In the dynamic world of cement manufacturing, every component plays a vital role in the efficiency and durability of the production process. Among these components, mill liners, or revestimientos para molinos de cemento, stand out as essential elements that ensure the smooth operation and longevity of the equipment. Professionals in the field recognize the impact that selecting the right liners can have, not only on production volume and energy consumption but also on the overall quality of the cement produced.
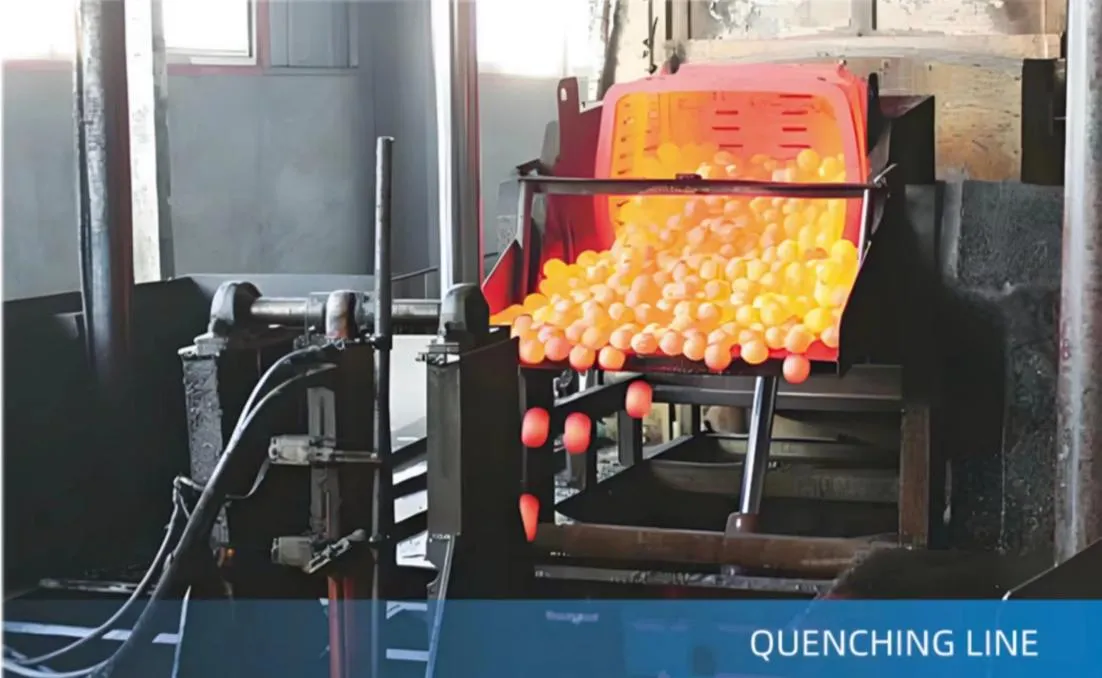
Innovations in mill liner technology have transformed not only the way cement is produced but also how plants operate and maintain this essential equipment. Advanced materials and designs have emerged from extensive research and practical experimentation in real-world conditions. As experts in the field have shown, the use of optimized mill liners can lead to significant improvements in efficiency and cost-effectiveness.
From a professional standpoint, understanding the technical intricacies and material science behind mill liners is crucial. The choice of material—whether it’s rubber, composite, or metal—directly influences their performance. Each type offers distinct advantages. For instance, rubber liners are preferred for their dampening properties and ease of installation. On the other hand, composite liners bridge the gap between metals' toughness and rubber's wear resistance, offering extended service life and reduced downtime.
