Liner plates are crucial in a variety of industries due to their role in providing structural support and protection. These components are found in multiple applications, including mining, construction, and manufacturing, and understanding the different types is vital for selecting the right product for any given use.
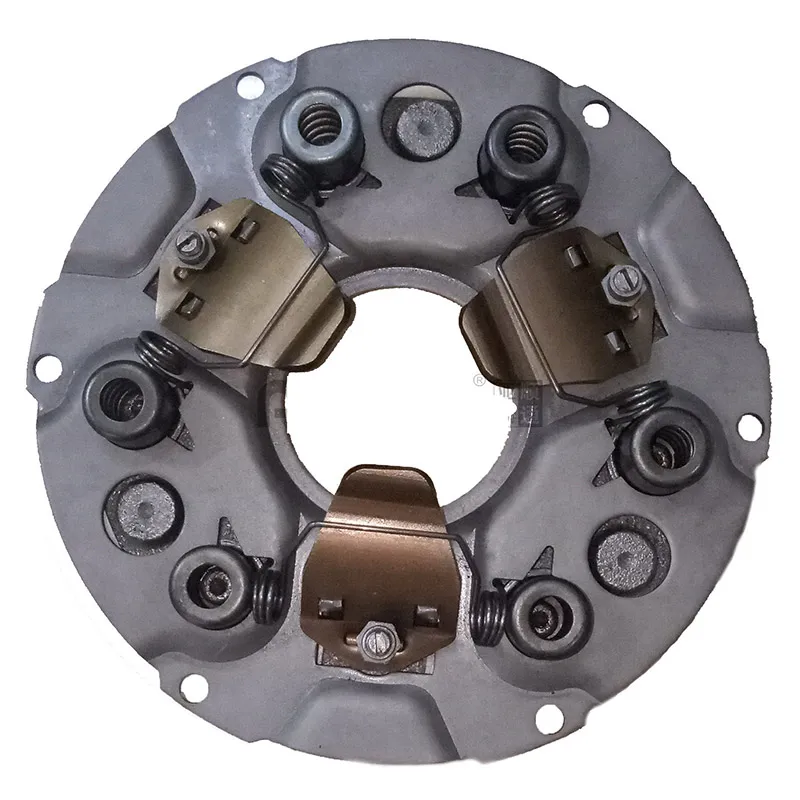
The first type of liner plate is the corrugated steel liner plate. Known for its exceptional strength and flexibility, corrugated steel is often used in environments where both durability and adaptability are crucial. The undulating design not only sheds water efficiently but also provides superior reinforcement to structures by distributing weight and pressure more evenly. This type of liner plate is commonly used in tunneling projects where unstable soil conditions require robust support systems. Furthermore, it is often coated with anti-corrosion layers to extend its lifespan in harsh environments, making it a preferred choice for underground applications.
Polyurethane liner plates offer a contrasting profile, recognized for their lightweight properties and superior abrasion resistance. Polyurethane liners are prominently used in industries where significant wear and tear occurs due to constant material flow over surfaces, such as in hoppers and chutes in the mining industry. Their ability to withstand high-impact forces without degrading makes them an efficient long-term choice, especially in operations where downtime can critically affect productivity. Additionally, their installation and maintenance are comparatively straightforward, reducing operational costs over time.
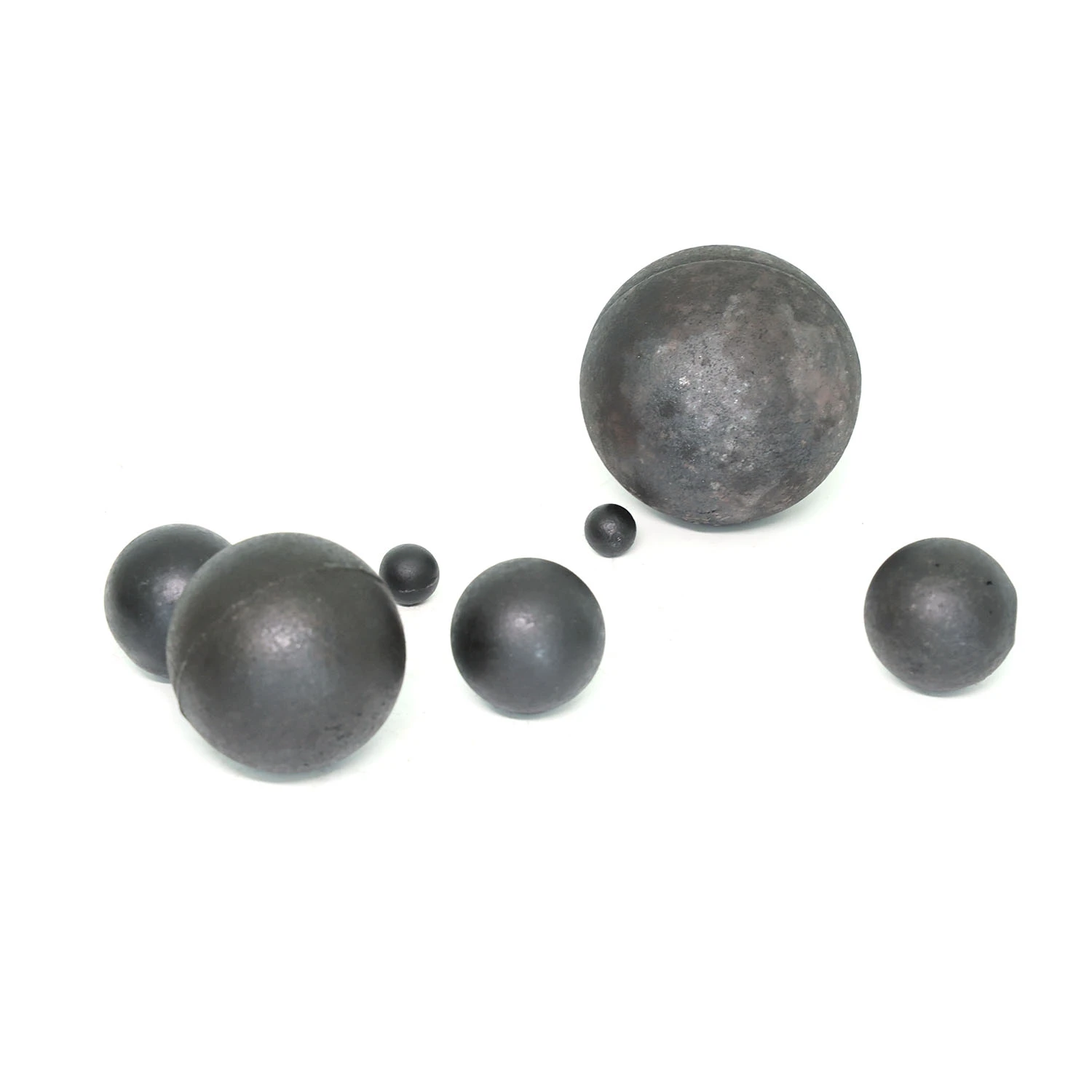
Ceramic liner plates are another popular choice, particularly valued in industries where extreme friction and corrosion present persistent challenges. Their composition of high-alumina ceramics gives them remarkable hardness and a smooth surface, helping reduce damage from abrasive materials. Ceramic liners are especially common in power generation and mining industries, where equipment faces constant wear from abrasive particles. Due to their high durability, ceramic liners significantly decrease the frequency of replacements and repairs.
Rubber liner plates are often employed in environments where noise reduction is necessary, aside from protecting against physical wear. These liners are notable for their ability to dampen sound while providing good resistance against impact and corrosion. Thus, they are frequently used in the manufacturing sector where equipment noise can be overwhelming. Additionally, rubber liners are an excellent choice for applications where kinetic vibrations could lead to equipment damage, helping extend the lifespan of machines.
