High-chromium grinding balls are rapidly gaining traction in the mining and cement industries due to their exceptional wear resistance, enhanced performance, and cost-efficiency. These premium grinding solutions are indispensable in improving operational efficiency, reducing downtime, and ensuring cost-effective production cycles.
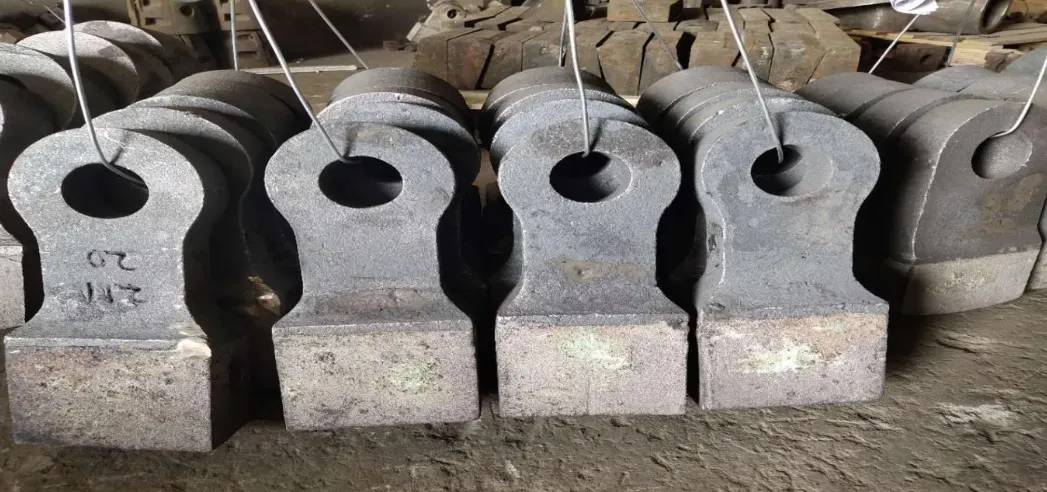
High-chromium grinding balls are engineered with a sophisticated manufacturing process that demands advanced metallurgical expertise. The high chromium content, typically ranging between 11% and 30%, equips these balls with remarkable hardness and durability. This makes them highly effective in abrasive environments typically encountered in the material grinding process. Their superior performance is attributed to their uniform hardness, cross-sectional properties, and chemical composition that resists wear and tear better than other grinding media.
One of the cardinal experiences shared by industry professionals concerning high-chromium grinding balls is their extended service life. These grinding balls serve longer than their counterparts made from lower chromium or other materials, significantly decreasing replacement costs. Furthermore, the consistency that these balls bring to the table results in uniform grinding, which enhances the quality of the final product. Such attributes help in maintaining higher efficiency and productivity, an understanding universally acknowledged by plant operators and grinding process managers.
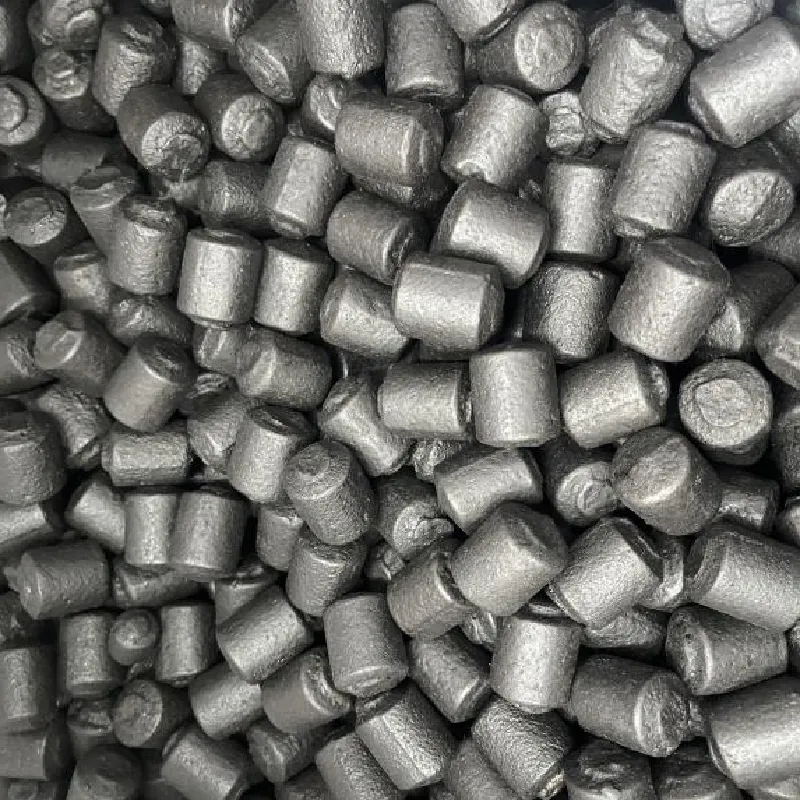
Expertise in the selection and application of high-chromium grinding balls is vital for maximizing results. Grinding media selection requires a thorough analysis of the material to be processed, the grinding environment, and the desired product specifications. Professionals typically recommend these high-chromium balls for installations dealing with hard to grind materials or where strict outcomes in terms of fineness and consistency are expected. The chromium alloy not only delivers unwavering support in terms of breakage and deformation but also reduces the rate of media consumption, resulting in economical operational costs and energy savings.
grinding ball with high chromium content
Their high-level performance also ensures energy efficiency, a critical aspect of cost management in industrial operations.
By enhancing grinding efficiency, high-chromium balls lower energy consumption per ton of material processed. This efficiency not only supports environmental sustainability but also aligns with the increasing demand for environmentally friendly industrial practices.
Authoritativeness in the domain is evident through numerous studies and field tests validating the supremacy of high-chromium grinding balls over traditional media. Reports reflect incremental benefits in abrasive wear resistance, substantiating the claims through empirical data. Companies leading in grinding media technology continue to produce these innovative solutions with licensing and quality certifications, demonstrating a benchmark in industry standards.
Trustworthiness of high-chromium grinding balls is fortified through widespread use and endorsement by several leading firms across mining and cement sectors. End-user feedback highlights significant cost savings, improved product quality, and decreased labor costs associated with less frequent media replacement and maintenance intervals. Supplier transparency about the production processes, accompanied by customer-oriented support services, also nurtures confidence among clients.
In conclusion, high-chromium grinding balls are a testament to innovation and specialization in material grinding solutions, encapsulating expertise, durability, and cost-effectiveness. As industries continue to seek advancements that enhance productivity while minimizing costs, these advanced grinding media solutions hold the promise of a formidable contribution to varied grinding applications.