Forged grinding balls stand as indispensable tools in the mining and cement industries, where precision and durability are paramount. These balls, crafted from carbon steel or stainless steel, undergo a meticulous forging process that enhances their mechanical properties, ensuring optimal performance in diverse grinding applications.
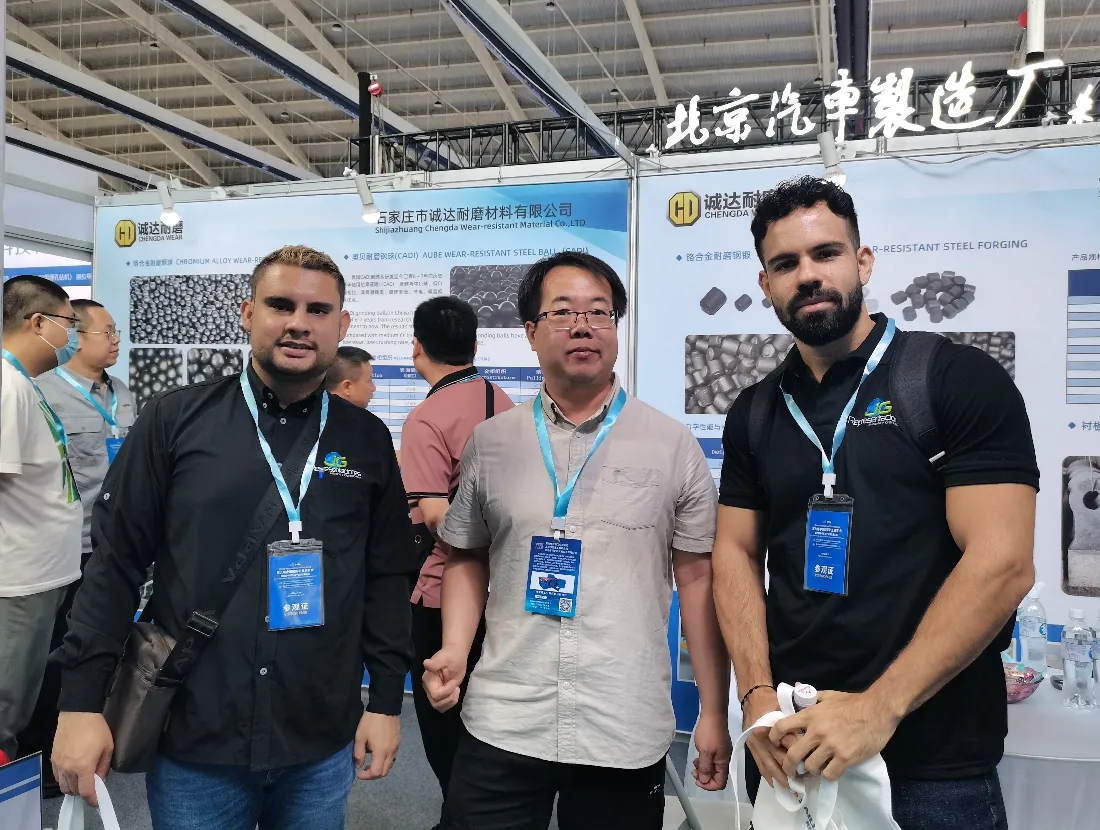
Industries demand tools capable of withstanding extreme pressure and wear, and here forged grinding balls excel. Through the forging process, these balls boast a uniform grain structure, enhancing their tensile strength and resistance to impact and wear. This ensures a longer lifespan compared to cast balls, reducing frequent replacements and contributing to operational efficiency.
The expertise in the manufacturing process is crucial. At its core, forging involves heating metal blanks to a pliable state before shaping them into balls under high pressure. This process not only refines the microstructure of the metal but also eliminates internal defects, resulting in a product that can endure harsh grinding environments. The precision engineering involved attests to the expertise required in this field, ensuring each ball meets stringent industry standards.
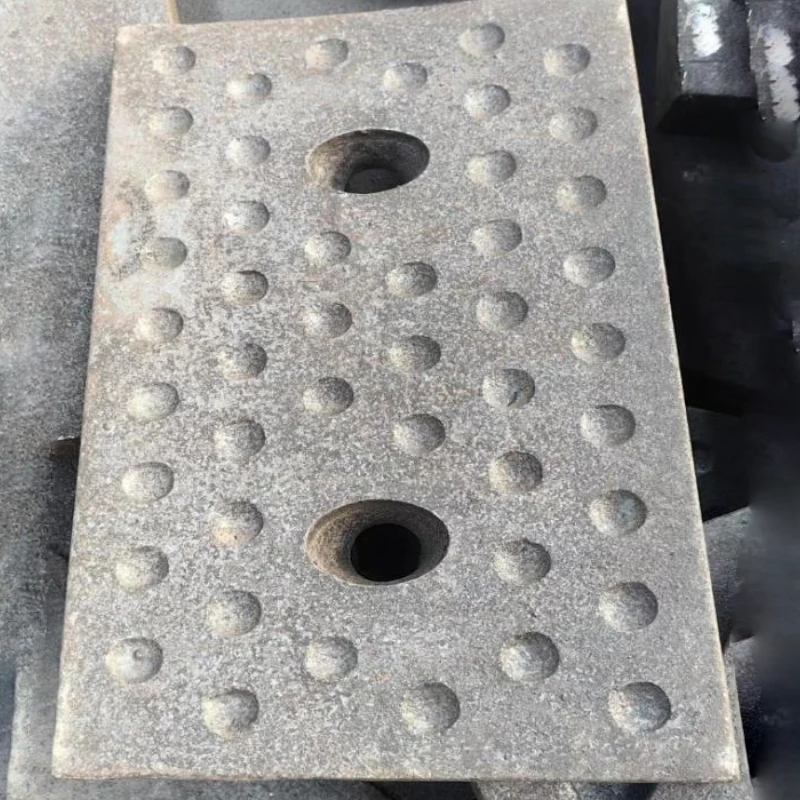
The authoritative nature of forged grinding balls stems from their widespread adoption and proven track record in various industries. Mining operations, in particular, rely heavily on these balls to crush and grind raw ore into finer particles, facilitating further processing. Many leading companies have documented improvements in grinding efficiency and output quality after switching to forged options, establishing these balls as trusted components in the industry.
кованые мелющие шары
Trustworthiness, a cornerstone of any reliable product, is evident in the traceability and quality control measures integrated into the production of forged grinding balls. Manufacturers often adhere to international standards such as ISO 9001, ensuring that every batch is subject to rigorous testing protocols. Such commitment to quality assures users of the consistency and reliability of the balls, thereby safeguarding personal and business investments.
The real-world experiences of users further emphasize the indispensability of forged grinding balls. Operators often report a marked reduction in operational downtime and maintenance costs due to the enhanced durability of these tools. Additionally, their uniform hardness and superior wear resistance translate to consistent mill performance, optimizing productivity and reducing energy consumption over time.
As the market evolves, technological advancements in manufacturing, such as the integration of automated forging lines and real-time quality monitoring systems, continue to enhance the properties of forged grinding balls. These innovations not only improve efficiency but also open new avenues for customization, catering to specific industry needs and further establishing these balls as leaders in their field.
Investing in forged grinding balls is not merely a product choice but a strategic decision to improve operational longevity and efficiency. Their unparalleled strength, durability, and reliability make them an optimal choice for industries where performance cannot be compromised. Embracing this technology is a testament to a company’s commitment to quality, efficiency, and long-term success.