Wear-resistant plates are revolutionizing industries where equipment faces severe wear and tear. Manufacturers of these specialized products understand the critical need for durability and longevity in rigorous environments. Such plates, often constructed from steel alloys and infused with compounds like tungsten carbide, provide unparalleled resistance to abrasion and impact. This makes them indispensable in sectors such as mining, construction,
and manufacturing.
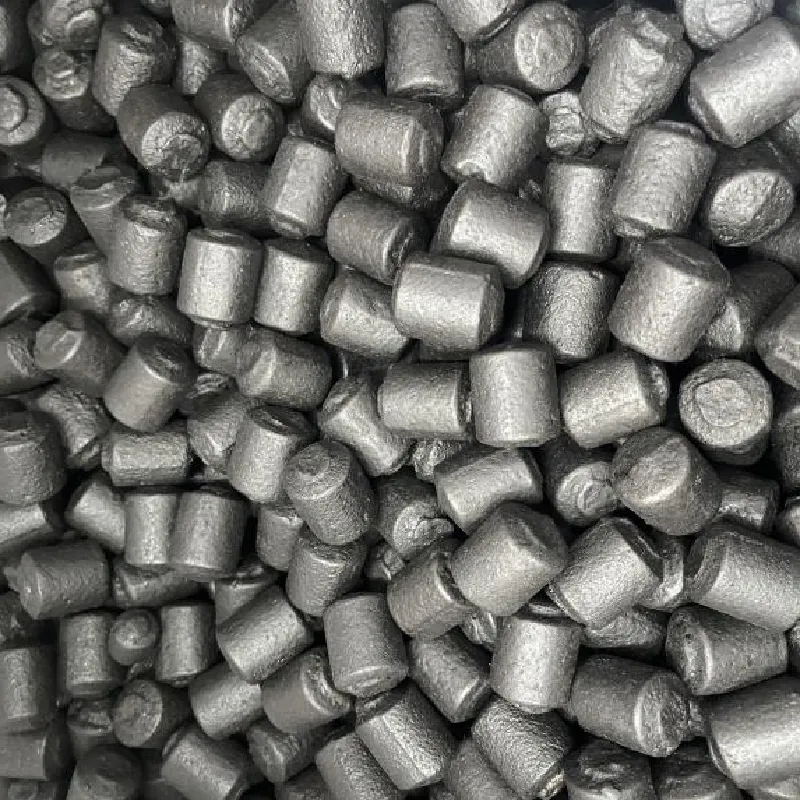
Expert manufacturers leverage advanced metallurgical techniques to enhance the durability of their wear plates. This includes processes like quenching and tempering, which refine the microstructure of the steel, significantly boosting its tensile strength and toughness. These enhancements ensure the plates can withstand harsh operating conditions, reducing downtime and maintenance costs for end-users.
Industries utilize wear-resistant plates primarily in situations where equipment parts repeatedly come into contact with abrasive materials. For example, in the mining sector, heavy machinery like excavators and dump trucks are constantly exposed to rocks, sand, and other abrasive substances that can quickly wear down standard steel. Implementing wear-resistant plates in these machines drastically extends their operational life, making them a cost-effective investment over time.
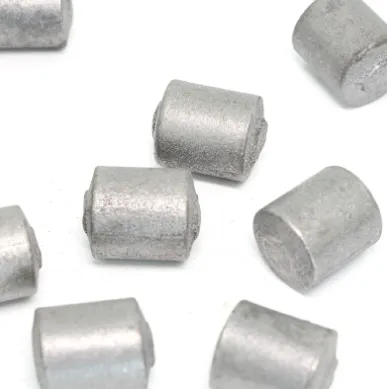
Companies like SSAB, Hardox, and Dillinger are leading the charge in wear plate innovation. They have developed proprietary materials that not only resist wear but also offer ease of fabrication. This is crucial for manufacturers needing to cut, weld, or otherwise customize the plates for specific equipment or operations. Their commitment to research and development ensures that their products consistently meet the evolving demands of the market.
производители износостойких пластин
Quality assurance is a non-negotiable priority among reputable wear-resistant plate manufacturers. Rigorous testing protocols are employed to certify that each plate meets stringent industry standards. This includes hardness testing, impact testing, and real-world simulations to verify performance under expected operational stresses. Such testing fosters trust with consumers, providing a strong assurance of product reliability.
Industrial players looking to integrate wear-resistant plates into their operations often seek comprehensive consultation services offered by top-tier manufacturers. These services include needs assessments, material selection advice, and after-sales support, which are critical in optimizing product performance and ensuring correct application. This expert guidance assures clients that they are making informed choices tailored to their unique operational requirements.
Sustainability is also increasingly prominent in the production of wear-resistant plates. Manufacturers are actively seeking ways to minimize environmental impact through the use of recycled materials and innovative production techniques that reduce energy consumption. This eco-conscious approach not only addresses global sustainability concerns but also aligns with the values of forward-thinking businesses aiming to reduce their carbon footprint.
Incorporating wear-resistant plates into industrial applications represents a strategic move to enhance performance, prolong equipment life, and increase operational efficiency. Their deployment translates to significant cost savings in maintenance and reduced downtime, positioning businesses for greater competitive advantage. As industries continue to evolve, the role of these plates will only become more integral, solidifying their place as a cornerstone in the future of industrial innovation.