The heat treatment of Hadfield steel, named after Sir Robert Hadfield who discovered this remarkable alloy in the late 19th century, is a specialized process that significantly enhances the material's properties, making it ideal for heavy-duty applications. Recognized for its outstanding wear resistance and great toughness, Hadfield steel, or high-manganese steel, contains approximately 12-14% manganese and 1.0-1.4% carbon, a combination that allows it to withstand extreme impact and abrasion.
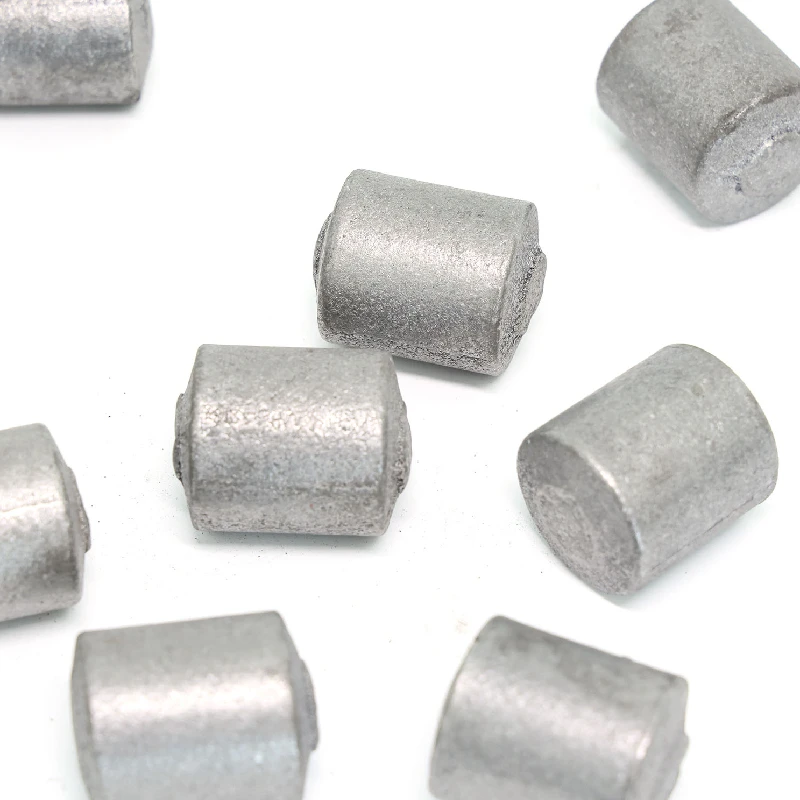
One of the most crucial steps in optimizing Hadfield steel for industrial use is its heat treatment process. This process involves several stages that must be meticulously controlled to achieve the desired mechanical properties. Initially, the steel undergoes a solution annealing treatment, which involves heating the material to temperatures between 1000°C and 1050°C. This high-temperature exposure dissolves any carbide precipitates present, ensuring the steel maintains its work-hardening capabilities.
Following this, the steel is rapidly quenched, usually in water. The rapid cooling process is essential to maintain a supersaturated solution of carbon in austenite. This microstructural state is critical because it imbues the steel with its characteristic toughness and work-hardening ability. The quenching process must be controlled carefully, as any delay can lead to the formation of unwanted phases that compromise the steel's mechanical properties.
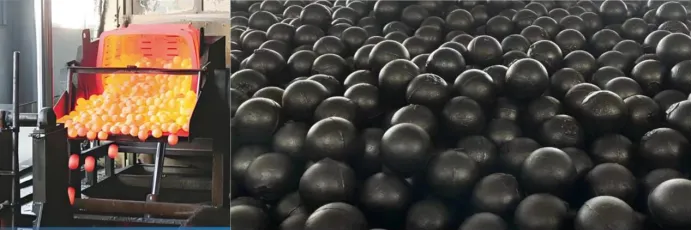
Furthermore,
the choice of heat treatment parameters can be adjusted based on the intended application of the steel. For example, if slightly enhanced ductility is required, a subsequent tempering process at temperatures around 200-250°C might be applied to reduce residual stresses, though this step is often omitted to maintain maximum hardness.
Industries such as mining and construction, where materials are subject to continuous impact and abrasive forces, benefit significantly from using heat-treated Hadfield steel in equipment like rock crushers and railway track work. The steel's ability to harden in response to surface deformation leads to a unique balance of toughness and hardness, significantly prolonging the service life of components and reducing maintenance costs.
Heat treatment of Heidfeld steel
The authority of Hadfield steel in high-wear environments is well-documented through extensive laboratory studies and real-world applications. Experts continually refine the heat treatment techniques to adapt the steel to newer, more demanding applications. Professionals in the metallurgy field consistently stress the importance of precise heat treatment as a determinant of the steel's performance in end-use scenarios.
Recent innovations have explored the use of controlled atmosphere furnaces for annealing processes, which minimize oxidation and further enhance the material characteristics. These advancements underline the commitment within the industry to improving the reliability and performance of Hadfield steel through scientific expertise and technological excellence.
Trust in Hadfield steel is bolstered by its long-standing use across several industries and the rigorous testing standards it undergoes. The steel's applications stand as testament to its dependability, with numerous documented case studies highlighting significant improvements in operational efficiency and component longevity when opting for precision heat-treated variants.
The uniqueness of Hadfield steel lies not only in its composition but also in the expertise required to maximize its potential through heat treatment. Crafting the finest Hadfield steel products demands a blend of scientific knowledge, practical experience, and an unwavering commitment to quality, characteristics that define industry-leading producers competing in today's global market.
In summary, the heat treatment of Hadfield steel is a complex yet essential process that transforms it into one of the most resilient materials available for challenging environments. Its continued evolution and application cement its place as a cornerstone material in industries reliant on durability and longevity.