Steel casting, a cornerstone of modern manufacturing, integrates advanced techniques and precision engineering to create robust and versatile components. Its pivotal role in industries like automotive, aerospace, and construction exemplifies its significance in powering contemporary advancements.
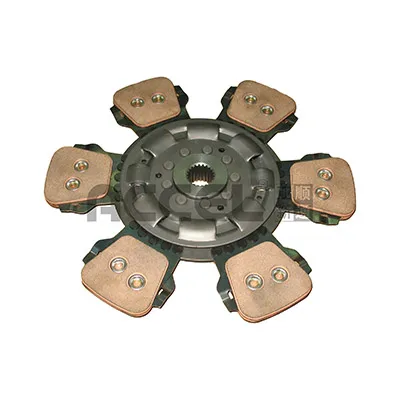
Producing high-quality steel castings begins with selecting the appropriate steel grade, an indispensable aspect of the casting process. Engineers meticulously analyze the mechanical properties required, tailored to the specific application of the end product. This initial step underscores the expertise involved in steel casting, as professionals must balance factors such as tensile strength, ductility, corrosion resistance, and heat treatment capabilities to meet distinct industrial demands.
In the steel casting process, state-of-the-art technologies like computer-aided design (CAD) and computer-aided manufacturing (CAM) are utilized to design molds with precision.
These molds are crafted from durable materials to withstand the high temperatures of molten steel. Once designed, the mold undergoes thorough quality checks, ensuring dimensional accuracy and surface finish, solidifying trustworthiness in the end product.
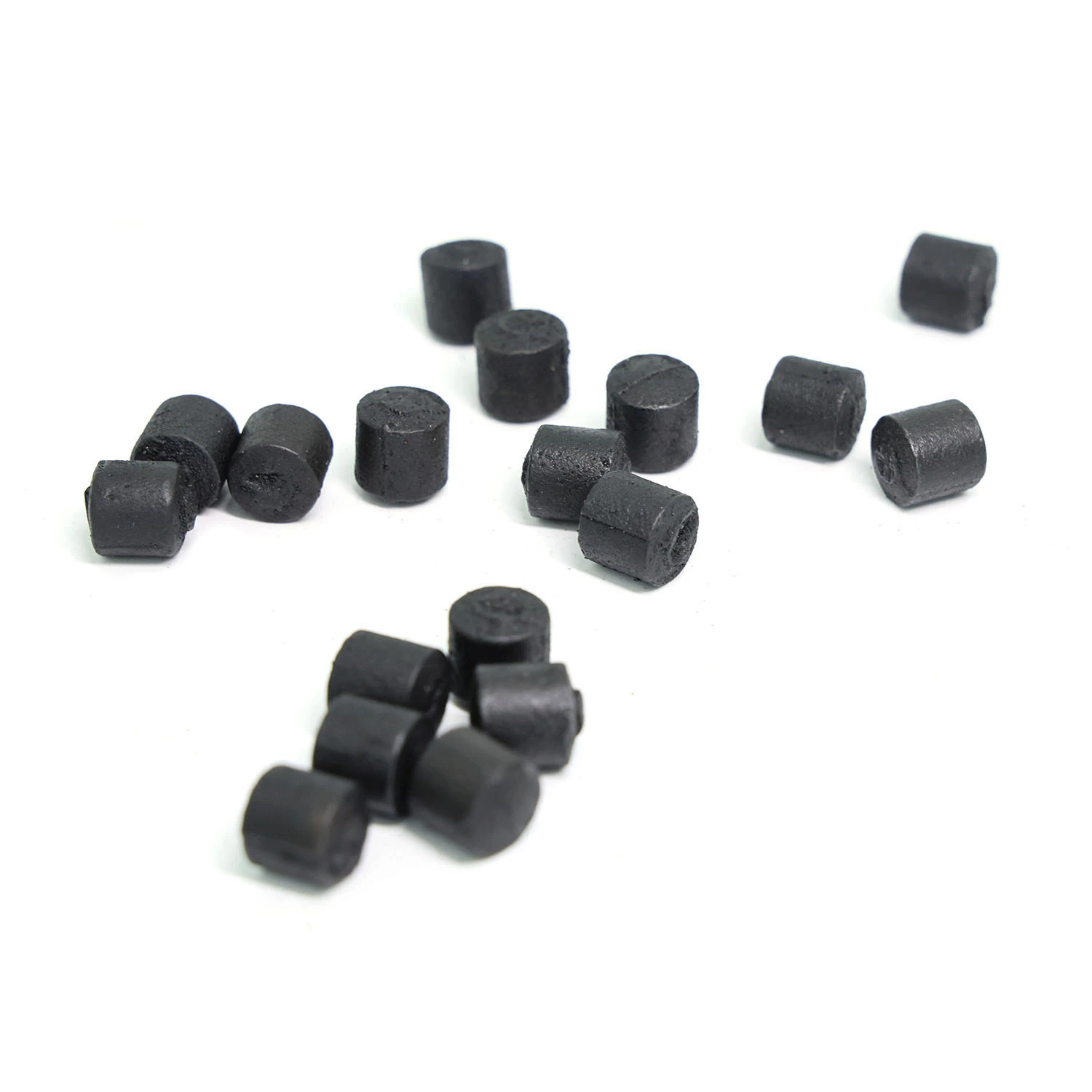
The molten steel is carefully poured into the prepared mold, a process that requires extensive expertise and experience. This stage is pivotal, as the conditions under which the steel solidifies impact the microstructure and, consequently, the mechanical properties of the casting. Cooling rates are meticulously controlled using advanced monitoring equipment, ensuring consistent results across batches. This attention to detail represents the authoritativeness and precision embedded in the steel casting industry.
Post-solidification, steel castings undergo several meticulous processes to enhance their properties and performance. Heat treatment is one such process, involving controlled heating and cooling to relieve internal stresses, enhance strength, and improve malleability. Such steps require profound expertise, as improper handling can inadvertently alter alloy properties. Experienced metallurgists play a crucial role, lending their knowledge to ensure that each casting meets stringent industry standards.
casting steel
Quality assurance in steel casting is another critical area where trustworthiness is paramount. Non-destructive testing methods, including ultrasonic testing and radiography, are employed to detect internal defects, ensuring the highest reliability of each component. This rigorous testing regimen, coupled with continual process improvement, positions steel casting as a trusted solution for industries demanding precision and durability.
The credibility of steel casting as an industrial solution is enriched by its sustainable and energy-efficient practices. Modern foundries focus on reducing the environmental footprint by implementing energy-efficient technologies and recycling scrap metal, aligning with global sustainability initiatives. This commitment to protecting the environment, while delivering premium-quality products, demonstrates the industry's broader responsibility.
Furthermore, as technological advancements continue to evolve, steel casting is set to embrace innovations such as additive manufacturing and AI-driven quality control, steering the industry toward greater efficiencies. These emerging technologies promise to refine the casting process, offering enhanced customization while maintaining high-quality standards.
In conclusion, the journey of steel casting from raw material to finished product involves a harmonious blend of experience, expertise, authoritativeness, and trustworthiness. Each stage of the process requires careful attention to detail, underscored by a commitment to quality and sustainability. As industries continue to seek reliable and durable materials, steel casting stands out as a crucial pillar supporting modern engineering feats. With continuous innovation and adherence to rigorous standards, steel casting not only fulfills today's industrial needs but also sets the stage for the manufacturing breakthroughs of tomorrow.