Grinding wheel tools, intricately designed and highly efficient, have become indispensable in the world of manufacturing, metalworking, and construction. Their role in shaping, cutting, and finishing materials with precision speaks volumes about their capability and relevance. This article explores the key aspects of grinding wheel tools, drawing upon expert insights and real-world experiences to highlight their significance in various industrial applications.
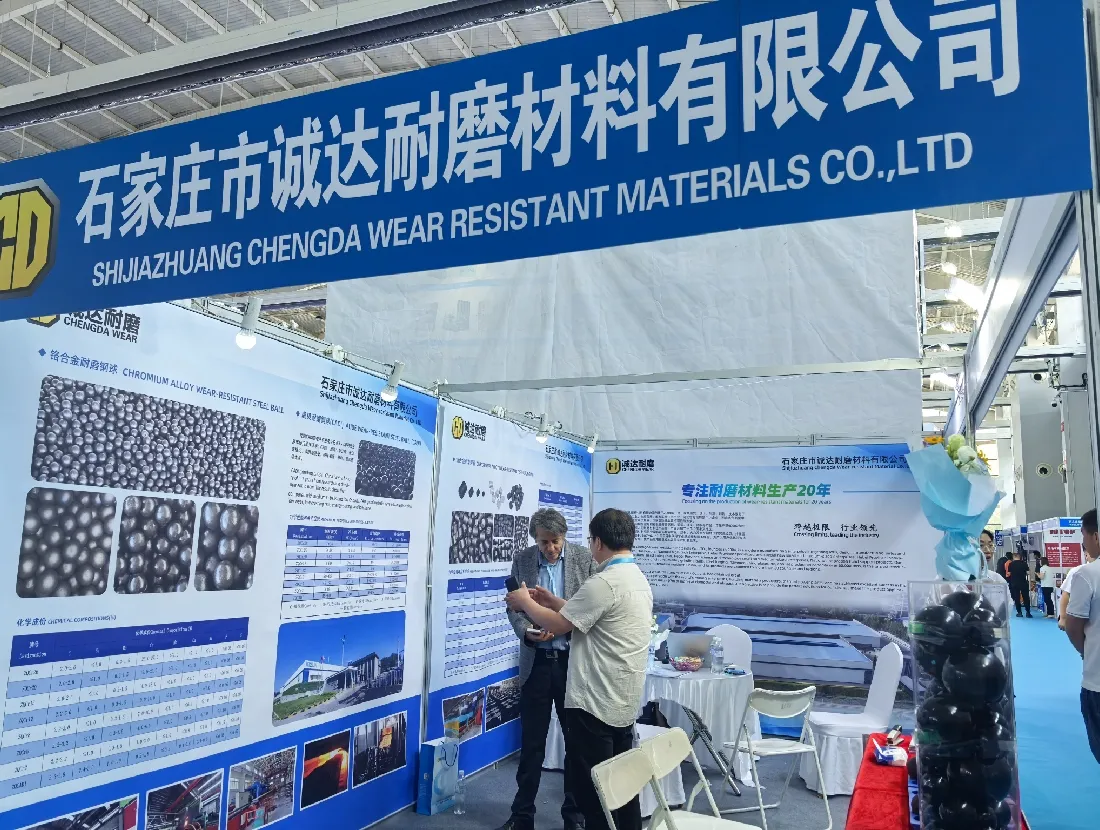
The design and construction of grinding wheel tools are a marvel of modern engineering. These tools are constructed from abrasive grains, bonded together to form a solid circular mass. The choice of abrasive grain—such as aluminum oxide, silicon carbide, or diamond—depends on the material they are intended to process. Each type of grain is selected based on its hardness and cutting ability, making the customization process crucial for optimizing performance across different materials.
The precision offered by grinding wheel tools is unparalleled. They are employed in scenarios where high accuracy is essential, such as in the automotive and aerospace industries. In these sectors, components must meet strict tolerances, and grinding wheels offer the quick material removal rate and fine surface finish required to achieve such high standards. Real-world application of these tools showcases their capability to enhance product quality, reduce production time, and ultimately contribute to operational efficiency.
