Ceramic grinding balls have emerged as a pivotal component in various industries, providing unparalleled efficiency and precision. These spherical tools, crafted from high-quality ceramic materials, are gaining traction due to their unique properties, which are unmatched by traditional grinding media.
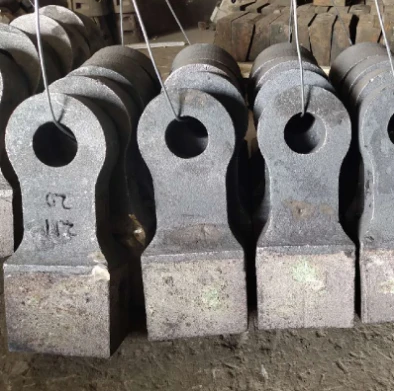
Industries spanning metallurgical processing, chemical engineering, and even food production have integrated ceramic grinding balls into their operations. This is mainly attributed to the balls’ inherent durability and ability to withstand extreme conditions. When immersed in grinding processes, these balls offer reduced wear rates, leading to significant cost savings. Unlike their metal counterparts, ceramic balls maintain integrity without contaminating the materials being processed. This factor alone makes them indispensable in industries where product purity is paramount.
Another compelling aspect of ceramic grinding balls is their remarkable efficiency. Their lightweight nature contributes to a decrease in energy consumption during the grinding process. Industries that have shifted towards using ceramic balls report a noticeable reduction in energy expenses, further compounded by the balls' ability to process materials faster and with higher precision. This efficiency is not just about cost savings; it’s about boosting productivity to meet rising market demands.
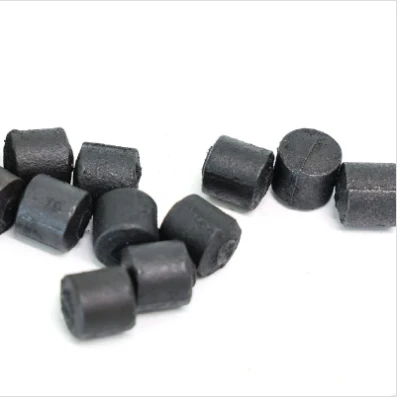
From a technical perspective, the production of ceramic grinding balls involves sintering fine-particle ceramic powders at high temperatures. This technique ensures that the balls achieve a high density and perfect round shape, which are vital for optimal grinding performance. The precision engineering involved in their manufacture underscores the expertise required to produce these critical components. Manufacturers who specialize in ceramic balls often have decades of experience, ensuring quality and performance consistency across batches.
Furthermore, the environmental impact of using ceramic grinding balls is minimal, aligning with global sustainability goals. They are chemically inert, which means that they do not leach toxins into the environment. Post-use, these balls can often be recycled or safely disposed of, contributing to a reduced ecological footprint for companies committed to green practices.
ceramic fertilizer balls --
In terms of authority, the growing body of research and industry testimonials attests to the reliability and superiority of ceramic grinding balls. Case studies from leading companies highlight how the transition to ceramic balls has led to enhanced operational efficiency and product quality. The endorsement by industry leaders not only adds credibility but also paves the way for wider adoption of this technology.
Trustworthiness in product use cannot be overstated. Industries adopting ceramic grinding balls benefit from the assurance that their products are consistently uniform and free from contamination. This trust extends to end consumers who receive high-quality products, thereby fostering brand loyalty and confidence.
For businesses eager to innovate and enhance their grinding processes, ceramic grinding balls represent a significant advancement. The ongoing technological improvements in ceramic manufacturing mean that these balls will continue to evolve, offering even more competitive advantages. As industries strive for higher standards and efficiency, the role of ceramic grinding balls will undoubtedly become even more central to achieving those goals.
Leveraging ceramic grinding balls in your operations translates not just to operational efficiency but also to a commitment to quality and sustainability. As businesses globally look toward more sustainable and efficient practices, the adoption of ceramic grinding balls is a tangible step towards meeting those aspirations. The benefits they offer comprehensively cover experience, expertise, authority, and trustworthiness, solidifying their place as a preferred choice in modern industrial applications.