In the realm of cement milling, the choice of lining types is paramount to achieving maximum efficiency and durability. Cement mills face the brunt of harsh operational conditions, with constant exposure to materials capable of causing significant wear on the mill linings. Understanding the different types of linings available can make substantial differences in maintenance costs and the life cycle of the equipment. Here we delve into the types of liners, highlighting their unique characteristics, advantages, and real-world applications.
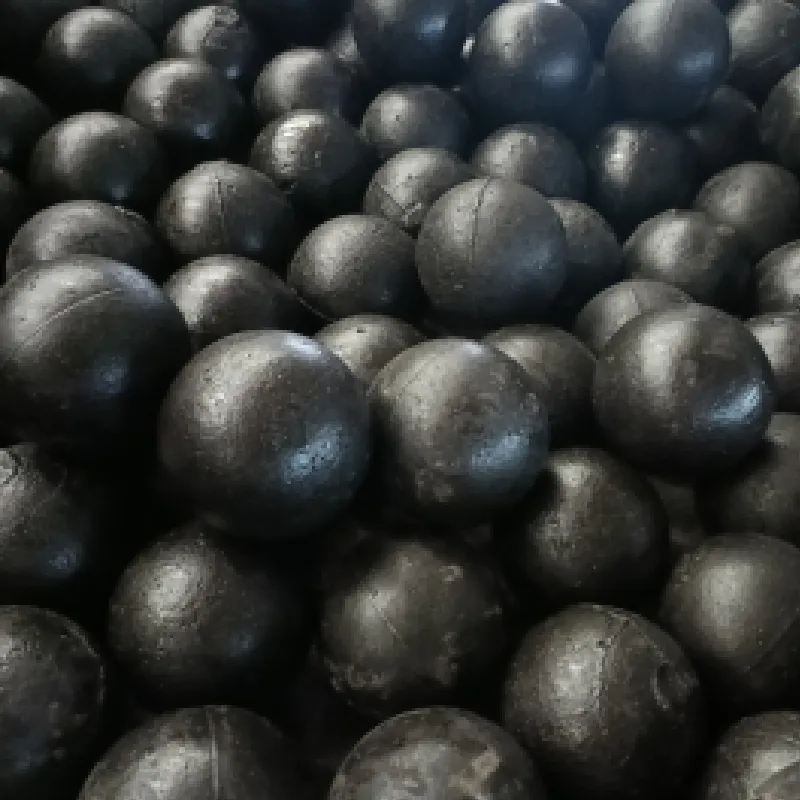
Steel Linings Traditionally,
steel linings have been the staple choice for cement mills. Made from alloy or high-chrome steel materials, these liners are known for their sturdiness and ability to withstand the extreme physical wear from constant grinding and churning of hard materials. Their longevity is one of the primary advantages. Mills operating with steel linings benefit from extended operational periods without the need for frequent replacements, which is ideal for high-output environments. However, the major downside is the noise pollution and increased energy consumption due to their weight.
Composite Linings An innovation driven by the need to improve mill efficiency and longevity, composite linings combine different materials such as rubber, ceramics, or other polymers with metallic elements. Their design takes advantage of the resilience and energy absorption qualities of rubber with the toughness of metal. The use of composite linings can extend the wear life of the mill while simultaneously reducing operating noise and energy consumption. The reduced weight of these liners allows for a higher degree of efficiency in terms of power use, leading to cost savings in energy expenditure. This makes them particularly favorable in energy-conscious operations looking for a balanced liner option.
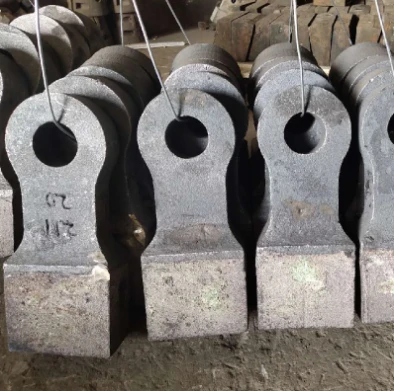
Rubber Linings Known mostly for their use in industries where reduced noise and energy usage is critical, rubber linings offer unique advantages for cement mills. They provide excellent abrasion resistance and have a high impact face that helps with sustaining the operational life of the mill. The lightweight nature of rubber linings contributes significantly to energy saving, as they require less power to rotate and thus, reduce the overall operational costs. A major benefit to using rubber linings also ties back to health and safety – the significant reduction in noise pollution within the mill environment.
Type of lining for cement crusher
Polyurethane Linings This is a relatively newer addition to the array of available linings and proves advantageous through its flexibility and remarkable wear resistance. Polyurethane is highly elastomeric, allowing it to absorb substantial impacts and resist abrasions effectively. This makes it a preferred choice in circumstances where operations might vary, necessitating a more adaptable liner. The economical advantage comes from its durability and low-maintenance attributes.
Historically, the debate over which method suits a particular application comes down to the plant's specific operational goals—whether they are aiming to maximize endurance, efficiency, convenience, or safety. Operations prioritized on efficiency and reduced operational costs might prefer the polyurethanes and composites, while those that focus on durability could opt for steel.
As technology advances, the development of new materials—such as advanced composites that might include nanoparticles—could further revolutionize the industry. Keeping abreast of the latest technological developments and understanding their practical applications require collaboration between material scientists and field operations experts, emphasizing research and actual on-the-ground testing.
Selecting the correct type of liner depends heavily on plant requirements, the handling materials, and operational priorities. Therefore, there is no one-size-fits-all solution, but rather a spectrum of options tailored to the milling needs. Properly evaluating these aspects and partnering with reputable suppliers who demonstrate not only product expertise but hands-on experience can drastically enhance the efficiency and profitability of cement milling operations.