubber’s inherent flexibility reduces noise levels in the plant, contributing to a more favorable working environment. The reduced structural stress extends equipment life, hence promising an economic advantage. The lightweight nature of rubber facilitates maintenance and replacement, an essential factor in enhancing production continuity.
The lining type of cement plant
Steel liners are distinguished by their robustness and structural integrity. Offering high durability against impact and wear, steel liners are often employed in ball mills where the mechanical load is substantial. The customizable properties of steel, through alloying, allow for liners that are tailored to specific functional needs of cement manufacturing. Innovation in metallurgical processes has further strengthened the efficiency of steel liners, including the development of hybrid options incorporating composite materials to balance durability and cost.
Aligning liner selection with operational needs demands expertise and strategic thinking. Factors such as the raw materials employed in production, operational temperatures, and the mechanical load of the process are essential in determining liner suitability. Collaborating with experts in materials technology and undergoing comprehensive plant assessments will guide optimal liner application, promoting longevity and effectiveness.
In conclusion, embracing the ideal liner type within a cement factory can drastically optimize operations. The choice extends beyond immediate application, considering future adaptability and technological advancements. As the architecture and machinery of cement plants evolve, the potential for increased efficiency through superior liner application becomes increasingly viable. By adopting a strategic approach to liner selection, cement plants predict not only an enhancement in operational efficiency but also sustainable growth aligned with proactive manufacturing practices.
Engaging continuously with advancements in liner technology and industry trends allows plant operations to maintain a competitive edge, ensuring the manufacturing process is not only effective but, importantly, ahead of evolving industry standards.