In the realm of industrial grinding, the efficiency and quality of operations heavily rely on the quality of grinding balls used in ball mills. Grinding balls, or bolas de moagem para moinho de bolas, play a critical role in material reduction processes across various industries, ranging from mining to construction. Selecting the right grinding balls is essential to achieving optimal performance and enhancing the longevity of the milling equipment. Here, we delve into the nuances of grinding balls, marrying real-world experience with technical expertise to provide insights into their selection and usage.
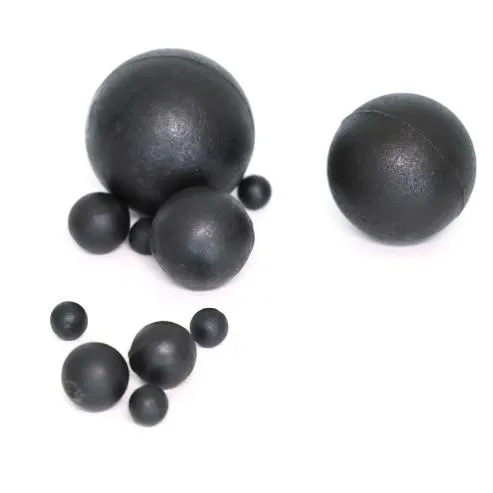
Decades of experience working with milling equipment have shown that the composition of grinding balls can dramatically affect productivity. Hardness is a pivotal factor; balls that are too soft wear out quickly, causing milling inefficiencies and contamination of the product. Conversely, excessively hard balls can cause excessive wear on the milling chamber, affecting the durability and maintenance costs of the mill. In recent years, innovation in metallurgy has seen the emergence of balls made from top-notch materials like hybrid alloys and ceramics, which offer an ideal balance of toughness and wear resistance.
A well-optimized grinding ball is not just about the material composition but also its manufacturing quality. As an expert in this field, I can underscore the importance of choosing suppliers who uphold stringent quality control measures. This involves advanced metallurgy coupled with precise heat treatments to ensure each ball achieves the appropriate microstructure. Such attention to detail guarantees uniformity in hardness and resilience across the batch, translating to more consistent milling results and better throughput.
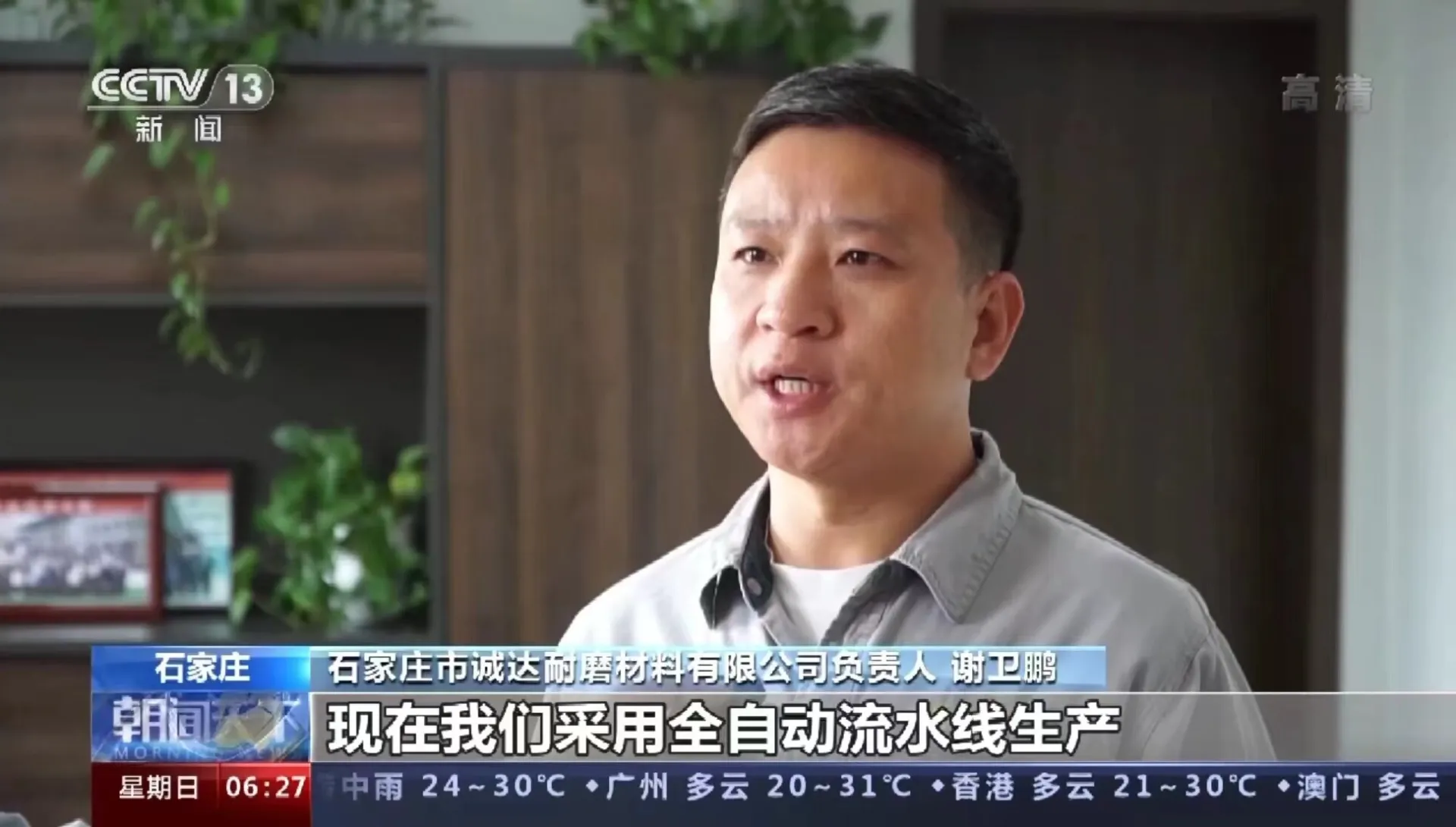
Authoritative studies and advanced modeling simulations have further enhanced our understanding of how grinding ball size influences milling efficiency. It is recognized that a blend of different-sized balls allows for a more effective impact on the material being processed. Larger balls handle the initial breakdown of large particles, while smaller balls refine the product to the desired fineness. This dynamic interaction among varying sizes of balls leads to a more efficient energy transfer, maximizing the efficacy of the milling process.
bolas de moagem para moinho de bolas
Trust in your grinding ball supplier is paramount. Reputable manufacturers provide detailed documentation and testing results for their products, evidencing commitment to transparency and quality assurance. Trustworthy suppliers are willing to share empirical data regarding the wear rates, energy consumption, and productivity improvements offered by their products, reinforcing the credibility of their claims.
In practice, optimizing grinding operations with the right type of balls can reduce downtime and operational costs by significantly lowering the frequency of replacement and repair. Harnessing detailed performance analyses and feedback loops in real-time operations further refine the choice and usage of grinding balls, aligning with evolving industrial requirements and environmental considerations.
In conclusion, whether your focus is on minimizing operational costs or optimizing production efficiency, understanding and utilizing the right grinding balls in ball mills is a sophisticated endeavor that blends experience, expertise, and empirical evidence. By choosing high-quality grinding balls tailored to specific operational needs, industries can enhance their milling processes and maintain a competitive edge.