Grinding balls play a critical role in mining and cement industries, being indispensable elements in milling processes. Their efficiency in reducing particle size profoundly impacts operational productivity, making an understanding and selection of these components imperative.
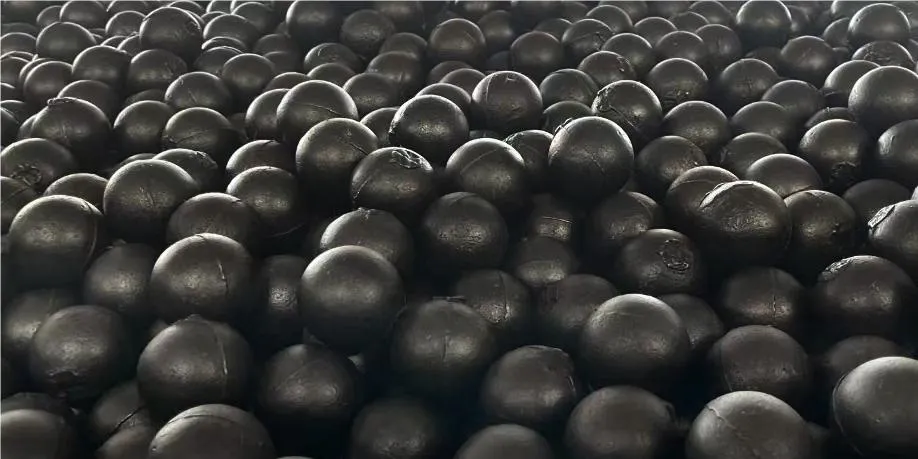
Quality and durability of grinding balls remain non-negotiable. The manufacturing process involves casting, forging, and rolling, each with distinctions in wear resistance and impact toughness. Forged steel balls are celebrated for their resilience in high-impact applications, providing longevity that translates into tangible production efficiencies. Furthermore, the production techniques emphasize an optimized metal grain structure, minimizing potential weak points susceptible to wear.
Accurate material selection is paramount. Typically, grinding balls comprise carbon steel, chrome steel, and stainless steel, each offering unique benefits. Carbon steel is pragmatically used for its cost-effectiveness, while chrome variants exemplify hardness and anti-wear properties. Stainless steel is the champion where corrosion poses substantial risks, safeguarding machinery and extending service life through consistent performance.
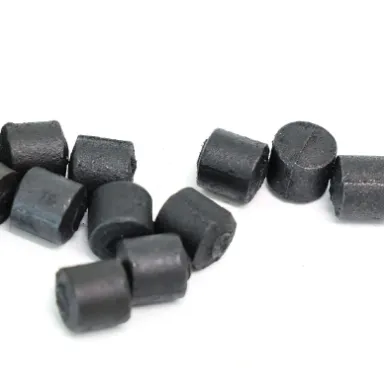
Valuable insights come from real-world experiences in optimizing milling conditions. The choice of ball size and density can profoundly alter milling outcomes. For instance, larger diameter balls are often preferred for crushing coarser particles, while smaller sizes excel in achieving fine milling results. The equilibrium between feed size and output requirements guides these meticulous choices, enhancing process efficiency and product consistency.
мелющие шары
Specialized coating technologies have emerged as a game changer. By mitigating abrasion and chemical attack, coatings significantly extend the lifespan of grinding balls. This innovation results in lower operational costs and enhanced trust in process stability amongst industry stakeholders. Legitimate expertise in this area provides competitive advantage by tailoring solutions specific to operational challenges faced by industrial players.
Moreover, authoritative training and meticulous data analysis fortify the selection and usage strategy of grinding bodies. This specialized guidance elevates the strategic application of grinding media, aligning with environmental stewardship by enabling judicious material use and reducing waste. Sound adherence to industry standards and regulations further instills confidence, defining the supplier as a reliable partner in the value chain.
In summation, the judicious choice of grinding balls influences every facet of milling operations. Reliable performance, robust design, and technological advancements foster an environment of operational excellence. Commitment to innovation, followed by transparent communication of advantages, underpins a relationship built on trust and expertise. Future-forward thinking, coupled with sustainable practices, enhances not only the efficacy of grinding operations but also affirms an ethical stance on global industrial impact.