Mastering the Milling Ball An Expert's Insight into Selection, Use, and Maintenance
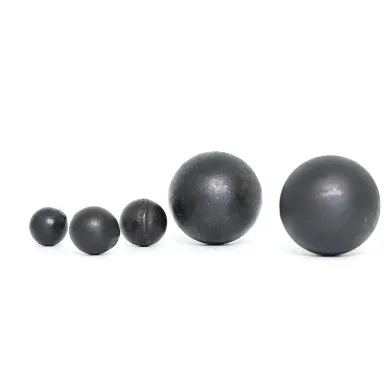
In the world of manufacturing and material processing, the milling ball serves as a cornerstone tool in the milling, grinding, and pulverizing processes. With applications reaching as far as pharmaceuticals, mining, and metal fabrication industries, the meticulous selection and use of milling balls can significantly impact operational efficiency and product outcomes.
To fully harness the potential of milling balls, understanding their core functionalities and mechanics is essential. Milling balls come in various materials, including steel, ceramic, and carbide. Each type offers distinct benefits suitable for specific applications. Steel milling balls, known for their robustness, are most suitable for grinding hard materials due to their excellent durability. Ceramic milling balls, on the other hand, boast resistance to acid and alkali, making them ideal for chemical preparations. Carbide milling balls can withstand extreme temperatures and pressures, offering superior precision in highly technical applications.
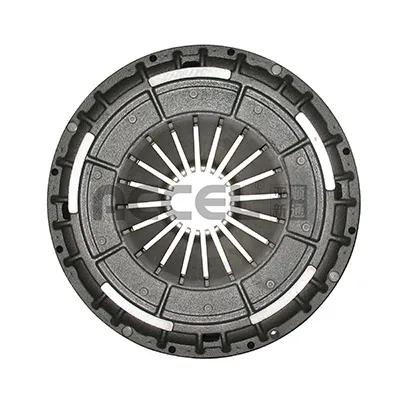
The size and weight of a milling ball are crucial determinants of its effectiveness. Optimal size and weight ensure maximum energy transfer during the milling process, thus reducing time and increasing the efficiency of material comminution. Selecting the proper dimensions requires an understanding of material characteristics and grinding requirements. A size too large may lead to improper grinding, while too small a size may result in prolonged processing times.
An expert approach to utilizing milling balls involves the careful calibration of these variables to strike a balance between energy consumption and material fineness. For instance, maintaining a high ball-to-powder ratio enhances the kinetic energy transfer, expediting the milling process. A typical rule of thumb within the industry recommends this ratio be kept around 101 for ideal outcomes.
Milling ball
Manufacturers are advised to consider the rotational speed at which milling balls operate. The velocity should facilitate the cascading motion of the balls within the mill, ensuring comprehensive and effective contact with the material. A speed that is too high risks a centrifugal motion where balls stick to the inner walls, whereas too low may lead to suboptimal grinding.
Calculating the critical speed, therefore, becomes indispensable. It enables users to unlock the optimal speed for the particular mill size and material, ensuring peak operational efficiencies.
Equally critical is the maintenance of milling balls to preserve their lifespan and functionality. It is recommended that regular check-ups be scheduled to assess wear and tear, particularly in high-volume milling operations. Employing a systematic approach for inspecting milling equipment for surface imperfections can prevent unexpected operational delays. Professionals advocate for replacing balls that showcase significant wear to ensure the precision and efficiency of the milling process are not compromised.
Trustworthiness in utilizing milling balls extends to ensuring safety protocols are strictly observed. Whether considering dust discharge systems or vibration dampening structures, safeguarding operations from potential hazards associated with high-intensity milling environments is paramount. Adopting necessary protective measures around the operations can mitigate risks traditionally associated with mechanical breakdowns or hazardous spillovers.
To conclude, the comprehensive selection, application, and maintenance of milling balls evoke a delicate balance of expertise and industry insight. The nuanced understanding of materials, parameters, and processes can drive operational excellence and innovation in material processing. For businesses aiming to stay ahead of the curve, embracing advanced techniques and continuous learning around milling ball technology offers a distinct competitive edge over their contemporaries.
Through strategic planning infused with experience, authority, and trust in their milling practices, manufacturers can achieve superior precision, enhanced product quality, and reduced processing time, establishing themselves as industry leaders in efficiency and reliability.