Grinding balls are the unsung heroes in the mining industry, playing a crucial role in ore processing and extraction. For those who have ventured into this sector, the experience of selecting and utilizing the right grinding media can profoundly impact operational efficiency and output quality. Understanding the intricacies of grinding ball mining is essential for anyone looking to optimize production and ensure sustainability.
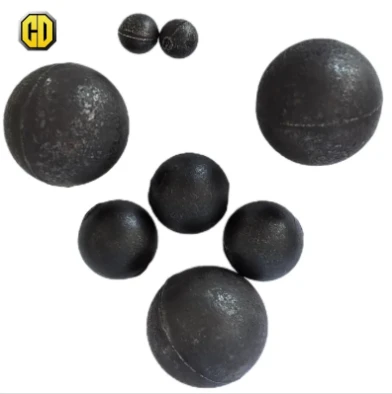
In any mining operation, the quality of the equipment used directly influences the quality of the work done. Grind media, particularly grinding balls, are paramount in the size reduction process. They ensure that the ore is finely ground to unlock the valuable minerals for subsequent processing. When choosing grinding balls, experience shows that factors such as material composition, hardness, and size can significantly affect milling efficiency and cost-effectiveness.
Experts in mining emphasize that the composition of grinding balls is critical. They are typically made from steel, alloyed steel, or cast iron. The choice often depends on the specific requirements of the milling process. Steel grinding balls, for instance, are prized for their durability and cost-effectiveness in hard rock applications. On the other hand, alloyed variations might offer better wear resistance, extending the lifespan of the milling equipment and reducing downtime.
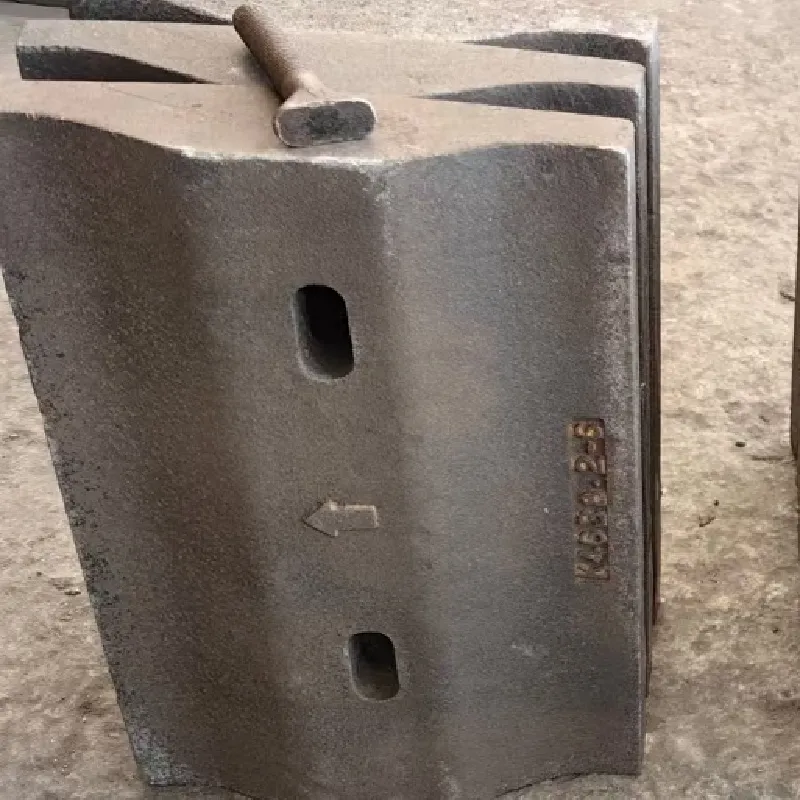
Another expert insight revolves around the importance of hardness. The grinding process involves a series of heavy impacts on materials. Balls with adequate hardness will withstand these forces and maintain their shape and size over time. Thus, they reduce the rate of ball consumption and overall operational costs. However, excessively hard balls can be brittle and prone to breaking. Striking a balance between hardness and toughness is critical, necessitating a deep understanding of metallurgical principles and wear mechanics.
Size selection of grinding balls is equally vital. The general rule of thumb within the industry is to match the ball size to the size of the grinding material. Larger balls are suitable for breaking down larger chunks of ore, while smaller ones are better for finer tasks, providing a more uniform particle size in the output. This size optimization not only enhances the grinding efficiency but also aids in reducing power consumption, highlighting another layer of expertise required in the decision-making process.
Grinding Ball Mining
The authority of a reliable supplier cannot be understated when procuring grinding balls. Trustworthiness in this context is built on transparency about product specifications, consistent quality, and reliable delivery schedules. Collaborating with manufacturers with a proven track record can help minimize risks associated with variable grinding ball performance, which can lead to production inconsistencies.
Within the grinding ball mining sector, the real-world experience further underscores the necessity of regular testing and monitoring of the balls during operation. Experts recommend periodic inspections to gauge wear patterns and determine when balls need replacement or reordering. This proactive approach ensures that the milling process remains uninterrupted and efficient.
Moreover, some industry veterans advocate for the use of simulation software to predict performance outcomes and optimize ball selection before purchasing. These advanced tools utilize algorithms that consider multiple variables, providing miners with a strategic advantage in their grinding operations.
In conclusion, the world of grinding ball mining is steeped in expertise and demands authoritative knowledge to navigate successfully. Experience and trust are the cornerstones of effective grinding media selection, underpinned by a commitment to professional engagement with the latest technological advancements and a keen focus on material science. As the industry continues to evolve, staying informed and adapting to new innovations is the pathway to maintaining a competitive edge in ore processing and extraction activities.