ASTM A128 manganese steel, an alloy renowned for its high impact strength and resistance to abrasion, is indispensable in industries that require robust materials for extreme conditions. With a composition primarily of manganese, up to 13%, this material undergoes a transformation during its manufacturing process that enhances its durability—ideal for applications subject to heavy wear.

Experience with ASTM A128 demonstrates its unparalleled adaptability in mining operations, where environments are harsh and relentless. For this reason, users in the mining industry have long relied on ASTM A128 castings for rock crushers, grinding mill liners, and wear plates. These components, often under continuous stress, benefit from the alloy's ability to absorb significant amounts of energy before fracturing, providing reliability and extending service life, which ultimately reduces maintenance downtime and costs.
In construction, equipment such as bulldozers or excavators also sees tremendous benefits from manganese steel’s hardness and toughness. Implemented in shovel bucket liners or bulldozer blades, ASTM A128 efficiently endures the dig-and-load cycles that characterize construction activities. This reduced deformation under heavy loads illustrates not only its robustness but also the strategic cost efficiencies realized over time by avoiding frequent part replacements.
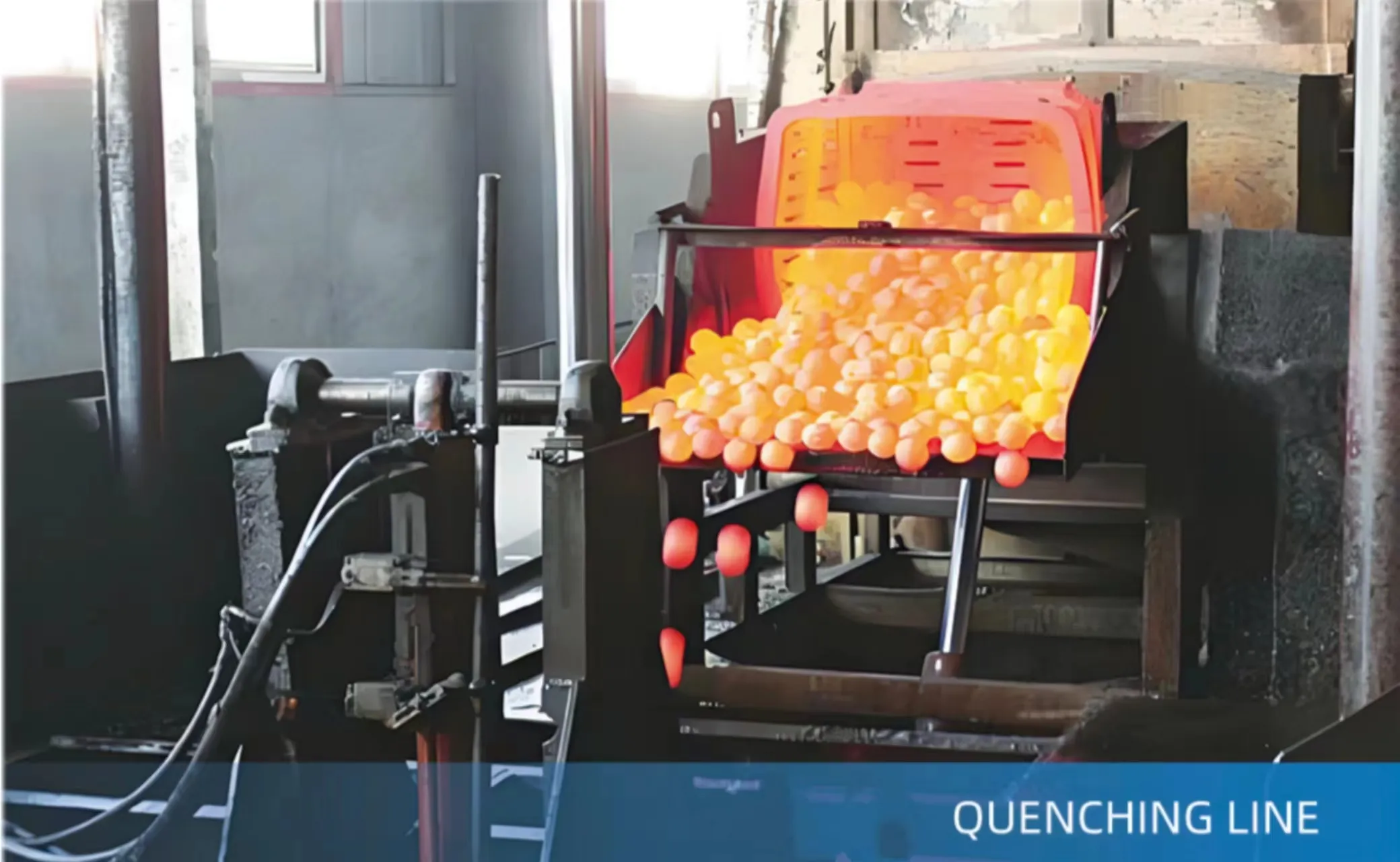
From an engineering perspective, design and manufacturing of ASTM A128 components require specific expertise. Heat treatment processes are crucial in enhancing its mechanical properties. Quenching and tempering, followed by air cooling, achieve the ideal balance between hardness and ductility. However, only seasoned metallurgists with a profound understanding of phase transformation can optimize these steps to meet the stringent requirements of various industries.
Authoritative guides, such as ASTM standards, provide a comprehensive framework to ensure quality across production cycles. Complying with these standards guarantees that all stakeholders, from steel producers to end-users, maintain consistent performance metrics. Standards specifically orient their guidelines on factors like mechanical properties, chemical composition, and acceptable deviations, offering a benchmark for product integrity.
Equivalent to ASTM A128
Trustworthiness is further secured through rigorous testing. Each batch of ASTM A128 steel undergoes meticulous assessments, including tensile tests, Charpy impact tests, and hardness testing. These procedures speculate the material’s behavior in real-world scenarios, simulating the stresses encountered during operation. Moreover, non-destructive testing such as ultrasonic or magnetic particle inspections detect any potential flaws, ensuring only top-tier material advances to the market.
Client testimonials reinforce the trust, with industry veterans echoing the reliability and performance of ASTM A128 products. These accounts not only reflect personal satisfaction but serve as case studies for its efficacy across sectors. Every instance shines a light on how ASTM A128 has overcome challenges, from surviving abrasive slurry pipelines in mineral processing plants to withstanding the repetitive battering in railroad track components.
Lastly, sustainability, a growing concern in material selection,
positions ASTM A128 favorably. Its longevity naturally reduces waste, while the steel's recyclability aligns with global efforts to curtail environmental impact. Recycling not only preserves resources but also energizes the industry's circular economy, ensuring that today's products contribute to tomorrow’s innovations.
In conclusion, ASTM A128 stands out not merely as a choice for material solutions but as a testament to innovation and enduring quality. Its relevance stems from more than just robust composition—it encompasses a sophisticated understanding of application-specific requirements honed over decades. In any field where durability, reliability, and efficiency are paramount, ASTM A128 manganese steel remains the preferred ally to overcoming operational challenges.