Understanding and optimizing the use of grinding media in ball mills is critical for enhancing the efficiency and performance of industries relying on particle size reduction. Known in German as Mahlkörper-Kugelmühle, these grinding media play a vital role in a wide array of industrial applications, from metallurgy to pharmaceuticals.
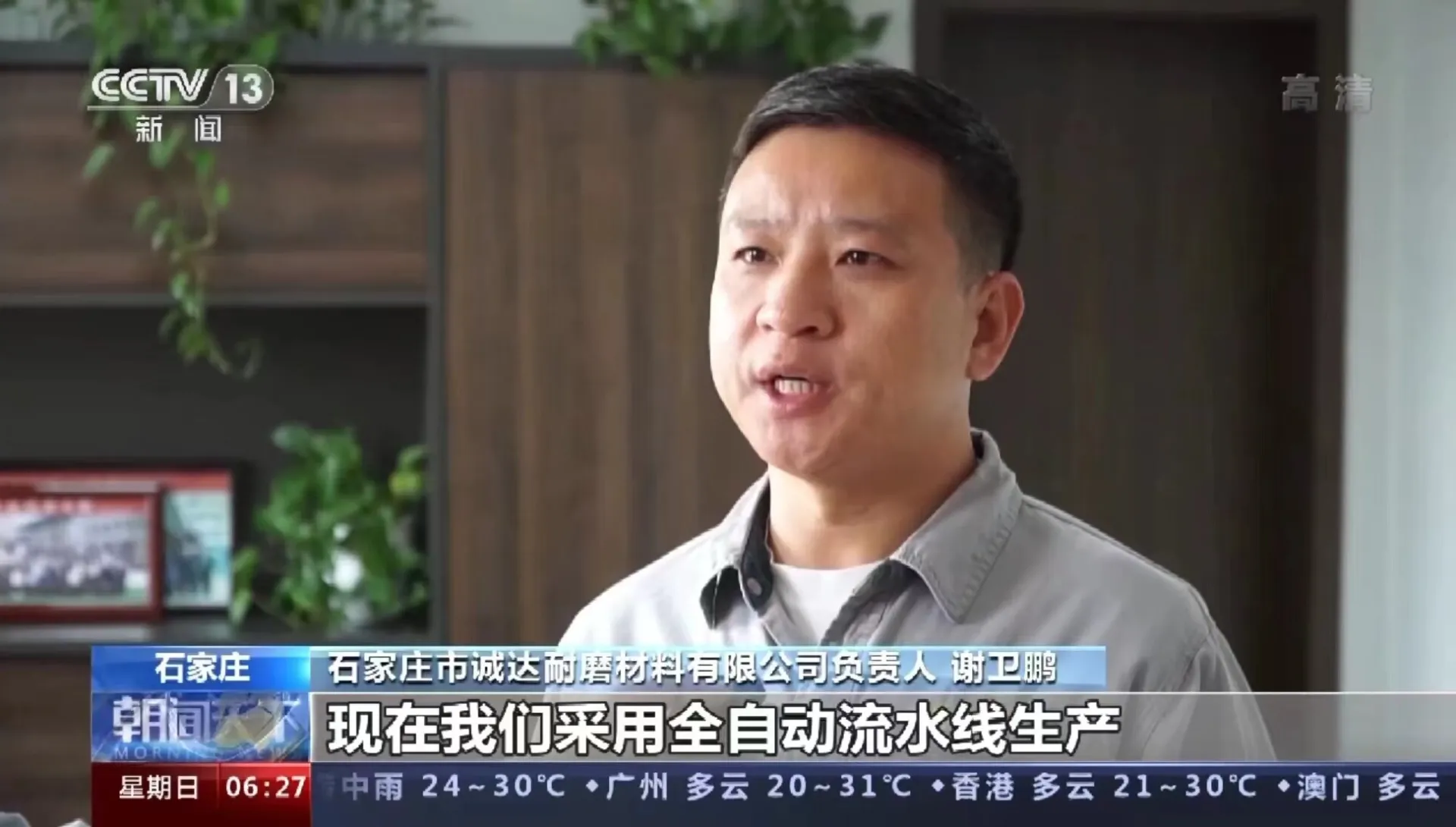
Among the primary factors in achieving optimal grinding performance is the selection of the correct type and size of the grinding media. Mismatches in the selection can lead to inefficiencies and increased operational costs. Therefore, it is essential to have a deep understanding of the materials and specifications best suited for specific milling tasks.
Steel balls, ceramic balls, and high-density grinding media are some of the most common types used in ball mills. Each type offers unique benefits. Steel balls, being robust and relatively inexpensive, are ideal for heavy-duty grinding operations. Their high density helps in the rapid reduction of particle sizes. However, they can introduce impurities, which might be undesirable in some applications.

Ceramic balls offer a contaminant-free alternative. Their inert nature makes them suitable for grinding processes where purity is a priority, such as in the manufacture of pharmaceuticals. Despite their higher cost, the purity advantages they offer often justify their use.
Selecting the correct size of the grinding media is another crucial aspect, which significantly impacts the milling efficiency. Smaller milling media allows for finer grinding, which is essential for achieving desired particle sizes in high-precision processes. Conversely, larger media facilitate efficient energy transfer, making them excellent for breaking down coarser materials.
Furthermore, the material composition of the milling media can affect the wear rate and longevity of both the media and the mill itself. Investing in higher quality materials can reduce replacement frequencies and maintenance costs in the long run. Advanced engineering has led to the development of media with improved resistance to abrasion and heat, further optimizing the milling process.
mahlkörper-ball mill
Real-world experiences shared by industry veterans highlight the importance of periodically reviewing and adjusting the choice of milling media. This adaptability is crucial in responding to changes in feed material properties or variations in the desired final product specifications. By monitoring variables such as milling time, rotational speed, and media loading, one can significantly enhance the process control and optimize the operational parameters of ball mills.
Expert insights also stress the necessity of maintaining proper mill balance. Overloading can lead to inefficiencies and increased energy consumption, while underloading might result in poor particle size distribution and longer milling times. A balanced approach ensures the milling media properly interacts with the processed material, maintaining the integrity and efficiency of the process.
In industries where regulatory compliance is essential, such as in pharmaceuticals and food production, ensuring the traceability and quality of the milling media is a testament to a company's commitment to excellence and safety. Using certified media from reputable manufacturers not only boosts operational trust but also aligns with industry best practices and standards.
Authoritative sources emphasize the significant advancements in milling technology, which have expanded the versatility and efficiency of ball mills. From the integration of advanced materials to the incorporation of automation and real-time monitoring systems, the modern Mahlkörper-Kugelmühle has evolved into a sophisticated piece of machinery tailored to meet stringent industrial demands.
Trustworthy operation of milling processes is bolstered by continuous innovation and adherence to quality standards, fostering environments where efficiency, safety, and productivity coexist. Engineers and operators are encouraged to stay informed about emerging trends and technologies in milling media to maintain their competitive edge.
In conclusion, the successful utilization of grinding media in ball mills requires a blend of technical knowledge and practical experience. Understanding the specific needs of the milling process, combined with rigorous selection and maintenance of the materials, ensures optimized performance and cost-effectiveness. Through strategic planning and smart management, industries can harness the full potential of their milling operations, delivering superior results and maintaining their leadership in the marketplace.