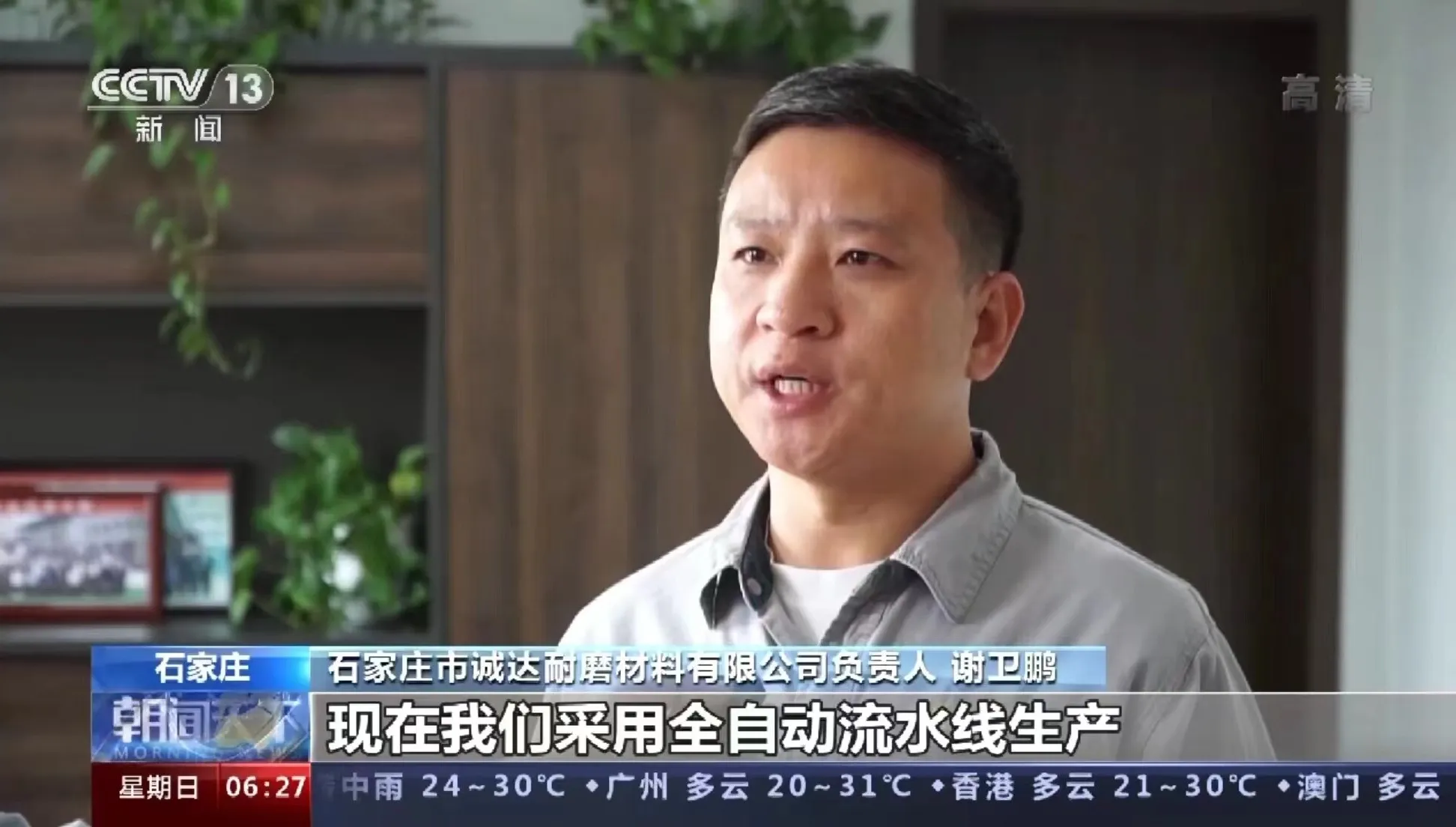
Cement plant operators often stress the importance of custom-designed liners. Unlike generic solutions, these tailor-made liners accommodate specific mill dimensions and material characteristics, enhancing the grinding process and minimizing energy losses. During the installation phase, precision alignment is crucial to prevent future issues like vibration or uneven wear that can significantly reduce the mill's lifespan.
The authoritative voices in cement production emphasize the role of quality control and regular monitoring. Liners, being at the frontline of the grinding process, must withstand varying levels of stress and impact. Regular inspections and maintenance schedules help detect signs of wear and tear early on, ensuring timely replacements and avoiding unscheduled plant stoppages.
Trustworthiness in this context is about relying on proven suppliers and manufacturers with a track record of quality and innovation. The market leaders often have documented case studies and testimonials that demonstrate their products' effectiveness across diverse operational scenarios. Selecting these tried-and-tested products reduces risks and boosts return on investment, as these liners are more capable of enduring harsh operational environments over extended periods.
revestimientos para molinos de cemento
From an experience perspective,
operators who have made the switch to more advanced liner systems report significant improvements. Commonly shared experiences include reduced energy consumption due to more efficient grinding processes and lower machine load. Moreover, these liner systems often contribute to better grinding media segregation, resulting in finer cement output at lower costs.
Incorporating insights from seasoned professionals is invaluable. Many point out that while the initial investment in high-quality liners might be higher, the long-term savings in maintenance and energy costs more than compensate for this initial expenditure. This accounts for why several plants are transitioning to state-of-the-art liner solutions despite budgetary constraints.
Scientific reviews in the realm of material science and engineering further attest to these findings. Studies indicate that modern liner designs incorporating computational fluid dynamics (CFD) and discrete element method (DEM) simulations are revolutionizing liner performance. These technologies allow for precise predictions of wear patterns and grinding efficiency, enabling manufacturers to refine designs that are optimal for both new installations and retrofit projects.
Ultimately, the decision to invest in top-tier mill liners is not merely about enhancing current operational efficiency—it's a strategic move towards future-proofing the cement manufacturing process against inevitable challenges. With the growing demand for environmentally sustainable and economically viable cement production, advanced mill liners present a viable path forward, ensuring that plants remain competitive while minimizing their environmental footprint.
In conclusion, whether you're guiding a state-of-the-art facility or looking to uplift an older plant's capabilities, paying heed to the evolving landscape of mill liner technology is crucial. These developments, backed by real-world testimonies, expert analysis, and authoritative research, underline the significant role that innovative mill liner solutions can play in the future of cement manufacturing.