Mastering the Art of Forged Grinding Balls Industry Insights and Innovations
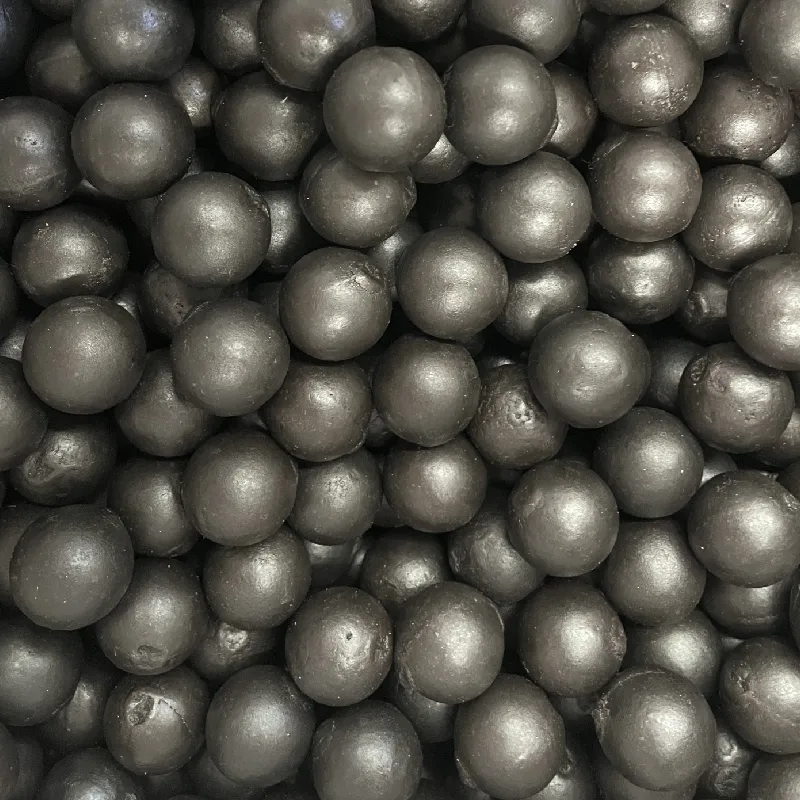
Forged grinding balls are integral components in industries focused on mining, cement manufacturing, and thermal power generation. As key players in grinding operations, their quality and performance significantly influence industrial productivity and operational efficiency. This article delves into the expert knowledge and innovative practices surrounding forged grinding balls, emphasizing their importance, development, and application.
Forged Grinding Balls An Overview
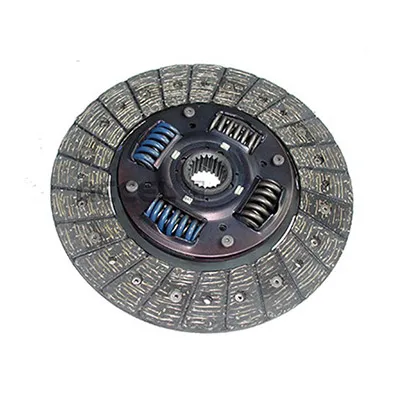
Forged grinding balls are made from high-quality steel, distinguishable by their lack of porosity and superior toughness. Their manufacturing process involves cutting, forging, hardening, and tempering high-carbon steel billets, which results in increased durability and resistance to wear and impact. These grinding balls optimize grinding media costs due to their extended service life and enhanced performance, making them invaluable in energy-intensive environments.
Experience in Forged Grinding Ball Utilization
From the experience shared by industry veterans, the choice of forged grinding balls over cast counterparts often results in a marked improvement in milling efficiency. Companies utilizing forged balls report a noticeable reduction in energy use, which translates to lower operational costs and reduced environmental impact. Additionally, the consistency in size and shape retention under high-stress conditions minimizes equipment wear, thereby prolonging the lifespan of machinery components.
Innovations Driving Expertise in Manufacturing
Recent advancements in metallurgy have led to the development of forged grinding balls with unique alloy compositions. These innovations enhance their hardness, abrasion resistance, and fatigue strength. Cutting-edge heat treatment technologies further refine their granularity and microstructure, providing uniform hardness throughout the ball. This progression in materials science enables the production of grinding media tailored to specific industrial needs, ensuring customized solutions for diverse operational challenges.
Authoritativeness in Quality Assurance and Standards
forging sliding ball
The production of forged grinding balls is governed by stringent quality assurance practices. Reputable manufacturers adhere to international standards such as ISO 9001, ensuring precision at every production stage. Regular quality audits and in-process inspections verify chemical compositions, physical dimensions, and mechanical properties. Such rigorous compliance ensures that customers receive products that meet their specific performance demands.
Building Trust through Performance and Reliability
Trustworthiness in forged grinding balls is built on consistent performance and reliability. Through comprehensive field studies, producers offer guarantees that their products will achieve desired grind outcomes with minimal downtime. This reliability fosters long-term partnerships with clients who depend heavily on uninterrupted production capabilities. Customer testimonials and case studies from globally recognized firms often highlight the significant gains in efficiency and cost-effectiveness achieved through the exclusive use of forged grinding balls.
Applications and Industry Impact
In mining, the extraction and processing of ores demand materials that can withstand high impacts and abrasive conditions.
Forged grinding balls meet these requirements, enhancing the liberation of valuable minerals. Similarly, in cement manufacturing, they improve the grinding process's output quality and reduce energy expenditures. In thermal power plants, the efficient milling of coal directly influences electricity production, making the role of grinding balls crucial.
The Future of Forged Grinding Balls Sustainability and Efficiency
Future trends in the forged grinding ball industry are poised to focus on sustainability and efficiency. With a growing emphasis on reducing environmental footprints, manufacturers are exploring eco-friendly production techniques and recyclable materials. Enhanced durability and lifespan of forged balls contribute to reduced resource consumption and waste generation.
Furthermore, the ongoing development of smart manufacturing technologies promises to revolutionize quality control processes. Implementing IoT and AI in monitoring systems can provide real-time insights into ball performance and degradation, allowing for proactive maintenance approaches and reduced downtime.
In conclusion, the forged grinding ball industry exemplifies a commitment to excellence, innovation, and sustainability. By continuously improving manufacturing processes and maintaining strict quality standards, the industry not only supports operational efficiency but also aligns with global movements toward sustainable industrial practices. As demands for optimized grinding media continue to rise, the advancements in forged grinding balls are set to pave the way for future progress across multiple sectors.