Manganese steel, often referred to as Hadfield steel, is renowned for its high impact strength and resistance to abrasion. Its unique characteristic is its ability to work-harden upon impact, making it an ideal material for high-wear applications. The process of hardening manganese steel through heat treatment is a critical factor in enhancing its properties, particularly in the realm of industrial components and applications.
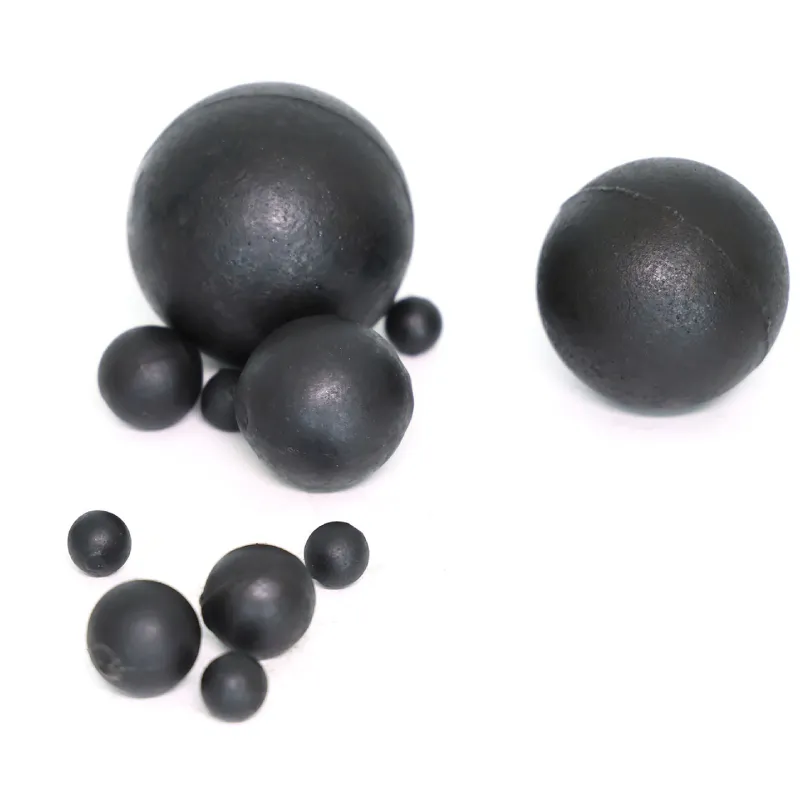
Manganese steel quenching involves a precise process of heating and rapid cooling to transform the steel's structure, optimizing its wear resistance and durability. This transformation is crucial for industries where materials are subjected to severe mechanical wear, such as mining, construction, and the manufacturing of heavy machinery.
To achieve successful hardening, the steel must first undergo solution treatment, which involves heating it to a temperature that allows the dissolution of carbides into the austenite matrix. This is followed by a rapid quenching process, typically in water or oil, to prevent the precipitation of carbides and ensure a high-impact resistant martensitic structure. The rapid cooling essentially locks in the hardness and toughness properties without allowing time for undesirable phases to form.
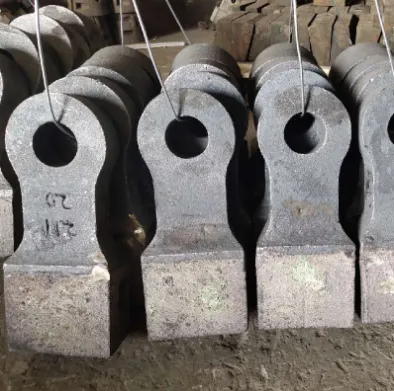
One key challenge in the quenching process is balancing the hardness level with the ductility of the material. If the steel is too hard, it may become brittle; if too ductile, it may not withstand abrasive conditions. Therefore, expertise in controlling the heating temperature, cooling rate, and the period at which the material is exposed to those temperatures is essential for optimizing the steel's performance.
manganese steel hardening
In practical applications, manganese steel's ability to undergo surface hardening under impact is leveraged in industries that require robustness and reliability. For instance, in the railway sector, it is used for manufacturing components like frog switches and crossings, providing durability and reduced maintenance. In the mining industry, crushers and grinding mills benefit from the long-lasting life span of manganese steel liners, which can withstand the rigors of crushing hard rock.
Recent technological advancements continue to improve the efficiency of quenching methods. Innovators are exploring sophisticated quenching technologies that incorporate modern sensors and computer-controlled systems. This technology allows for real-time monitoring and precise control over the quenching process, ensuring consistent and uniform hardening across large batches of steel components.
The authority and trustworthiness of manganese steel as a material of choice for heavy-duty applications are underscored by comprehensive testing and validation in harsh environments. Its proven track record across various high-impact industries highlights its indispensable role in the production of resilient components.
In conclusion, the quenching of manganese steel is an intricate process that enhances its ability to withstand extreme conditions. With expertise in metallurgy and ongoing advancements in technology, industries can continue to rely on manganese steel for its exceptional properties. Whether in construction, mining, or transportation, the benefits of manganese steel quenching remain pivotal to efficiency and longevity of steel components.