Ceramic milling media has steadily risen in prominence, revolutionizing industries with its remarkable attributes and applications. These sophisticated components, typically deployed in milling machines, distinctly outperform their metallic counterparts in life-span and performance, owing to their robust composition and superior wear resistance.
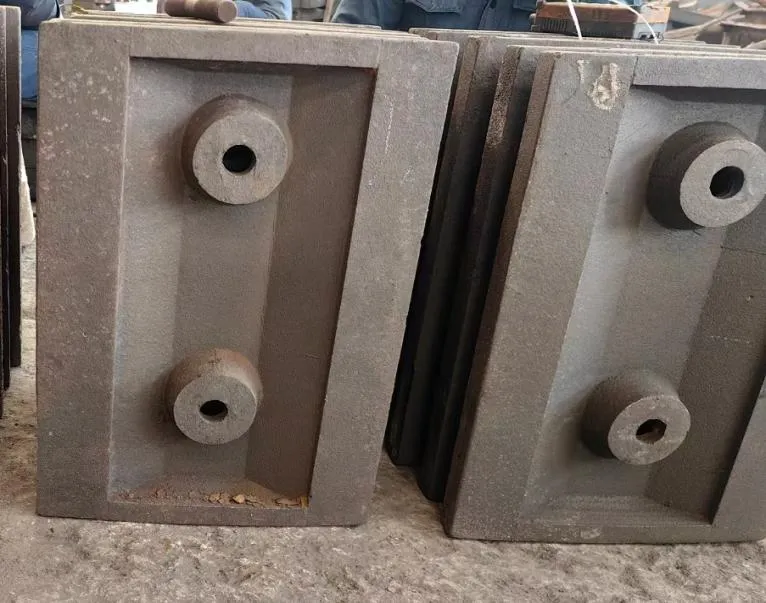
Industries ranging from pharmaceuticals to automotive, and even aerospace engineering, leverage ceramic milling media for a variety of applications including grinding and dispersing materials. The defining characteristic of these media is their incredible hardness and thermal stability. Unlike traditional metal media, which can degrade and contaminate the substance being milled, ceramic media maintain the purity of the materials by minimizing wear and tear.
The ceramic milling process offers unparalleled precision and consistency. In industries where material purity and structural integrity are critical, ceramic milling media such as alumina and zirconia stand out as ideal choices. Alumina ceramic media, for instance, is valued for its high corrosion resistance and cost-effectiveness, making it suitable for general-purpose milling. Meanwhile, zirconia media is preferred for its higher density and wear resistance, beneficial in more demanding milling conditions where achieving a finer grind is paramount.
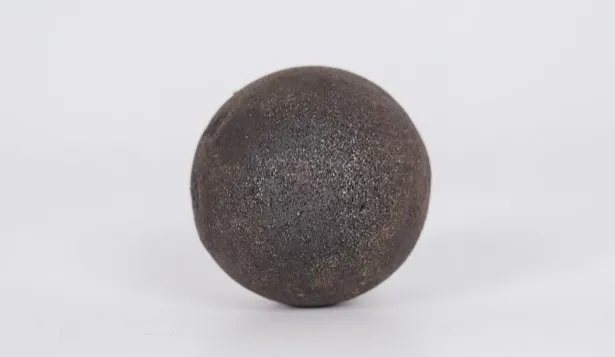
One notable experience comes from a pharmaceutical company seeking sterility and precision in drug formulation. They transitioned from stainless steel to zirconia milling media, resulting in significantly reduced contamination rates and improved bioavailability of their active pharmaceutical ingredients (APIs). By maintaining the integrity of the APIs, they not only enhanced product efficacy but also achieved considerable cost savings by reducing material wastage.
ceramic milling media
The technical expertise behind ceramic milling media stems from advances in material science. Unlike centuries-old metallic milling techniques, ceramic media manufacturing involves sophisticated processes such as isostatic pressing, followed by high-temperature sintering. This ensures high-density, homogeneous media with excellent mechanical properties. The expertise of material scientists and engineers plays a pivotal role in fine-tuning these processes, guaranteeing the reliability and durability of the final product.
Authorities in material science continue to explore innovative applications of ceramic milling media. Research and case studies widely acknowledge its ability to minimize energy consumption in milling processes. The efficiency gained from using ceramic media can lead to a reduction in operation costs and energy usage by up to 30%, a striking advantage for industries aiming to adopt more sustainable practices.
Trust in ceramic milling media extends from its proven track record across varied applications and its compliance with industry standards. Certifications such as ISO 9001 and FDA approval for pharmaceutical media underscore the reliability and safety of these products. Manufacturers of ceramic milling media are committed to continuous improvement, adhering to the highest quality controls and ensuring that their customers experience the full benefit of their investment.
In conclusion, the adoption of ceramic milling media embodies an intersection of advanced technology, economic efficiency, and sustainable practices. The experiences of industries utilizing these media demonstrate not only their superior performance but also their contribution to enhancing product quality and process sustainability. Expertise in this field assures continued innovation and application expansion, reinforcing the authoritative standing of ceramic milling media in today's high-tech manufacturing landscape. Businesses looking to optimize their milling processes should consider embracing this cutting-edge solution, not only to meet their current needs but also to prepare for future advancements in their respective domains.