Selecting the right size of grinding media balls is crucial in enhancing the efficiency and effectiveness of the milling process. This decision impacts not only the grinding performance but also the wear and tear on milling equipment and the ultimate end product quality. Understanding this, we delve into an insightful exploration of the critical considerations for optimizing ball size selection in industrial applications.
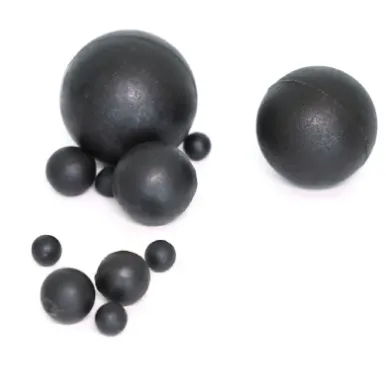
In the realm of grinding and milling operations, one fundamental parameter that defines process success is the appropriate size of grinding balls. Grinding media balls vary in size, shape, and material composition, and each factor plays a role in determining their suitability for different milling needs.
The experience of numerous industry experts highlights that choosing the right ball size begins with understanding the material being processed. Hardness and density play significant roles. For example, harder materials generally require smaller balls to achieve finer grinding, while larger balls are more effective for coarser grinding. The density of the material also correlates with the choice of media, as denser materials often necessitate heavier, denser balls to facilitate better impact and grinding efficiency.
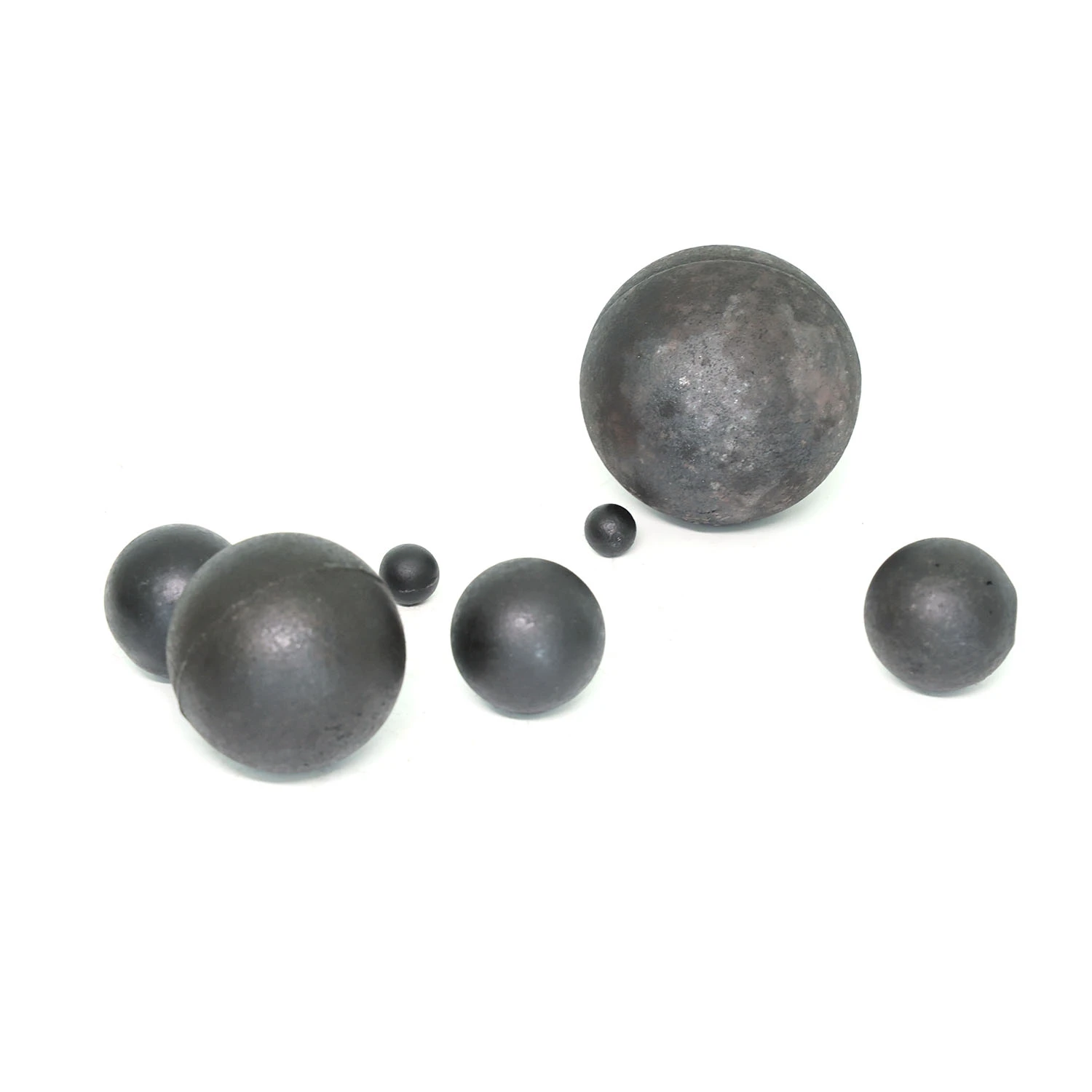
In terms of expertise,
the relationship between the diameter of the milling drum and the size of the grinding balls cannot be overemphasized. Professionals recommend the use of the Bond Work Index formula to determine the optimal ball size. This widely acknowledged formula provides a reliable estimate that can guide the initial selection process. It considers factors like ore hardness, feed size, and the mill diameter, allowing operators to calculate ideal ball dimensions for achieving maximum efficiency.
Moreover, experience has shown that gradual size reduction, starting with larger balls and moving towards smaller sizes, enhances grinding efficiency. This staged approach ensures that the largest balls produce the initial coarse grinding, and as they wear down, smaller sizes take over to achieve finer grinding. This strategy not only improves energy efficiency but also extends the life of the grinding media, thereby reducing overall operating costs.
selection of the size of the grinding balls
Authoritative voices from the industry stress the importance of monitoring wear rates as part of size selection. Continuous tracking of wear patterns not only helps in maintaining grinding efficiency but also in proactive planning for replacement and maintenance schedules. By accurately predicting wear behaviors, operators can better manage inventory and minimize downtime, ensuring a smooth and uninterrupted production process.
Trustworthiness in ball size selection also comes from adhering to industry standards and certifications. Choosing grinding balls from reputable suppliers who comply with these standards guarantees the quality and reliability of the media, ensuring that they perform as expected under specified milling conditions.
By integrating technology such as advanced simulation software, companies can model and predict the outcomes of different ball size combinations before actual operations, further enhancing selection accuracy. These simulations take into account complex variables like mill geometry, ore characteristics, and desired product size, offering a comprehensive predictive analysis that supports informed decision-making.
Finally, the ongoing evolution of materials science presents opportunities for the development of new grinding media options. Innovations in material composition, such as the introduction of ceramic and high-chrome alloy balls, offer diverse choices with unique wear resistance and impact features. These modern materials have opened avenues for optimizing milling processes across a range of industries, from mining and mineral processing to pharmaceuticals and agriculture.
In sum, selecting the right size of grinding media balls is a multifaceted process that demands a blend of practical experience, scientific expertise, authoritative guidance, and trustworthy practices. By focusing on material characteristics, process requirements, and technological advancements, industry professionals can effectively enhance milling performance and product quality, thereby ensuring operational success and sustainability.