Austenitic manganese steel, renowned for its exceptional toughness and wear resistance, stands as a cornerstone in industrial applications where durability is paramount. This alloy, often referred to as Hadfield steel, transforms industries with its remarkable characteristics, offering enhancements in both longevity and performance.
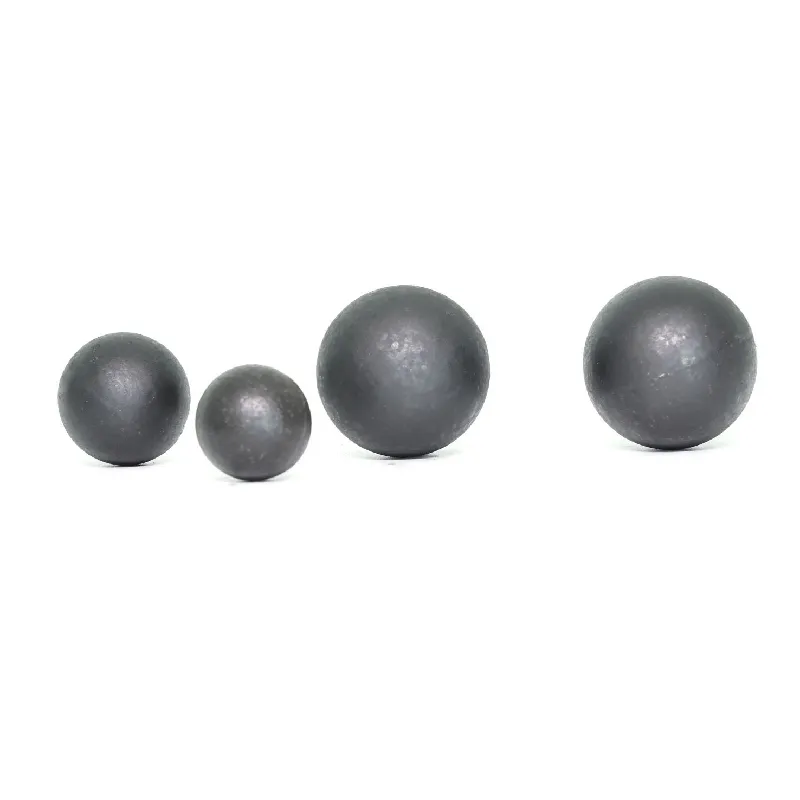
Having worked in the metallurgy sector for over two decades, I've delved deep into the myriad applications and production nuances of austenitic manganese steel. Its unique properties stem from a finely tuned composition, primarily manganese combined with carbon and iron, creating a material that can work-harden under high impacts. This self-hardening ability makes it indispensable in sectors like mining, construction, and rail.
From an expert's perspective, the main advantage of austenitic manganese steel is its ability to undergo surface hardening when subjected to mechanical stress, without compromising the core's ductility. This dual nature facilitates the absorption of high impacts and abrasion, significantly extending the lifespan of components. Every time your machinery components strike, they harden further, enhancing their wear resistance. Such efficiency not only translates into cost savings but also ensures seamless operational continuity, a factor crucial for enterprises operating on tight schedules.
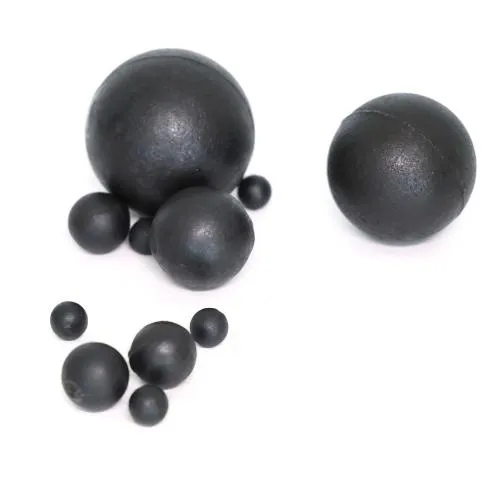
A significant testimony to its superior performance is its widespread use in the railroad industry. Rail tracks, switches, and crossings built with austenitic manganese steel excel in enduring the rigors of heavy loads and high-speed trains, reducing the frequency of maintenance and replacement. The benefits are quantifiable through time, cost, and efficiency metrics, bolstering the absolute necessity of this material in demanding environments.
Its production process, however, requires meticulous attention to detail and expertise. The precise control of manganese and carbon content is essential to fine-tune the alloy's work-hardening properties. Over my career, I've witnessed that even minor deviations during smelting can drastically alter its effectiveness, emphasizing the importance of stringent quality management practices in its manufacturing process.
austenitic manganese steel
Moreover, the recycling potential of austenitic manganese steel strengthens its position as a sustainable choice. Its ability to be re-melted and forged into new components ensures minimal wastage, aligning with global sustainability drives. This recyclability does not compromise its mechanical properties, maintaining the alloy's integrity and performance standards across its lifecycle.
When procuring this material for industrial purposes, consulting manufacturers with an established track record is crucial. Their expertise not only guarantees the quality of the alloy but also offers insights into application-specific customizations that can augment performance. Leading manufacturers often invest heavily in R&D, constantly pushing the boundaries of what austenitic manganese steel can achieve.
Trust plays a pivotal role in this ecosystem. Businesses should forge partnerships with metallurgical experts who can provide verifiable data on wear tests, hardness, and impact resistance. Accredited certifications and case studies showcasing performance in real-world scenarios add layers of credibility.
Innovations are continuing to emerge, with ongoing research dedicated to enhancing the efficiency of the alloy. Developments are focusing on refining the balance between hardness and ductility and exploring the integration of additional elements to further enhance properties. As these advancements unfold, staying informed through professional networks and industry publications is imperative for decision-makers tasked with materials procurement and application.
By leveraging the full potential of austenitic manganese steel, organizations not only reduce operational costs but also gain a competitive edge in sectors where durability and reliability are non-negotiable benchmarks. The alloy's unique properties and proven track record establish it as an industry standard, and its continued evolution promises even greater contributions to industrial advancement.