types of liner plates
Composite liner plates represent a modern advancement in materials engineering, combining various substrates to optimize different properties needed in diverse applications. Often, these liners merge metal with rubber or ceramics, creating a hybrid that leverages the strengths of each material. Composite liners are tailored for situations where specific challenges—such as intense heat and corrosive materials—must be managed simultaneously. They are often custom-designed to meet unique operational requirements and can be adapted to fit a vast array of equipment types, offering versatile solutions across industries.
The selection of liner plates fundamentally hinges on an in-depth understanding of the operational environment and the specific challenges faced. For example, mining operations involving frequent abrasive materials benefit from the hardness of ceramic liners, while sectors prioritizing lightweight yet durable solutions might find polyurethane liners more advantageous. Furthermore, considering factors such as cost, expected lifespan, ease of installation, and maintenance can significantly influence the choice of liner plates.
Professionals recommending or utilizing liner plates should stay informed about innovations in materials technology and manufacturing processes that continually evolve to enhance performance and efficiency. This proactive approach not only boosts the reliability of their solutions but also builds trust among clients and stakeholders who rely on their expertise.
When researching and implementing liner plates in operational contexts, relying on empirical data gathered from real-world applications will enhance the decision-making process. Collaborating with industry experts and manufacturers who specialize in liner plate technology ensures access to the latest advancements and best practices. Whether replacing, upgrading, or designing from scratch, understanding the specific attributes and advantages of each liner plate type is pivotal to successful application and will drive optimal results in operational performance.
In conclusion, the diverse types of liner plates—from corrugated steel to advanced composites—offer tailored solutions for various industrial applications. Selecting the right type requires careful consideration of the operational environment and demands a commitment to continuous learning about emerging trends and innovations in materials science. This strategic approach enhances not only productivity and efficiency but also builds a foundation of reliability and trust in the solutions provided.