The sphere grinding process, referred to as 구형 볼 연삭 in Korean, plays a pivotal role in the realm of machining, providing precision shaping and finishing of spherical components. This procedure is integral to industries that demand highly accurate, perfectly round components, such as aerospace, automotive, and precision engineering sectors.
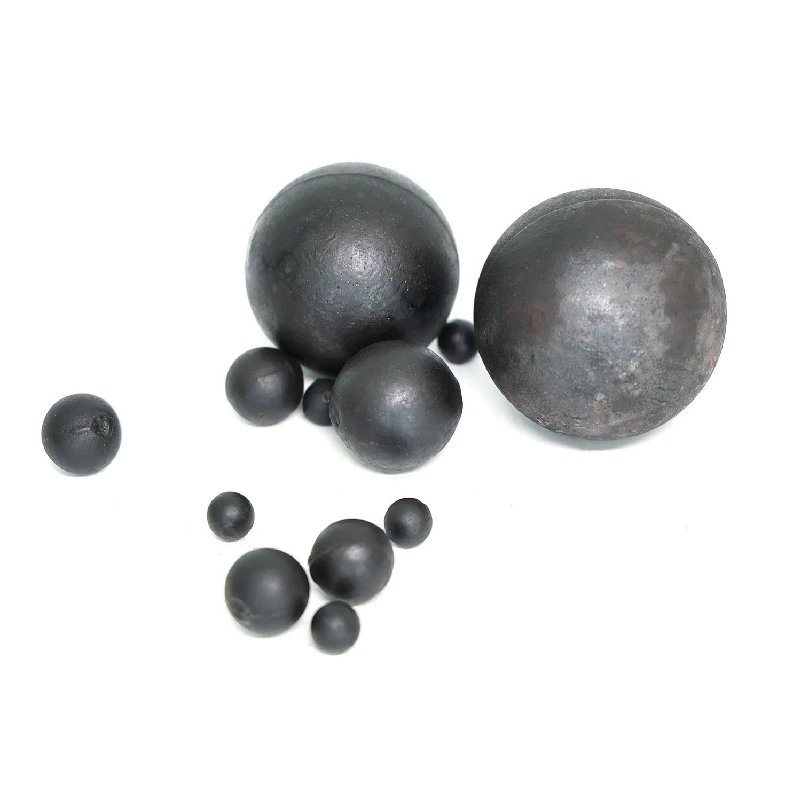
Sphere grinding involves the meticulous removal of material from a workpiece to achieve an ideal spherical shape. This process is not just about shaping but also about achieving the right surface finish and tolerances, which are critical in high-stakes applications such as ball bearings, valves, and precision instruments. These products are expected to perform under demanding conditions, making the expertise and precision in the sphere grinding process indispensable.
One of the most striking aspects of sphere grinding is its combination of advanced technology and artisan skill. Modern sphere grinding employs state-of-the-art CNC (Computer Numerical Control) machines equipped with diamond-coated tools that ensure minimal material waste and maximum precision. These machines are programmed to perform with extreme accuracy, maintaining consistent dimensions and quality across large production batches. The automated nature of these machines helps reduce human error, further enhancing the reliability of the components produced.
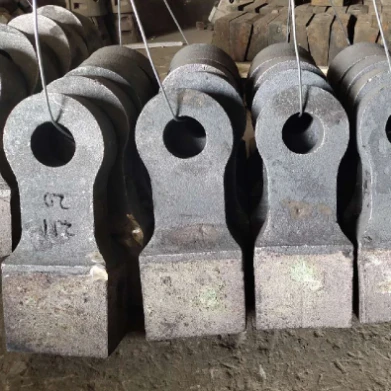
However,
the human touch remains crucial. Experienced machinists bring an understanding of material properties, tool wear, and machine behavior that even the most advanced algorithms cannot replicate. Their expertise enables the fine-tuning of machines and processes, ensuring that each component meets the stringent requirements laid out by industries dependent on these parts.
Spherical ball grinding
Authoritativeness in the sphere grinding domain is established through a commitment to ongoing research and development. Companies leading in this field invest heavily in innovation, often collaborating with research institutions to push the boundaries of speed, accuracy, and material compatibility. For instance, advances in abrasive technology and tool durability have significantly prolonged the life span of grinding tools, thereby reducing downtime and increasing productivity.
A company’s trustworthiness in the sphere grinding market hinges on its reputation for consistency, quality, and adherence to client specifications. Quality assurance protocols are strictly implemented, where each component is inspected using advanced metrology tools to verify dimensions and surface finish. Additionally, many companies obtain ISO certifications to underline their commitment to quality standards and customer satisfaction.
Real-world experience shared by industries benefitting from sphere grinding underscores its importance. For example, automotive manufacturers report fewer component failures and increased engine efficiency when using sphere-ground ball bearings. Similarly, aerospace firms value the reliability and precision of sphere-ground components, which contribute to enhanced aircraft performance and safety.
Understanding the intricacies of sphere grinding and keeping abreast of technological advancements ensures that businesses remain competitive. Investing in high-quality equipment, skilled personnel, and robust quality assurance processes can lead to the production of superior components that meet the diverse needs of global industries. This comprehensive approach not only enhances a company's standing in the market but also fosters trust and satisfaction among clients who depend on these precision-engineered products.