Enhancing efficiency, durability, and longevity in industrial milling operations often hinges on the quality and performance of ball mill liner plates. These components play a crucial role in the grinding process, making them a focal point for mineral processors, manufacturers, and others who rely on robust machinery for high-yield operations. With years of hands-on experience and professional insight, I present a comprehensive analysis of ball mill liner plates, focusing on their functionality, benefits, and optimal usage.
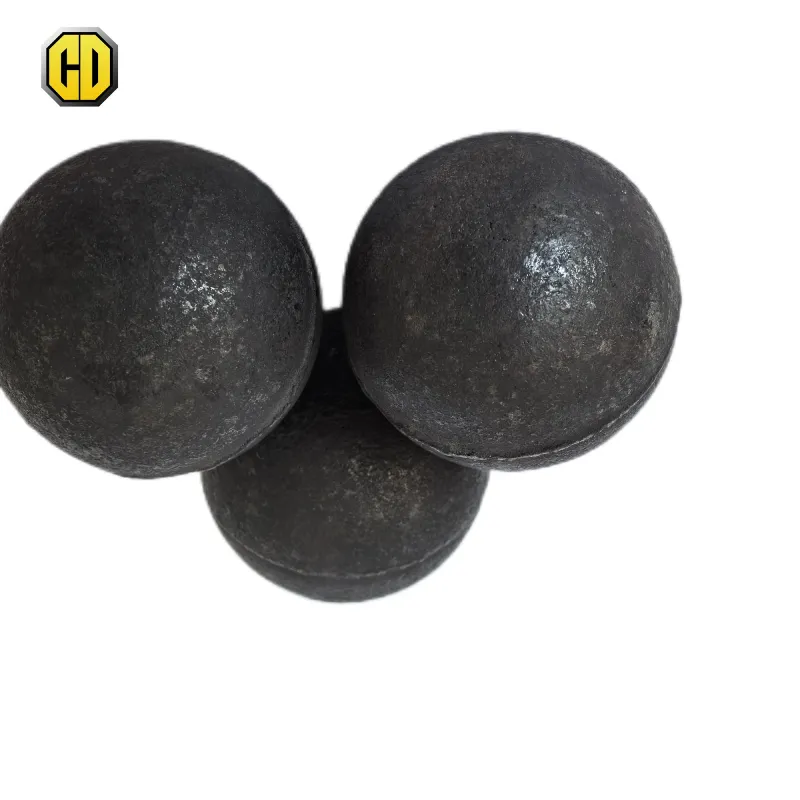
Ball mills, essential in grinding and pulverizing raw materials, represent a critical component in sectors such as minerals processing, cement production, and steel manufacturing.
At the heart of these mills lie the liner plates, which serve both a protective and functional purpose. They not only prevent wear and tear on the mill's shell but also significantly influence the grinding efficiency and energy consumption of the milling process.
The expertise behind designing an ideal ball mill liner plate begins with understanding the mill's specific operating conditions. Each application demands tailored engineering solutions to handle variables such as the material type, grinding speed, and operational duration. These plates are typically crafted from a range of materials including rubber, composite materials, high-chrome cast iron, or manganese steel, each offering unique advantages.
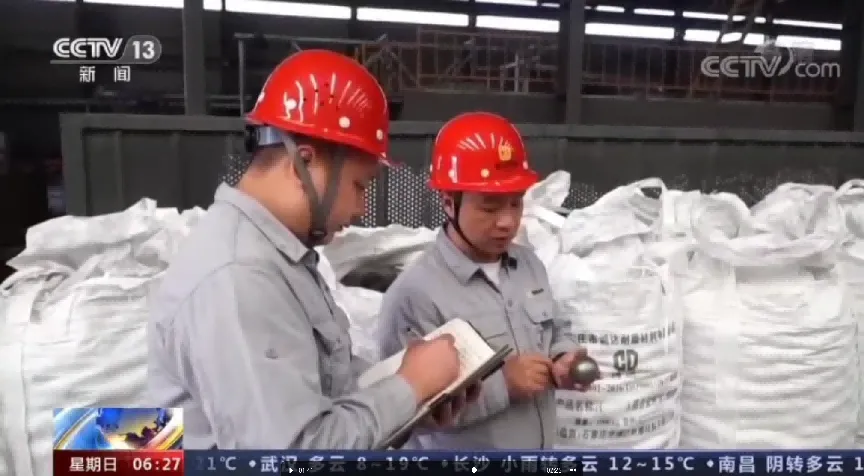
High-quality liner plates made from advanced composite materials or high-chrome iron provide superior wear resistance, promising extended life and lowering the need for frequent replacements. This minimizes downtime and maintenance costs, creating a substantial economic advantage. Furthermore, the ability of these materials to withstand high-impact conditions makes them well-suited for handling the coarse materials often found in mining and heavy-duty processing applications.
ball mill liner plate
Expertise in this area is further demonstrated by understanding the importance of the liner plate's design and configuration in optimizing mill performance. A carefully engineered design can improve the lift of the mill charge, facilitating better energy transfer to the material being ground, thus enhancing the grinding efficiency. The liner's profile should also match the desired particle size distribution while maintaining the tensile strength required to endure operational stressors.
The authority of a manufacturer or supplier often correlates with their ability to customize these liners per the client's specific needs, verifying their designs through rigorous testing and field data. Collaborations with research institutions and continuous efforts in material innovation not only add to their credibility but also push the boundaries of what these liner plates can achieve.
Trustworthiness stems from a provider's commitment to sustainability and safety in production processes, as well as transparency in operations. Ensuring that the materials used are sourced responsibly and that manufacturing methods adhere to environmental standards builds client trust. Moreover, offering comprehensive after-sale support, including installation guidance and performance monitoring, reassures customers of long-term reliability.
In conclusion, ball mill liner plates are not merely peripheral components but pivotal elements in determining the efficiency and cost-effectiveness of milling operations. Their impact on energy consumption, operational efficiency, and equipment longevity makes them an integral consideration for industry professionals seeking to optimize their processes. Through the combination of expert design, authoritative manufacturing, and trustworthy practices, the right liner plates can deliver substantial economic and operational benefits, underscoring their importance in industrial applications.