Cast iron grinding balls have long been an essential component in the mining and cement industries, serving as the backbone of the grinding process. These spheres of hardened iron are indispensable for their efficiency in breaking down coarse materials into finer particles, facilitating smoother and more efficient extraction of valuable minerals or cement production. Companies operating in these sectors understand that investing in superior-quality grinding media is crucial for optimizing production capacities and cost-efficiency.
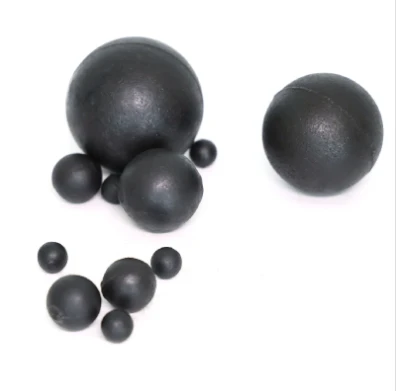
Mastering the art of manufacturing cast iron grinding balls involves a blend of expertise, precision, and a comprehensive knowledge of metallurgy. The production process typically starts with the careful selection of raw materials, where only the finest grades of cast iron are chosen. The next step involves melting the iron in electric arc furnaces and adjusting its chemical composition to enhance hardness and durability. A rapid cooling process, known as quenching, follows, allowing the iron balls to acquire a uniform microstructure essential for maintaining their form under high-impact conditions.
The authoritative differences that distinguish top-tier cast iron grinding balls from inferior versions lie in these intricate production details. Companies with experience in metallurgical processes ensure that their products meet industry standards for wear resistance and hardness, typically measuring between 55 to 65 HRC. This resistance translates directly into longer operational lifecycles and minimized downtime — factors that any mining or cement operation deems pivotal.
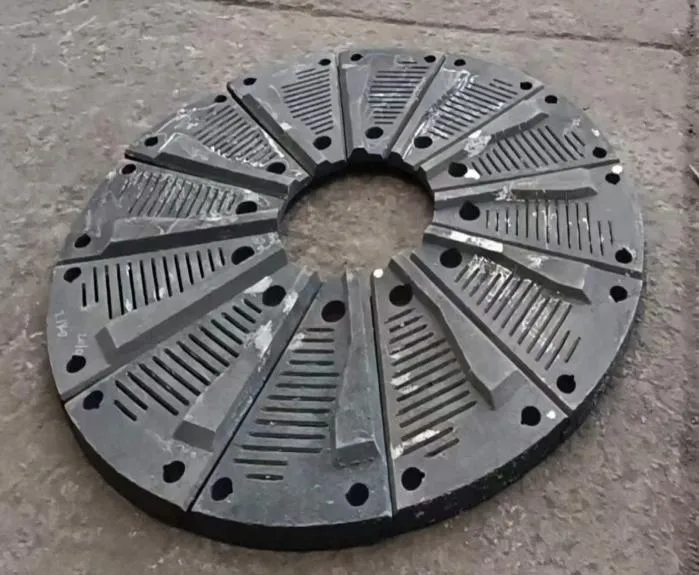
Trust forms the core of any long-term supplier relationship, especially in sectors where equipment failure can lead to significant financial loss. Vendors who offer cast iron grinding balls understand this deeply. Many of them provide detailed documentation and quality assurance reports to clients, showcasing a commitment to excellence. Partnering with firms that prioritize transparency and consistent quality control assures customers that they are making informed decisions, further solidifying trust.
bolas de molienda de hierro fundido
For end-users,
real-world experience quickly demonstrates the critical role these grinding balls play in daily operations. A plant manager overseeing a cement plant might recount how a switch to superior cast iron grinding balls reduced their grinding media consumption by over 20%, effectively saving costs. Similarly, in the mining sector, operators frequently report improved throughput and minimized wear on milling equipment, reducing maintenance demands.
Expertise in the field of metallurgy also feeds into the innovation of cast iron grinding balls, where continuous research and development foster improvements. This ongoing innovation can lead to the development of grinding balls with enhanced resistance to high-temperature environments, corrosion, and chemical exposure — aligning with evolving demands in industrial applications. Companies at the forefront of this innovation often partner with academic institutions, pushing the boundaries of knowledge and technology in metallurgy.
Moreover, sustainability has become a growing concern in heavy industries. Forward-thinking manufacturers of cast iron grinding balls are exploring eco-friendly alternatives, such as recycling scrap metals or utilizing sustainable energy in their production processes. In doing so, they contribute to a more sustainable industry model, addressing environmental concerns while maintaining product integrity.
In conclusion, the business of producing and supplying cast iron grinding balls is underpinned by a commitment to expertise, precise manufacturing processes, and an unwavering focus on quality and trust. Whether used in pulverizing ores or refining cement, the real-world experience of these spheres is testament to their critical role. Industry leaders not only rely on these robust grinding balls to improve their operations but also seek partnerships with trusted and innovative suppliers who will continue to meet the challenges of tomorrow’s industrial landscape.