In the world of industrial manufacturing, the efficiency and effectiveness of material processing can significantly determine operational costs and product quality. One indispensable component in this process is the grinding ball, or boules de broyage. These spherical tools play a pivotal role in the pulverization process, impacting the final texture and composition of the materials they help produce.
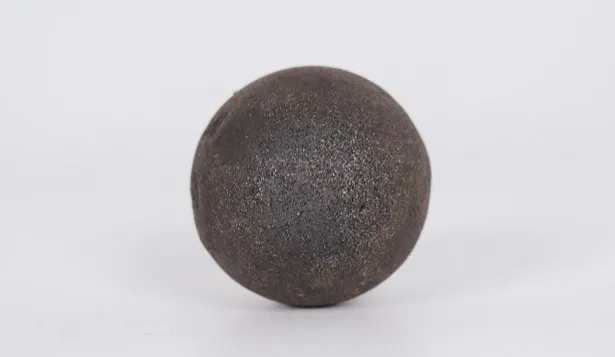
Experience underscores that the right choice of grinding balls can drastically alter the productivity and output quality in sectors ranging from cement production to mineral processing. In industries like these, both the material of the balls and their operational performance are constantly scrutinized to maintain high-quality outputs. For instance, in cement plants, where every minute of downtime can result in substantial revenue loss, the reliability of grinding media is critical. Companies have reported that switching to high-quality balls tailored to their specific needs not only extends the lifespan of their mills but also reduces operational anomalies, directly contributing to the bottom line.
Expertise in the selection and use of grinding balls begins with understanding the materials. The typical choices include steel, ceramic, and even certain types of advanced composites. Each of these has its specific advantages steel balls, noted for their durability and strength, are ideal for heavy-duty applications that require high-impact resistance. Conversely, ceramic balls are preferable in scenarios where chemical stability and wear resistance are prioritized over impact resistance. The choice of material, therefore, must align with the demands of the specific task, whether it be the grinding of ores, pigments, or any other industrial material.
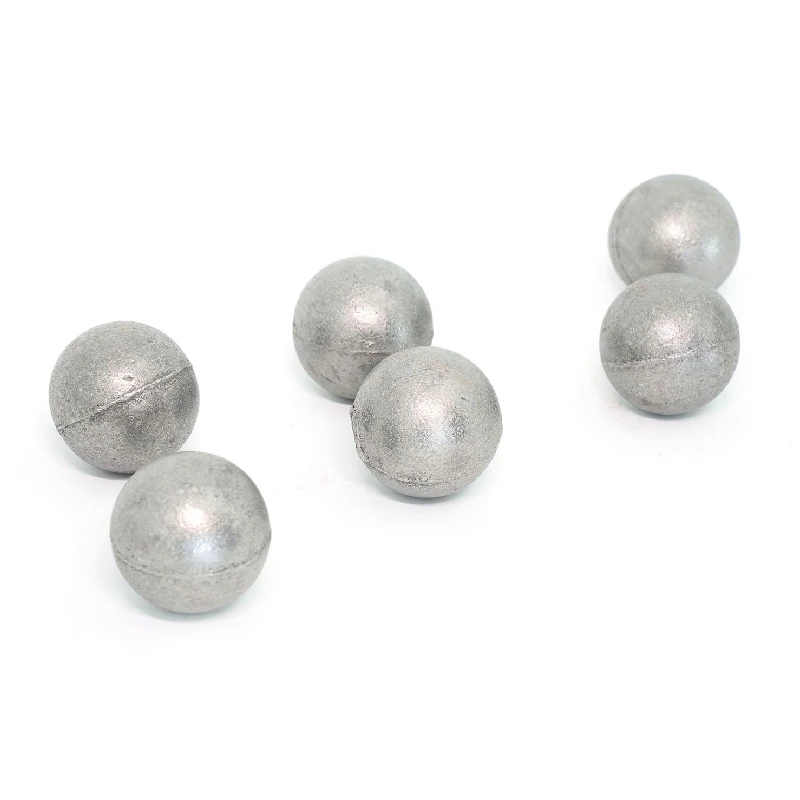
Authoritativeness in the sphere of grinding media is not just about selecting the right balls but also understanding the micromechanics of milling. What distinguishes seasoned professionals from novices is the ability to tailor the milling process itself—adjusting the rotational speed, the ball-to-material ratio, or the fraction of ball load. Advanced industry players impart their strategies and findings through conferences and publications, sharing insights on how varying these parameters can influence the kinetic energy of collisions and therefore the efficiency of the grinding process. With ongoing research and development, cutting-edge innovations—such as nanostructured materials—are introduced to enhance the performance standards of traditional grinding media.
boules de broyage
To establish trustworthiness in this domain, manufacturers must commit to transparency and rigorous quality assurance protocols. This extends from the initial sourcing of raw materials to the final production and supply of grinding balls.
Each batch should undergo comprehensive testing for sphericity, hardness, and wear resistance. End users, particularly those in critical sectors like pharmaceuticals where contamination could have dire consequences, should look for suppliers who not only comply with international standards (such as ISO certifications) but also offer full traceability of their products.
The integration of data analytics and IoT technologies into the maintenance and monitoring of grinding processes further enhances trust by allowing real-time monitoring and predictive maintenance. By leveraging these technologies, plant operators can predict wear and tear before it becomes a critical issue, ensuring uninterrupted production and optimal efficiency. Such proactive measures, when shared with industry peers, contribute to a collective advancement in the field, fostering a collaborative environment where information and experiences can be freely exchanged for mutual benefit.
In conclusion, the intricate world of boules de broyage holds a significant place in modern industrial processes, demanding a confluence of experience, expertise, authoritativeness, and trustworthiness to navigate effectively. By continually integrating cutting-edge technology with foundational knowledge, companies can refine their methodologies, resulting in improved productivity and product quality. For those seeking to excel, a hands-on approach grounded in continuous learning and adaptation is not just advantageous—it is essential.