The utilization of dry ball mills in industrial manufacturing processes represents a pivotal advancement in material refinement. These mills serve a critical function efficiently grinding materials to achieve precise particle sizes and optimal consistency, necessary for various applications across multiple industries. Users keen on enhancing their production efficiencies find dry ball mills an indispensable component of their equipment repertoire due to their superior performance parameters and customization capabilities.
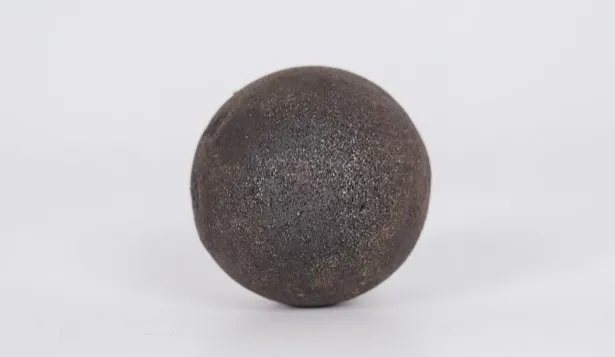
Engineered to meet the complexities of modern manufacturing processes, dry ball mills offer several tangible benefits. First, their design supports extensive materials processing, accommodating both hard and soft substances with prodigious ease. The result is a uniform particle distribution that significantly contributes to the improved quality and performance of the final product.
From a technical standpoint, dry ball mills distinguish themselves through their operational principles. They employ a tumbling action to grind materials, leveraging both impact and friction forces. This dual force application ensures that even heat-sensitive materials are processed without thermal degradation – a notable advantage over other grinding methods. Furthermore, dry ball mills require minimal maintenance and exhibit high operational reliability, fostering a low total cost of ownership over their lifespan.
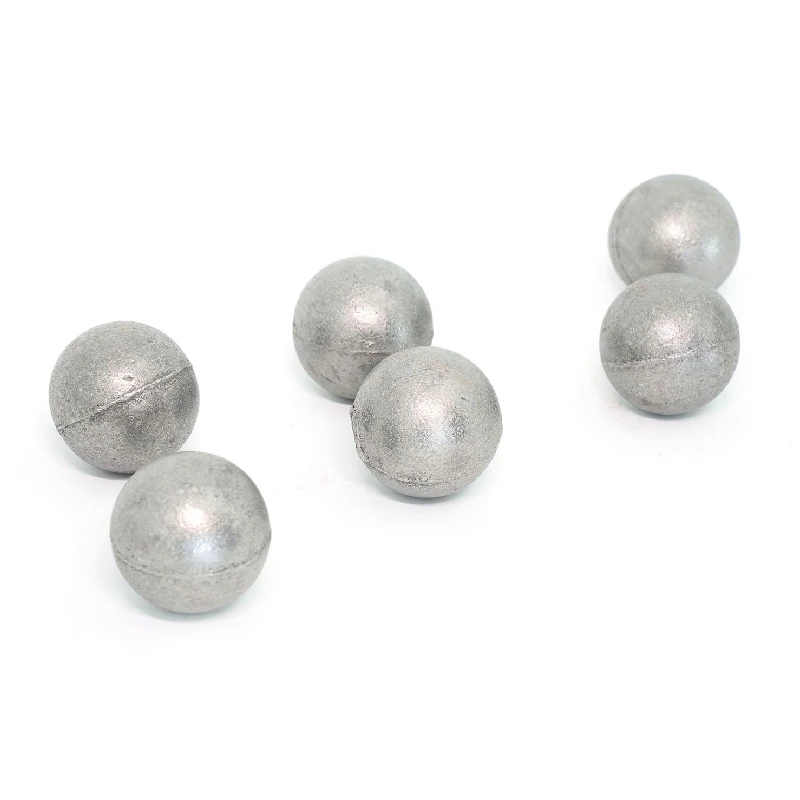
Expertise in the deployment and maintenance of dry ball mills is anchored in understanding the specific requirements of each application. Tailoring the mill's operation to the material's characteristics – such as hardness, moisture content, and temperature sensitivity – can drastically enhance the efficiency of the milling process. Professionals adept in optimizing these settings ensure that the equipment operates at peak capacity, further cementing the dry ball mill’s reputation for operational excellence.
For industries such as ceramics, minerals processing, and metallurgy, dry ball mills are transformative. They enable the precise production of powdered materials essential for diverse products, from advanced electrical components to high-quality ceramics. Their versatility extends beyond pure material processing; the mills also serve as vital research tools in laboratories, facilitating breakthrough innovations by allowing precise control over experimentation parameters.
Dry ball mill
Authoritative voices in engineering and manufacturing sectors often advocate for dry ball mills as the preferred solution for modern milling challenges. This endorsement is backed by numerous case studies illustrating successful integration of these mills into production lines, showcasing enhancements in both product quality and manufacturing efficiency. As a result, industry leaders who prioritize precision, sustainability, and scalability continually invest in updating their dry ball milling technology.
Moreover, trust in dry ball mills is solidified by their performance history and rigorous compliance with international quality standards. Organizations involved in their production and distribution often hold certifications from recognized bodies, providing customers with confidence in the equipment’s capability to meet stringent operational requirements.
In examining customer experiences, the consensus highlights the mill's ability to exceed expectations. Users report significant improvements in workflow efficiency and material quality, reinforcing the dry ball mill’s standing as an essential machine in sophisticated manufacturing ecosystems. Feedback-driven innovations over the years have further refined the mill’s design, augmenting its usability and ensuring that it remains at the forefront of technological advancement.
In conclusion,
dry ball mills stand as a testament to engineering functionality and adaptability. By satisfying the demand for consistent and precise material processing, they not only empower businesses to refine their production capabilities but also uphold the qualities of trustworthiness and reliability that are imperative for ongoing industrial success. With continuous advancements and committed industry support, dry ball mills epitomize the intersection of cutting-edge technology and practical application in the manufacturing landscape.