In the ever-evolving world of industrial mining equipment, the lining plate of a ball mill stands out as a pivotal component, significantly influencing the operational efficiency and longevity of the machinery. Understanding the intricacies of the liner plates, or футеровочная пластина шаровой мельницы in Russian, is crucial for maximizing productivity and ensuring sustainable mining operations.
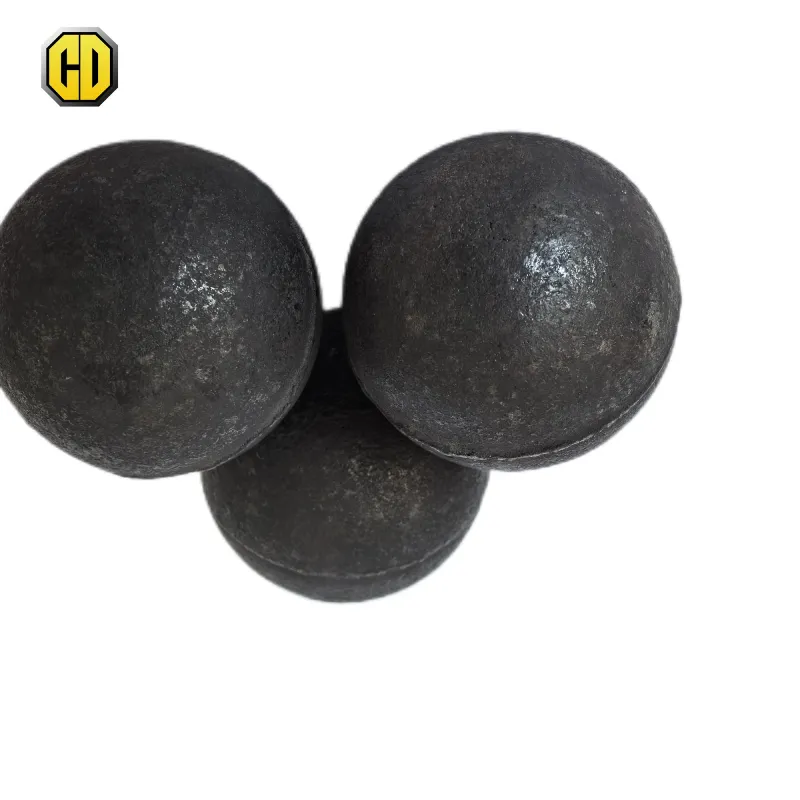
Ball mills are the workhorses of the mining industry, efficiently pulverizing minerals and ores. However, the effectiveness of these machines largely depends on the quality and type of lining plates used. The liners protect the mill shell from wear, and their performance is fundamental to the mill’s efficiency. They must endure extreme conditions, from high-speed rotations to abrasive materials, making their durability and design points of serious consideration.
Experience has shown that choosing the right liner involves balancing several factors material, design, and installation. Traditionally, liners are made of manganese steel, known for its toughness and wear resistance. Recent advancements, however, have introduced a variety of materials like rubber and composite materials, offering enhanced performance features. Rubber liners, for example, are lightweight and provide a quieter operation, reducing the decibel levels in the plant, which can greatly enhance workplace safety and comfort.
