The manganese processing industry is pivotal in various sectors due to the metal's unique properties, which include hardness, toughness, and resistance to wear. To effectively harness these attributes, a comprehensive understanding of the manganese processing stages is essential. Drawing from years of experience and professional expertise, we delve into the intricate processes involved in transforming raw manganese into commercially viable products and the industry's best practices for ensuring quality and compliance.
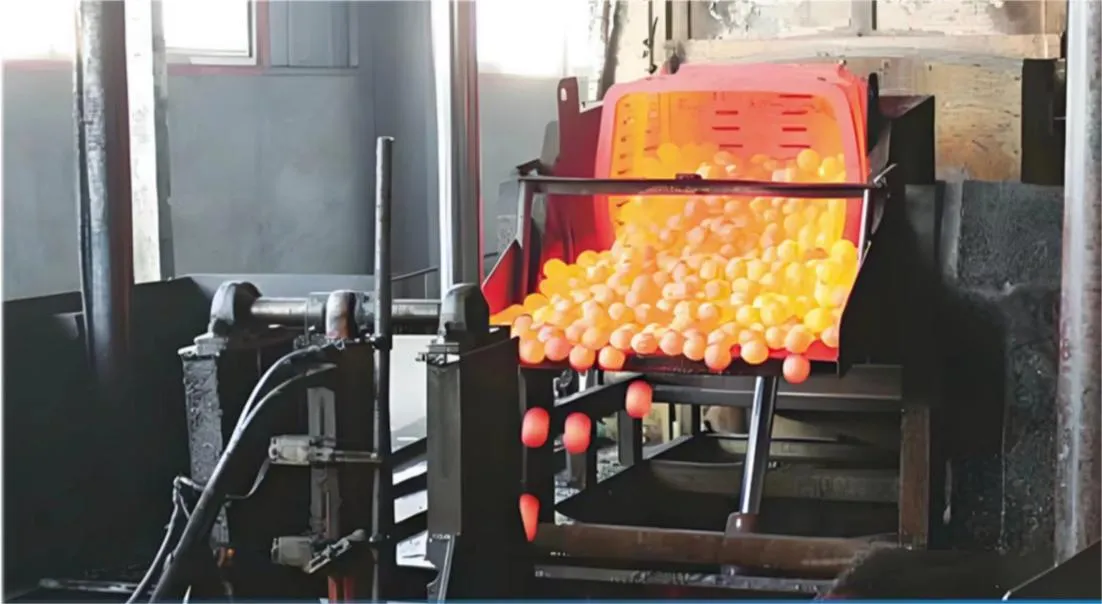
Manganese, often found in combination with iron, is extracted primarily through open-pit mining. The initial stage involves careful removal of the overburden, which is the soil and rock overlaying the manganese ore seams. This requires high-level proficiency in mining techniques and machinery to ensure efficiency and safety. Once exposed, the manganese ores undergo mechanical processing, including crushing and grinding, to reduce the ore to finer particles suitable for the extraction of manganese.
Next comes the concentration process, where the finely ground ores are subjected to various beneficiation techniques like froth flotation, gravity separation, and magnetic separation. These methods require precision and expertise to increase the manganese content and enhance the ore's quality. Trustworthiness in this field is attributed to continuous monitoring and adjusting processes based on the specific characteristics of the ore being processed.
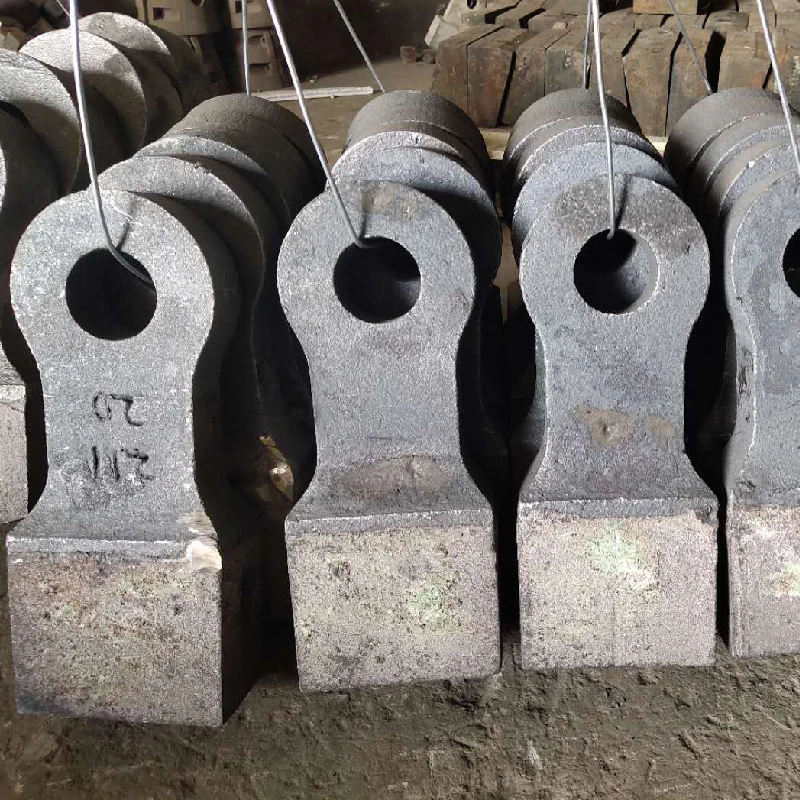
Following concentration is the smelting phase, an area reliant on expertise in pyrometallurgical techniques. The smelting process transforms manganese ores into ferromanganese or silicomanganese through the application of heat and reducing agents in electric arc furnaces. This highly specialized process demands a deep understanding of thermodynamics and chemical reactions, emphasizing the importance of qualified professionals to achieve the desired alloy compositions.
To achieve exemplary results, professionals must also engage in the refining stage, involving further treatment of alloys to eliminate impurities. Electrolytic manganese, known for its high purity, is used in specialty applications such as battery production. This stage requires authoritative knowledge of electrolytic processes and strict adherence to quality standards to produce manganese suitable for high-performance applications.
Manganese treatment
Innovation in manganese processing involves exploring environmentally friendly techniques and safer alternatives for traditional methods. Research and development play a crucial role, with authoritative bodies constantly reviewing and updating methodologies to reduce environmental impacts and enhance the sustainability of manganese processing.
Professionals and experts who maintain robust trustworthiness in this domain also focus on traceability and compliance with international standards and regulations. Rigorous documentation and adherence to policies ensure that the entire process, from the mine to the final product, meets all legal and quality requirements.
The manganese processing industry is not only about transforming raw material into valuable commodities but also about building trust through transparent operations and responsible practices. Companies that thrive in this sector are those that prioritize ethical practices, continuous improvement, and adaptation to new technologies.
In conclusion, manganese processing demands a blend of experience, expertise, and authoritative knowledge. The industry's leaders are those who not only leverage advanced technologies but also foster trust through stringent adherence to quality and environmental standards, ensuring the delivery of premium and sustainable manganese products to the market.