In the intricate world of industrial manufacturing and material processing, the selection of the appropriate milling media stands as a critical determinant of product quality and process efficiency. The process of choosing the correct size for grinding balls, often encapsulated under the term Auswahl der Mahlkugelgröße, is vital for a myriad of industries ranging from pharmaceuticals to ceramics and beyond. This selection process is not merely a matter of convenience or routine; it is a nuanced decision grounded in scientific principles and practical experience.
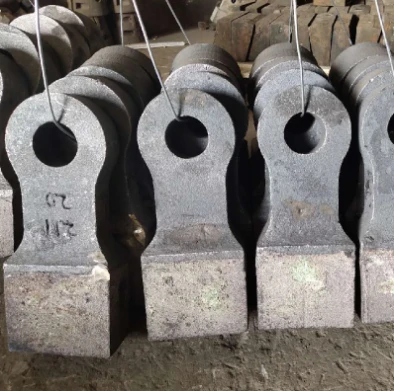
Choosing the correct size of grinding balls hinges on understanding the material characteristics and intended output. Larger grinding balls exhibit a higher impact force, making them suitable for coarser millings and initial processes where the primary goal is the breakdown of relatively large particles. However, this comes with the potential drawback of excessive wear on equipment and energy inefficiencies if not aligned with process requirements. Conversely, smaller grinding balls allow for finer milling and a greater surface area interaction, ideal for producing finer particles and achieving a homogeneous mixture in the substance being processed.
Material type plays a pivotal role in the selection process. Harder materials might demand larger, more robust grinding balls to efficiently break down particles without excessive wear and tear. On the other hand, more fragile substances can be more effectively processed with smaller grinding balls, minimizing the risk of damaging the structural integrity of the material. The practitioner must weigh material brittleness, hardness, and moisture content, among other factors, to ascertain the optimal ball size.
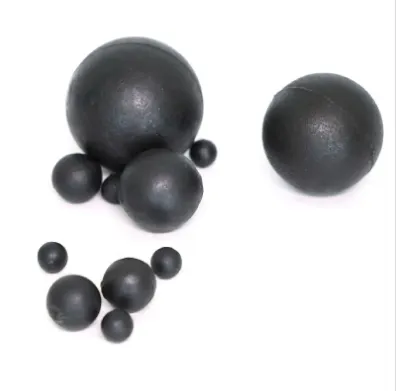
The expertise required to make these decisions is often rooted in extensive industry experience and academic knowledge. Professionals in this field typically have an in-depth understanding of material science and engineering principles and are adept at translating these into practical solutions for milling challenges. Moreover, industry experts often employ advanced simulation tools and empirical testing to validate their selections and refine processes, establishing a feedback loop that continually enhances efficiency and efficacy.
selection of the size of the grinding ball
Authority in this domain is generally demonstrated through a combination of scholarly publications, case studies, and real-world applications. Experts frequently share their findings through industry conferences and peer-reviewed journals, showcasing the latest research and development in milling technologies and media optimization. Such sharing not only underscores their authority but also aids in the collective advancement of industry practices.
Trustworthiness in the selection of grinding ball size is assured through adherence to industry standards and protocols. Many organizations are governed by regulatory standards that dictate material processing conditions and equipment specifications, ensuring consistent and reliable outcomes. Specialists in the field often prioritize stringent quality control and assurance regimes, providing clients and stakeholders with confidence in their processes and decisions.
Ultimately, the selection of grinding ball size, encapsulated by the Auswahl der Mahlkugelgröße, is far more than a procedural step—it is a critical component of product development and manufacturing strategy. Guided by expertise, authority, and trustworthiness, professionals navigate this complex terrain to optimize performance and ensure the success of their technological or industrial pursuits. Through continuous learning and adaptation, leaders in this field maintain the delicate balance between innovation and reliability, driving industry standards forward.