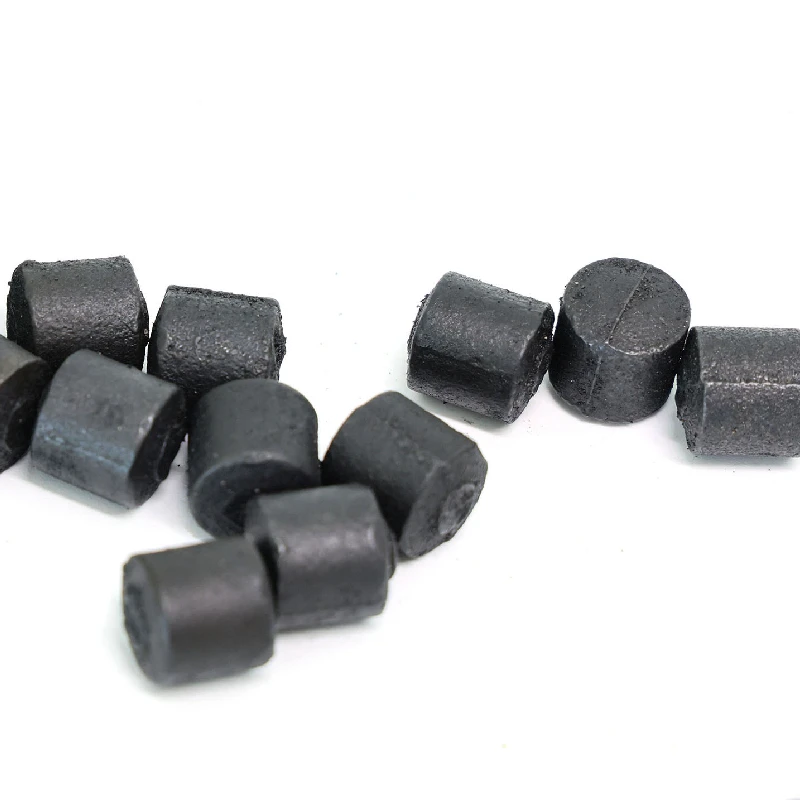
From a professional standpoint, selecting the right grinding wheel can significantly impact workflow and productivity. Experts emphasize the importance of considering factors such as wheel size, abrasive material, and bond type. For example, a vitrified bond is suitable for precision work due to its rigidity, while a resin bond offers more flexibility for rough grinding. Professionals in the field leverage their expertise to choose the perfect tool to suit specific tasks, ensuring optimal results and equipment longevity.
Furthermore, authoritative voices in the industry underline the necessity of adhering to safety standards when using grinding tools. The high-speed rotation of these wheels poses potential hazards, and compliance with safety guidelines is paramount to prevent accidents. Training and experience play crucial roles in the effective and safe operation of these tools. Trustworthy operators take the time to understand the machinery, wear personal protective equipment, and follow established procedures, thus maintaining a safe working environment.
Grinding worker
Upkeep and maintenance are also significant factors contributing to the long-term performance and reliability of grinding wheel tools. Regular inspection for wear and damage can preemptively identify issues that may compromise safety or efficiency. Experts advocate for routine maintenance schedules, aligning them with manufacturer recommendations and industry best practices. Proper handling, including correct storage and avoiding exposure to moisture or extreme temperatures, safeguards the integrity of the grinding wheels, thereby extending their lifespan.
Innovations in material science have further propelled the advancement of grinding wheel technology. The incorporation of cBN (cubic boron nitride) and polycrystalline diamond has expanded the capabilities of these tools to address the evolving demands in advanced manufacturing. High-performance grinding wheels equipped with these materials allow for remarkably high cutting speeds and improved resistance to wear, making them an excellent choice for tackling difficult-to-machine materials.
The real experiences of companies using grinding wheel tools illustrate their transformative impact on operations. By adopting advanced grinding technologies, manufacturers report improved surface finishes, reduced waste, and increased production yields. The competitive edge provided by these tools drives innovation and operational excellence, underscoring their pivotal role in modern industrial processes.
In conclusion, grinding wheel tools, revered for their precision, reliability, and versatility, continue to drive advancements in numerous industries. Their capability to precisely shape materials coupled with a profound understanding of their application empowers industries to push the boundaries of what is possible. Guided by expertise and meticulous attention to safety and maintenance, these tools are a testament to the enduring quest for quality and efficiency in the worlds of manufacturing and beyond.