Within the competitive landscape of industrial manufacturing, the role of grinding ball manufacturers is pivotal, ensuring the efficiency and durability required in heavy-duty operations. A meticulous insight into the life cycle and craftsmanship of these cylindrical objects uncovers a world where expertise, precise engineering, and innovation converge.
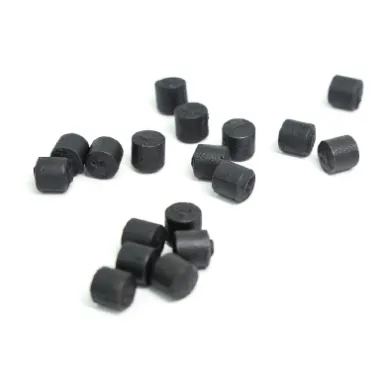
Grinding balls originate from a diverse array of materials, each meticulously selected to suit specific applications. The choices range from chromium and manganese steels, preferred for their high abrasion resistance and toughness, to more exotic materials like ceramics used for applications demanding minimal contamination. This diversity in material selection is not merely an engineering requirement but a strategic decision by manufacturers to cater to a vast spectrum of industries, from mining to cement production.
One of the fundamental principles in grinding ball manufacture is precision engineering. The technological processes involved are, in many ways, an art form as much as they are a science. Manufacturers must employ advanced measuring instruments, like laser-guided tools, to ensure each ball adheres strictly to dimensional tolerances. Minute discrepancies can lead to catastrophic system failures, making accuracy non-negotiable.
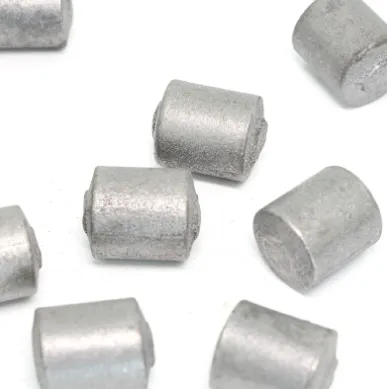
In recent years, a shift towards sustainability has become evident. Manufacturers are increasingly adopting environmentally friendly practices. Innovative manufacturing techniques, such as forging instead of casting, reduce energy consumption and increase the lifespan of grinding balls, thus minimizing waste. This transition reflects a broader industrial trend towards sustainability, meeting both ecological standards and customer demands for responsible corporate behavior.
Expertise in grinding ball manufacturing also extends to post-production testing. Rigorous tests, such as hardness testing, impact testing, and wear resistance evaluations, are crucial in guaranteeing product reliability. The application of metallographic examination techniques allows for the granular analysis of microstructural integrity, ensuring that each grinding ball can withstand the operational stresses of its intended environment.
Authoritativeness within the domain is often established through certifications and adherence to international standards such as ISO 3290-12014 for rolling ball products. This universal benchmark ensures that the grinding balls meet strict quality specifications, fostering customer trust and solidifying a manufacturer’s reputation as a reliable supplier.
grinding ball manufacturers
From a trustworthiness perspective, transparency in the supply chain is paramount. Many leading manufacturers are adopting digital solutions like blockchain to offer customers full traceability of their products. This not only boosts confidence in product authenticity but also enhances accountability throughout the manufacturing process.
A distinctive feature of expert grinding ball manufacturers is their ability to customize offerings. By closely collaborating with clients to understand their specific needs, manufacturers tailor grinding balls that optimize performance in particular applications. Customization may include altering chemical compositions or physical dimensions to suit unique operational conditions, such as extreme cold or high-pressure environments.
Moreover, the integration of digital technology is reshaping the landscape of grinding ball manufacturing. Predictive analytics and IoT (Internet of Things) are being deployed to preemptively identify manufacturing defects and optimize production lines in real-time. This technological infusion not only elevates operational efficiency but also empowers manufacturers to provide predictive maintenance services, reducing downtime and enhancing the lifecycle of their products.
Finally, customer service excellence sets leading grinding ball manufacturers apart. Comprehensive after-sales support, including on-site consultations, failure analysis services, and technical training sessions, underscores a commitment to customer success. These services are a testament to the manufacturer’s dedication not only to selling a product but to building enduring partnerships with their clients.
In summary, the grinding ball manufacturing industry is a dynamic amalgam of traditional craftsmanship and cutting-edge technology. Through precision engineering, sustainable practices, and technological advancements, manufacturers provide indispensable components crucial to the seamless operation of a wide array of industries. With a continued focus on quality and innovation, grinding ball manufacturers are poised to remain at the forefront of industrial engineering, ensuring that they meet the ever-evolving demands of global industries with credibility and authority.