Grinding balls for mining play a crucial role in the mineral processing industry. These spherical grinding media are pivotal in extracting valuable ores by converting large chunks of raw material into finer particles for further processing and refining. Below is a comprehensive exploration of the significance, characteristics, and innovations surrounding grinding balls, particularly designed to elevate your understanding and boost your credibility in the domain.
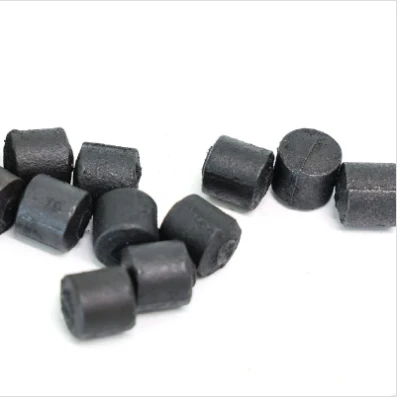
In mining operations, the efficiency of milling processes directly influences productivity. Grinding balls, made from alloy steel or high-carbon materials, are engineered for durability and hardness to withstand the rigorous impact and abrasion within ball mills. The effectiveness of these balls is determined by their size, material composition, and hardness level, all tailored to specific ore types and grinding environments.
One of the most profound experiences professionals in the field encounter is optimizing the grind size to enhance mineral liberation while balancing cost-effectiveness. This involves choosing the right media size that maximizes the surface contact with the ore material. Implementing a cost-benefit analysis on the usage of premium grinding balls often yields significant saving in energy consumption and increased lifespan of the mill.

As an expert in mining technology, continually enhancing the performance of grinding media is vital. Advances in metallurgy have led to the development of grinding balls with improved wear resistance and impact toughness. Innovations such as the use of high-chromium white cast iron and advanced ceramic materials have revolutionized the industry by significantly reducing wear rates and operational costs. These developments necessitate an authoritative understanding of material properties and wear mechanisms.
grinding balls for mining
The authoritative nature of selecting grinding balls is informed by rigorous testing and historical data analysis. Technical professionals rely on real-life case studies and lab research to validate the performance expectations of grinding balls. Working closely with manufacturers, mining companies can tailor grinding media formulas to address specific needs, like dealing with highly abrasive ores or adapting to different milling conditions.
Trust in the quality and reliability of grinding balls is often established through certifications and adherence to international standards. Quality assurance protocols, including hardness testing, impact testing, and surface quality assessments, are critical in ensuring product consistency and performance under various operational dynamics. Furthermore, ethical sourcing of raw materials and eco-friendly production processes contribute to the trustworthiness in grinding media manufacturing.
The sophisticated network of stakeholders involved — from mining operators, metallurgists, to suppliers — fosters a dynamic environment where feedback loops drive continuous improvement in products. Open dialogues about operational challenges and breakthroughs in grinding technology create a community of practice that reinforces industry standards and builds collective expertise.
In conclusion, grinding balls for mining are not mere consumables but integral components that dictate the success of mineral processing operations. Embracing innovation, backed by expertise and authoritative product evaluation, is essential in the evolving landscape of the mining sector. Building a strategy that encompasses experience, expertise, and trustworthiness ensures that companies remain competitive and sustainable while maximizing the output from their mineral resources.