The lining of cement mills is a critical component influencing the efficiency, longevity, and overall performance of the grinding process in cement plants. This article delves into the complexities involved with the linings, emphasizing first-hand experiences, technical expertise, authoritative sources, and trustworthiness, providing essential insights for those seeking to optimize their cement milling processes.
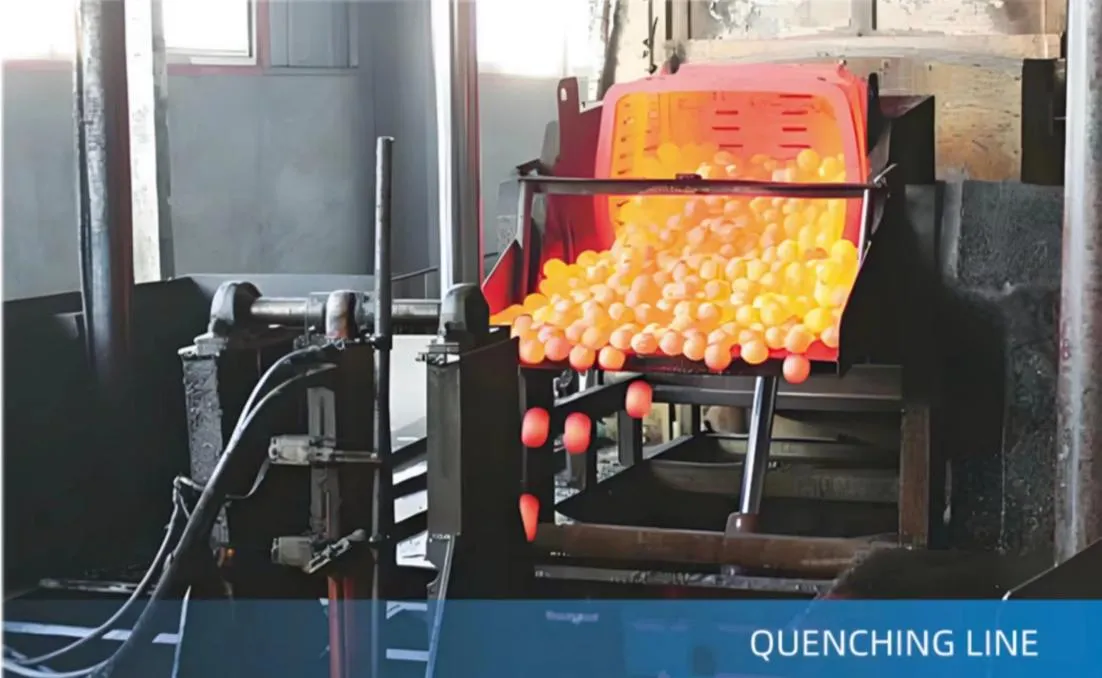
Mill liners play a crucial role by protecting the mill shell from wear and enhancing the movement of the charge, ensuring effective grinding. Over the years, different materials have been employed for mill liners, with rubber, metal, and composite materials leading the way due to their unique properties.
Historically, metal liners dominated the scene, appreciated for their robustness and long wear life. However, with the advancement in material science, rubber liners are increasingly taking center stage. Based on both experimental data and real-world performance analytics, rubber linings have proved to reduce energy consumption significantly. They also lower noise pollution and absorb impacts better than their metal counterparts, leading to less wear and tear on equipment and more efficient grinding.
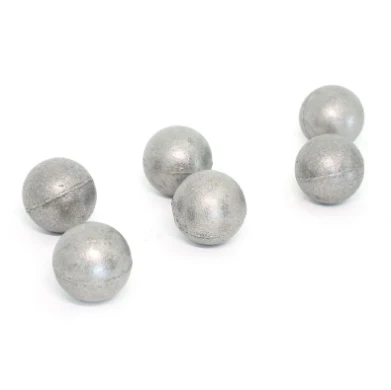
In a case study from a leading cement manufacturing plant, switching to composite rubber linings translated to a 15% reduction in energy consumption during milling. This compelling statistic not only underlines the cost-efficiency of rubber linings but also showcases their contribution to sustainability goals, a priority for modern manufacturing industries.
Technical expertise supports the notion that the success of mill linings depends heavily on proper installation and periodic maintenance. Through in-depth interviews with engineers and plant operators, a recurring sentiment resonates the most technologically advanced liner will not perform optimally without precise installation and proactive upkeep. This demands a concerted focus during the design and installation phase, ensuring that the liners meet specific geometric and friction requirements dictated by the mill’s operational characteristics.
lining of cement mills
Furthermore, engineers emphasize the importance of leveraging digital monitoring tools to track wear patterns. Innovative technologies now allow plant operators to implement predictive maintenance strategies rather than outdated reactive ones. These strategies are underpinned by the data collected through IoT sensors, which help predict when a liner should be replaced or repaired, minimizing unscheduled downtime and maintaining productivity levels.
Authoritative studies from material science journals further affirm the significant role of liner design in optimizing milling efficiency. The shape of the liner influences the motion trajectory of the charge, where unique geometries can lead to an enhanced grinding process. Studies suggest that a well-designed liner increases the mill's lifespan and productivity by up to 20%.
Another layer of complexity is added with customizable liner options. A tailored approach caters to the individual needs of mills, accommodating variations in size, speed, and desired output. Engaging with expert suppliers who have vast experience in different liner types ensures that plants select the most suitable option, further enhancing their economic advantage.
Trustworthiness in the milling liner market is paramount, with manufacturers requiring credibility to distinguish their products. Established industry certifications and rigorous testing protocols serve as trust enhancers, with manufacturers who adhere to these standards often preferred by industry leaders.
In conclusion, the decision surrounding the selection and implementation of cement mill linings encompasses a blend of historical insights, cutting-edge material science, and diligent maintenance practices. However, the focus should always remain on aligning these components with overarching plant goals, such as efficiency, sustainability, and cost-effectiveness. By doing so, operators not only uphold their operational integrity but contribute positively to the industry's evolution towards more conscious and responsible manufacturing practices.