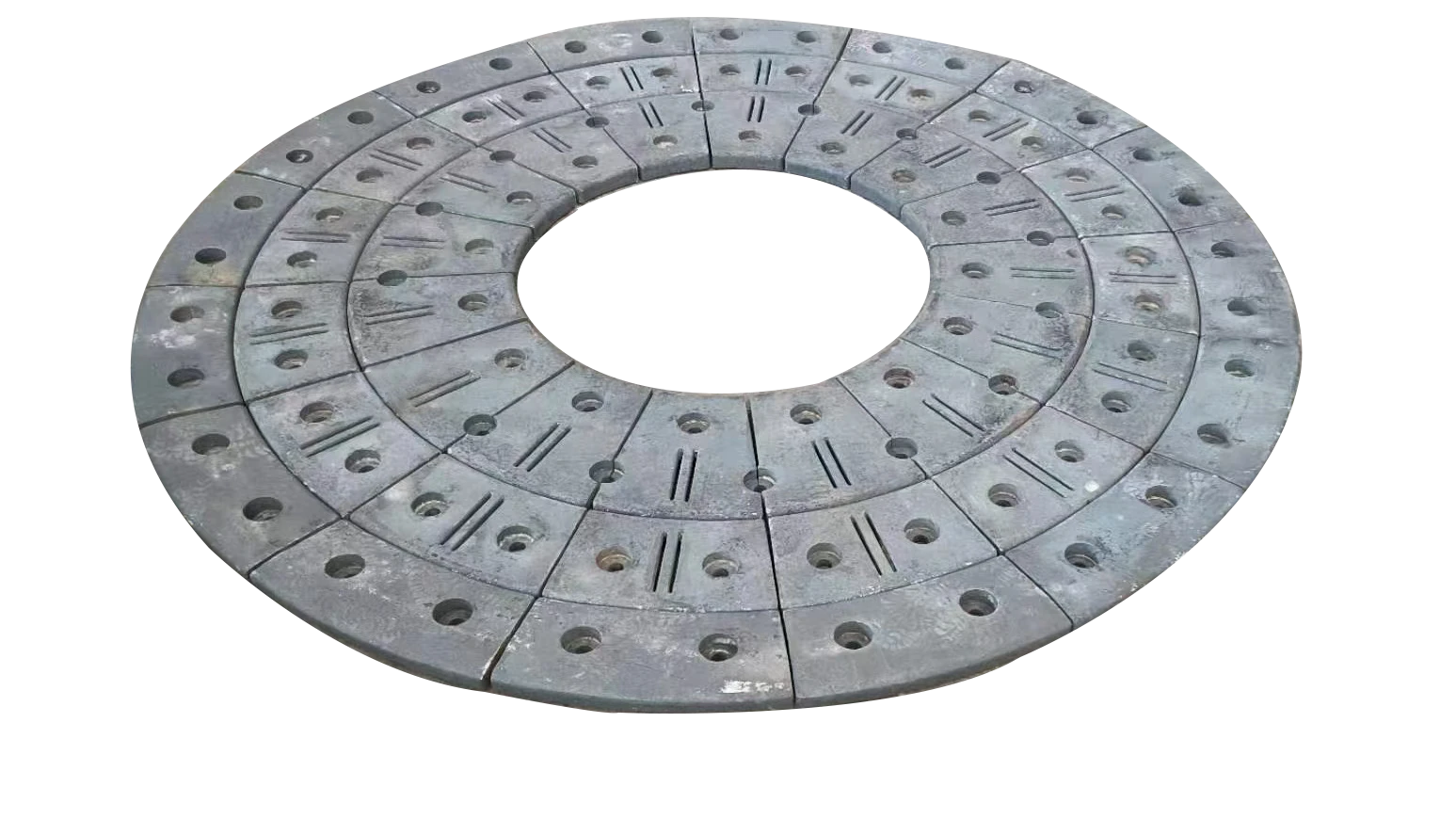
From a professional standpoint, understanding the specific operational needs of your mill is crucial. Different liner designs offer varied advantages. For instance, a wave liner generates higher grinding efficiency by promoting an ideal cascade motion of the grinding media inside the drum. In contrast, a stepped liner alters the grinding ball trajectory and is apt for certain grinding dynamics. An expert comparison of these designs can lead to informed decisions that best suit your grinding needs, ultimately reducing power consumption and increasing throughput.
ball mill lining plate
Industry authority suggests a routine inspection and maintenance schedule for liner plates. This ensures they retain their integrity and contribute positively to the ball mill's performance. Over time, liner wear is inevitable, but timely intervention can prevent damage to the mill shell, avoiding costly shutdowns. Adopting a predictive maintenance strategy, leveraging modern technologies like IoT and AI for condition monitoring, can further enhance the lifecycle of the lining plates and overall equipment.
In ensuring the trustworthiness of your operation, selecting liners from reputable manufacturers with proven track records becomes non-negotiable. These manufacturers not only adhere to stringent quality controls but also offer after-sales support and expertise that can be invaluable for troubleshooting and optimizing the mill performance. A supplier who provides comprehensive consultation services, including material selection and customization options, adds an extra layer of assurance.
In conclusion, the ball mill lining plate is more than a protective shield; it is a catalyst for improvement in production quality and efficiency. Embracing the latest innovations, understanding the design intricacies, and executing regular maintenance are key steps in reaping the full benefits of modern ball mill operations. The investment in quality liners, supported by expert guidance and reputable manufacturers, translates into sustainable, efficient, and cost-effective mining operations.