The ball mill is a fundamental piece of equipment for the mining and cement industries, known for its role in grinding materials into fine powder, facilitating subsequent processing stages. This article delves into the distinctive medium used in ball mills, exploring its impact on efficiency and performance.
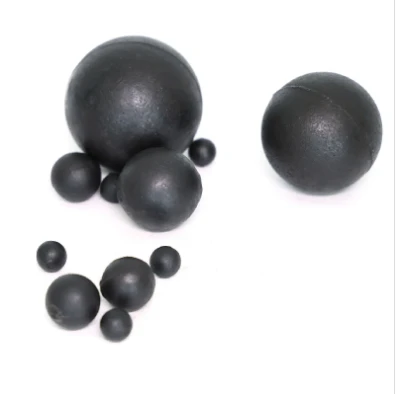
One of the foremost considerations is the choice of grinding medium, commonly steel balls of varying sizes. This choice significantly influences the effectiveness and efficiency of the milling process. The varying sizes cater to different milling needs larger balls are responsible for breaking up large particles, while smaller ones tackle the finer materials. This graded approach ensures comprehensive breakdown of materials, optimizing the grinding process.
In real-world applications,
the material composition of the balls is crucial. Steel is the traditional choice due to its density and durability, allowing it to exert significant force on the raw materials. However, advanced variations like ceramic grinding media are now being explored. These alternatives offer benefits such as reduced contamination and enhanced wear resistance. In one case study at a cement plant, switching to ceramic media led to a 15% increase in the lifespan of the mill, offering a compelling reason to consider such alternatives.
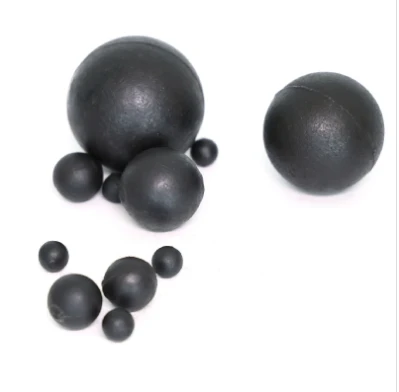
From an expertise standpoint, understanding the dynamics of charge interaction within the mill is paramount. The interaction between different sizes of balls and the tumbling motion ensures effective grinding. However, professionals emphasize the need for regular monitoring. Over time, balls can wear down, diminishing their effectiveness and necessitating replacement or replenishment to maintain optimal performance.
The weight and volume of the balls relative to the mill size also factor into the efficiency. An overcrowded mill can lead to reduced grinding efficiency due to hindered motion of the balls, while an insufficient amount can prolong the process unnecessarily. Experts recommend maintaining a balance, often using the thumb rule of filling 30-45% of the mill’s volume with the grinding medium. This ensures adequate space for movement, enhancing the system's milling efficiency.
meio de moinho de bolas
For those in procurement and maintenance, choosing the right supplier for these grinding media is critical. A reputable supplier offers consistency in product quality, ensuring that each batch of media performs as expected in terms of durability and grinding efficiency. This reliability reduces the risk of unexpected shutdowns due to media failure, reinforcing trustworthiness in the choice of supplier.
Moreover, technological advancements have led to the incorporation of smart sensor technology in modern ball mills. This innovation allows for real-time monitoring of media wear rates and mill conditions, facilitating timely maintenance and replacements. Such technology is vital for operations aiming for minimal downtime and optimal productivity.
In terms of trustworthiness, it is essential to adhere to industry standards for the materials used in mill media, particularly in food or pharmaceutical applications where contamination can have serious consequences. Adhering to these standards not only prevents contamination but also aligns with regulatory expectations, ensuring product safety and quality.
Finally, efficiency improvements in media usage impact environmental sustainability. Reduced wear rates mean less frequent replacements, decreasing the demand for raw materials and energy usage. This approach not only supports sustainability goals but also contributes to cost savings.
In conclusion, the choice and management of ball mill media contribute significantly to the efficiency, productivity, and sustainability of milling operations. By drawing insights from practical experience, expertise in material science, and adherence to standards, industries can optimize their milling processes, ensuring high-quality outcomes while minimizing operational risks.