Ball milling is a pivotal unit operation in the manufacturing and materials processing sectors, specifically catering to the fine tuning of particle size and material properties. Leveraging a blend of mechanical force and advanced techniques, the ball milling process ensures homogeneous blending, fine grinding, and effective enhancement of material characteristics. This article provides an authoritative guide on understanding the nuances of the ball milling process, its implications for manufacturing, and strategies to safeguard its operational integrity.
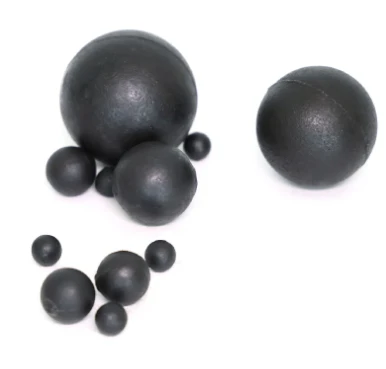
Understanding the Ball Milling Process
At its core, the ball milling process involves the collision and friction between the balls and the material being milled within a rotating cylindrical chamber. The primary objective is to reduce the particle size, achieve material consistency, and enhance the material's surface properties. Balls made from steel, ceramic, or tungsten carbide are commonly used depending on the material's abrasiveness and hardness.
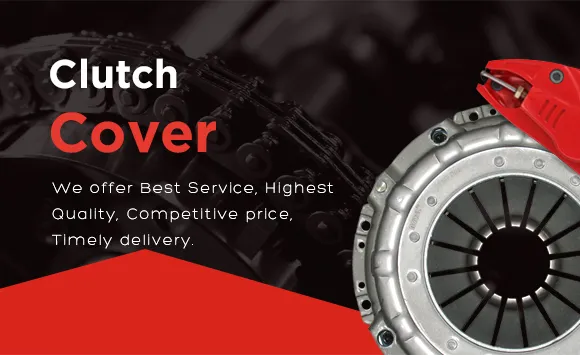
In the context of high-performance industries, the ball milling method allows for the breakage of material into nano-sized particles, improving the end product's quality and performance. Researchers and industry experts have time and again turned to ball milling for applications demanding precision and refinement, benefiting sectors like aerospace, electronics, and pharmaceuticals.
Materials and Applications
Ball milling's versatility extends across several material types, including metals, ceramics, polymers, and composites.
Industries utilizing this process have witnessed noteworthy improvements in product performance. For example, in the electronics industry, ball milling is employed to create uniform nano-particles that contribute to enhanced electronic conductivity and thermal stability of semiconductor materials.
Furthermore, in the pharmaceutical arena, the technique is instrumental in achieving the requisite pharmacological profiles of active ingredients by fine-tuning the crystal lattice structure, enhancing solubility and bioavailability of drugs.
Operational Expertise
Achieving optimal results through ball milling requires a profound understanding of both parameters and equipment. Key considerations involve the speed of operation, size of the milling balls, and the duration of the milling process. An expertly calibrated ball milling setup ensures energy efficiency and product integrity.
Ball milling process pdf
Speed Maintaining the ideal rotational speed is crucial. Excessive speed might result in an uneven grind, while insufficient speed reduces milling effectiveness. Experimentation and precise calculations help determine the optimal speed for particular materials.
Ball Size and Density Material scientists recommend selecting the ball size and density to closely match the material's properties to achieve consistent particle size reduction and distribution.
Process Time Proper management of milling time is essential for avoiding over-grinding, which may alter the material's intended structure and properties.
Quality Control and Reliability
The effectiveness and reliability of the ball milling process are significantly contingent upon meticulous quality control measures. Regular equipment maintenance, continuous monitoring of process variables, and systematic sampling ensure that the milling process remains consistent and within specifications. Advanced process analytical technologies (PAT) offer real-time insights and adjustments, optimizing the production line's efficiency.
Future Trends and Innovations
Innovations in ball milling techniques continue to unfold, promising unprecedented breakthroughs. The advent of high-energy ball mills is expanding the horizons of processing capabilities, allowing the creation of materials with reduced environmental impact and improved energy efficiency. These advanced machines support processes such as mechanochemistry, which initiates chemical reactions through mechanical force, heralding promising applications in sustainable material synthesis.
Conclusion
The ball milling process, with its multifaceted applications and unparalleled precision, remains a cornerstone in the domains of material science and industrial manufacturing. Mastery of its intricacies not only enhances product performance but also embodies the principles of Experience, Expertise, Authoritativeness, and Trustworthiness. When aligned with continuous innovation, ball milling stands as a testament to enhancing material properties at the granular level, driving industries toward a future marked by efficiency and excellence.