Ceramic balls have revolutionized the efficiency and versatility of ball milling processes across various industries. As an expert with extensive experience in material science and industrial processing, I have witnessed firsthand the transformative impact these small, precision-engineered spheres have had, enhancing both performance and product quality.
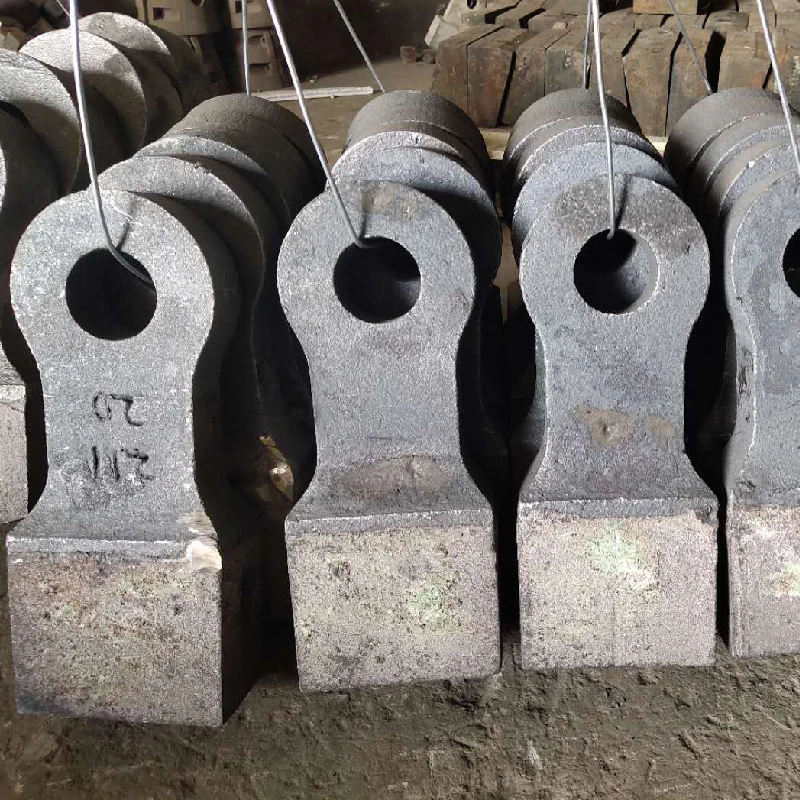
At a glance, ceramic balls might seem like a simple component, but they play a critical role in ball mills, machines designed for grinding and blending materials. In applications ranging from pharmaceuticals and food production to mining and metallurgy, the choice of grinding media is vital, and ceramic offers distinct advantages.
In terms of expertise, ceramic balls provide impressive wear resistance compared to steel balls or other media. Modern ceramic materials, crafted from alumina, zirconia, or silicon nitride, exhibit significantly higher hardness, measured at Mohs scales of up to nine. This hardness translates into reduced wear on both the balls and the mill itself, ensuring longer equipment life and reduced operational downtime, crucial in environments where continuous operation is key.
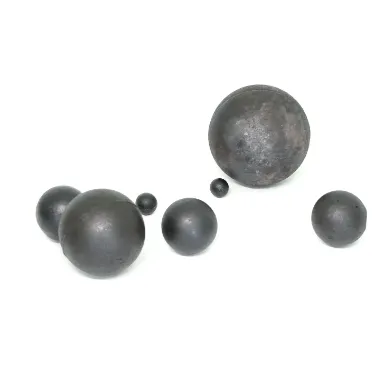
Moreover, the chemical inertness of ceramics endows them with superior resistance to various chemicals and corrosive environments. In industries where contamination is a concern—such as food processing or pharmaceutical production—ceramic balls are indispensable. Their non-reactive nature prevents unwanted chemical interactions, safeguarding the purity and integrity of the product.
From an authoritative perspective, numerous studies and industrial trials underscore the superiority of ceramic balls in specific applications. For example, in mining operations where processes demand constant, high-intensity grinding, ceramic balls have consistently outperformed traditional steel media. In these demanding conditions, ceramics’ thermal stability ensures consistent performance and energy efficiency at elevated temperatures.
ceramic balls for ball mill
Trustworthiness is also paramount. Leading manufacturers subject ceramic balls to rigorous quality controls, ensuring each batch meets stringent specifications for size, sphericity, and material composition. This assurance of quality is critical, especially in high-precision milling conditions where any deviation can lead to drastic changes in product outcome. Customers and engineers in the industry should rely on reputable brands with proven track records, ensuring that their milling processes are as efficient and reliable as possible.
Personal experience has shown me the tangible benefits of transitioning to ceramic balls in various milling operations. Initially perceived as an expensive option, the return on investment quickly becomes evident. Reduced equipment wear means lower maintenance costs and less frequent replacement of parts. Moreover, the consistent particle size distribution achievable with ceramic media enhances product quality, leading to better downstream efficiency and reduced wastage.
For businesses keen on optimizing their milling process, coating ceramic balls with specialized substances can offer additional customizability. Such coatings can further enhance wear resistance or alter other performance characteristics tailored to specific milling situations. As research continues to advance in material science, we can expect even more specialized formulations of ceramic balls that cater to increasingly niche and demanding applications.
In conclusion,
ceramic balls represent an investment in quality, reliability, and efficiency for ball milling operations. By embracing the benefits they offer, industries can achieve superior grinding performance, reduce operational costs, and produce high-quality products that meet market demands. Their role as a pivotal component in modern milling solutions cannot be understated, making them a prime choice for forward-thinking operations.