In the vast realm of industrial machinery, particularly in sectors like mining and cement, the role of grinding balls for ball mills has become pivotal. The efficiency and productivity of these industries often hinge on the quality and performance of the grinding media employed. As someone deeply entrenched in this industry, I’ve witnessed firsthand the substantial impact that superior grinding balls can have on operational output and longevity of milling equipment.
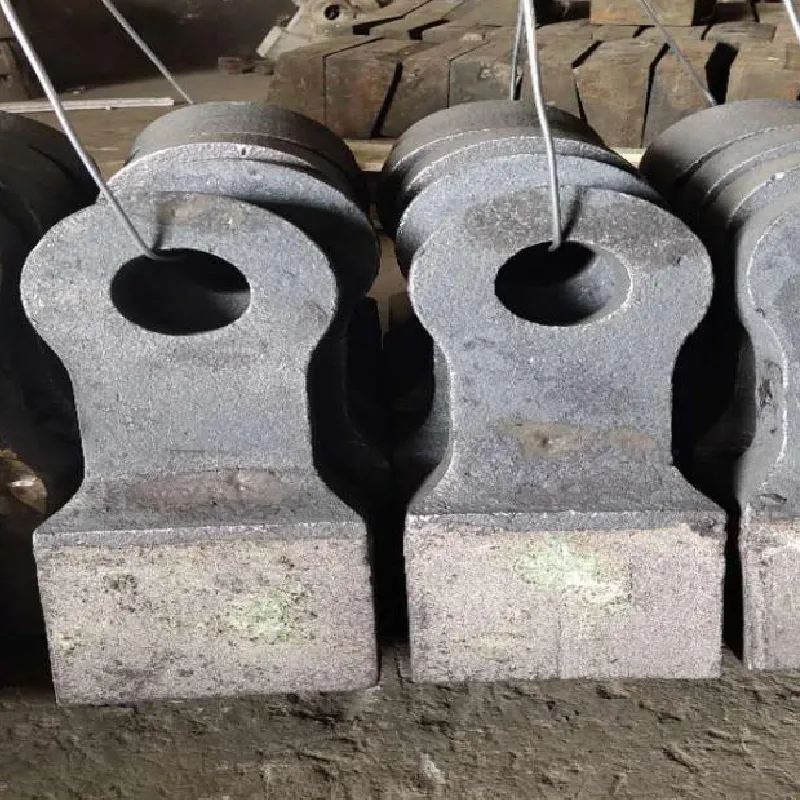
Grinding balls, specifically designed for ball mills, play a crucial role in material dispersion, grinding, and size reduction. These spherical elements need to withstand the operational rigors, such as high impact and abrasion, to effectively grind materials to the desired fineness and contribute to the production process. From my extensive industry experience, the choice of grinding balls often dictates the pace of operations and energy consumption, influencing overall cost efficiency.
The market today offers a variety of grinding balls, primarily categorized by material composition—steel, ceramic, and high chrome. Each material brings its unique set of advantages depending on the milling application
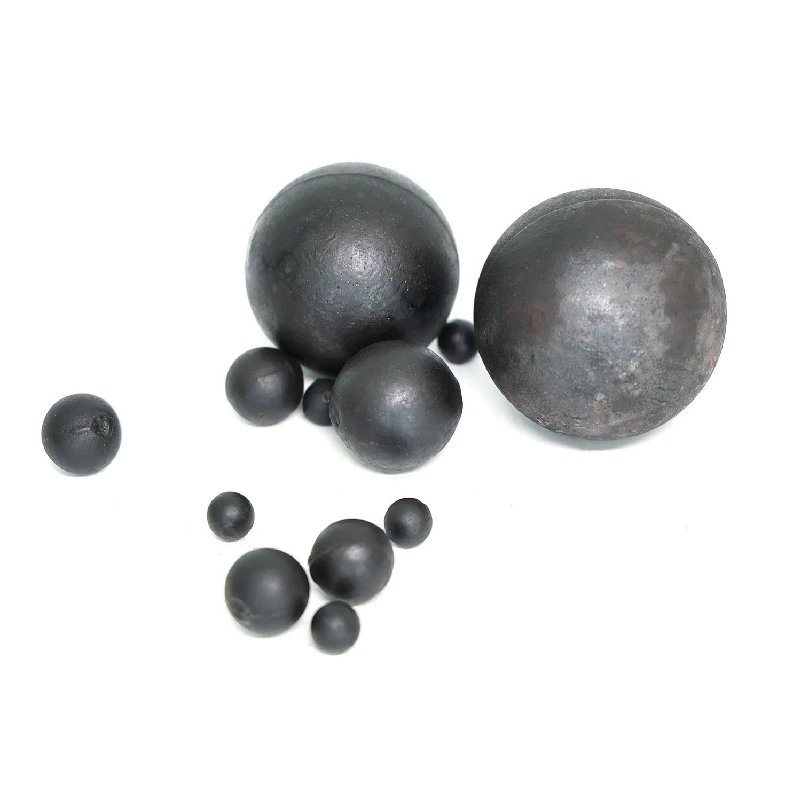
1. Steel Grinding Balls These are the most common and cost-effective option,
ideal for large-scale operations. With high hardness and tensile strength, steel balls ensure optimal grinding efficiency. I've noticed that when sourced from a reputable manufacturer, they offer excellent wear resistance, significantly minimizing downtime and maintenance costs.
2. Ceramic Grinding Balls Well-suited for applications where contamination by metal is a concern, ceramic balls provide high purity and corrosion resistance. Their lightweight nature reduces load on the mill, ultimately contributing to energy savings. In my experience, they are particularly useful in pharmaceuticals and food processing industries, where maintaining the integrity of the milled product is paramount.
3. High Chrome Grinding Balls Known for their superior wear resistance and anti-corrosive properties, high chrome balls are favored in milling processes involving aggressive materials. They've demonstrated exceptional longevity even in the most abrasive environments, making them a staple in heavy-duty mining operations.
bolas de molienda para molino de bolas
Selecting the right grinding balls for a specific milling task goes beyond mere functionality. It requires aligning the material type with the specific demands of the milling environment. Various parameters like ball size, material density, and milling speed must be precisely configured to meet operational goals. Engaging with technical consultants during this selection process can provide valuable insights tailored to the specificities of your industry.
Optimal usage of grinding balls also involves rigorous maintenance protocols. Regular monitoring of wear patterns, real-time analysis of milling output, and timely replenishment of grinding media can extend the life of both the balls and the mill itself. Implementing an automated monitoring system can significantly enhance operational reliability, as I’ve observed in several modernized facilities.
Trustworthiness and authority in this domain are underscored through adherence to internationally-recognized manufacturing standards. Certified grinding balls, compliant with ISO and ASTM standards, ensure unparalleled quality and performance. Partnering with suppliers known for stringent quality control not only guarantees product integrity but also elevates the overall credibility of the operation.
In an era where industrial efficiency is constantly challenged by economic and environmental factors, leveraging superior grinding technology can transform milling operations. By investing in high-quality grinding balls that meet rigorous performance criteria, industries can boost productivity, reduce energy consumption, and ultimately contribute to sustainable practices.
For industry professionals contemplating a strategic overhaul of their milling operations, comprehensive knowledge, and guidance in selecting the appropriate grinding media cannot be overstated. Whether the focus is on enhancing production throughput or achieving finer material specifications, embracing advanced grinding solutions heralds a new era of industrial innovation and profitability.