High manganese steel, commonly referred to as 14 Manganese Steel or Hadfield steel, is renowned in the industrial world for its unparalleled properties that make it a preferred choice in harsh and demanding applications. This steel variant, which typically contains 12-14% manganese, is known for its unique ability to work harden under stress, which significantly enhances the wear resistance of materials made from it. The adaptability and durability of 14 Manganese Steel have cemented its place in industries such as mining, railway, and heavy machinery.
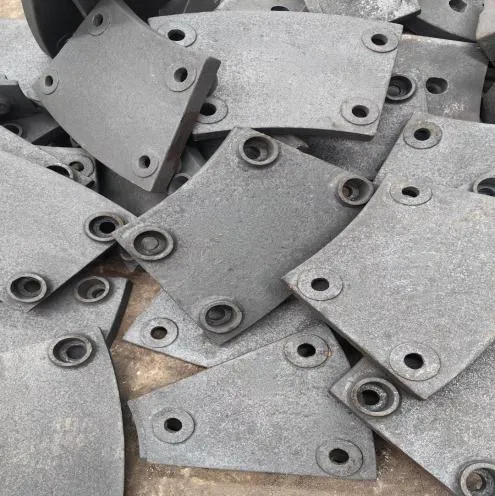
The primary advantage of 14 Manganese Steel lies in its work-hardening capability. Unlike most steels, which may become more brittle when hardened or exposed to stress, 14 Manganese Steel thrives under extreme conditions. When subjected to impact or strain, the steel undergoes a transformation in its surface layer, becoming incredibly hard while maintaining a tough and ductile core. This combination ensures maximum resistance to abrasion and extends the lifespan significantly beyond that of ordinary steel.
In terms of expertise, the integration of 14 Manganese Steel into manufacturing processes demands a deep understanding of its properties and behavior. Notably, industries that process wear-resistant parts appreciate the peculiarity of 14 Manganese Steel in situations involving repeated impact and high-pressure abrasives. Engineers and metallurgists often highlight its utility in crafting components such as excavator bucket teeth, crusher jaws, and railway points and crossings. Each application leverages the steel's ability to endure environments where lesser metals would suffer accelerated degradation.
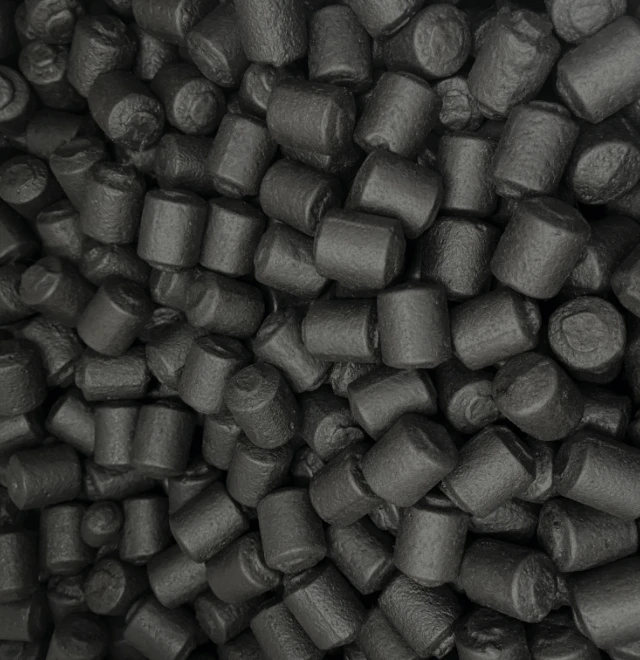
Authoritativeness is further established through case studies from leading mining companies, who have periodically replaced standard steel components with those made from 14 Manganese Steel, noting a significant reduction in operational downtime. For instance, a renowned mining firm documented that the switch resulted in a 30% increase in operational efficiency over a three-year period, confirming the material's long-term cost-effectiveness. Such endorsements from the industry not only substantiate the acclaimed durability of 14 Manganese Steel but also confirm its critical role in enhancing business operations.
14 manganstahl
Trust in 14 Manganese Steel is also derived from its proven track record in safety-critical applications. The railway industry, tasked with ensuring the highest safety standards, routinely utilizes this material in trackwork components. The material's robustness ensures both reliability and low maintenance, minimizing the risk of failures that could otherwise cause substantial service interruptions. Similarly, the material's non-magnetic properties make it suitable for applications near sensitive electronic equipment, where magnetic interference could pose issues.
As industries continue to evolve, the demand for materials that can withstand increasingly challenging environments grows. 14 Manganese Steel stands ready to meet these needs, boasting attributes that few materials can match. Its adaptability not only makes it relevant for current applications but also positions it as a material of choice for future innovations, embracing an era where longevity and reliability form the cornerstone of industrial advancement.
In conclusion, choosing 14 Manganese Steel is an investment in performance and reliability. For companies looking to optimize their operational efficiency and longevity, understanding and integrating this versatile material into their infrastructure symbolizes a commitment to harnessing the best that material science offers. Only through continued research, insightful application, and strategic implementation, can industries fully tap into the transformative capabilities of this remarkable steel.