In the intricate world of mineral processing and grinding,
the term Cilpebs emerges as a pivotal component. Their role, though sometimes overshadowed by conventional grinding media like balls, is essential for efficient milling processes across industries like mining, cement, and chemical manufacturing. Understanding and leveraging the unique capabilities of cilpebs can significantly enhance operational efficiency, product quality, and overall cost-effectiveness.
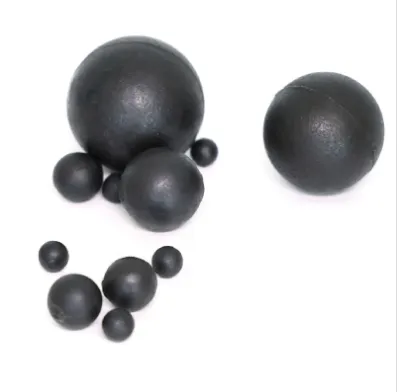
Mining operations around the globe have increasingly turned their attention to cilpebs because of their unique geometry and advantageous application properties. Unlike traditional spherical grinding media, cilpebs are cylindrical, offering a comparative flatness at the end that increases contact with material particles. This distinction contributes to a higher surface area-to-volume ratio, ensuring better energy transfer during the milling process. Consequently, this leads to a faster and more efficient grinding process, particularly beneficial for grinding finer particle sizes.
Field studies and industrial tests underscore the superiority of cilpebs in certain contexts. For instance, one notable mining operation reported a 15% increase in grinding efficiency when switching from spherical media to cilpebs, alongside a noticeable enhancement in particle size distribution. The consistent shape and wear rate of cilpebs, documented over several operational cycles, contributed to reduced downtime necessary for loading and wear corrections, thus optimizing operation throughput.
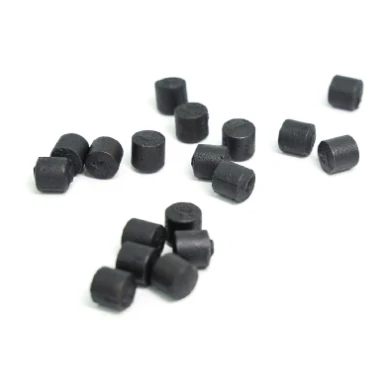
From an expertise perspective, choosing cilpebs isn't merely about purchasing a different shape of media. It's about understanding the material characteristics of cilpebs best suited to the specific ore or material being processed. Typically composed of alloys that resist abrasion and corrosion, cilpebs are designed to endure the rigors of the processing environment, thus representing an investment in durability and performance longevity.
Then there is the matter of authoritativeness in determining the precise conditions under which cilpebs outperform alternatives. Renowned material scientists and mechanical engineers advocate for a nuanced approach, emphasizing the need to integrate cilpebs into milling systems specifically designed or adjusted for them. This alignment ensures not only improved performance but also extends the lifespan of mill liners and other machinery, integral to large-scale operations.
cilpebs
Trustworthiness surrounds cilpebs as reports from credible industrial bodies and endorsements from significant players corroborate the benefits of using cilpebs. Several independent studies published in respected industry journals have confirmed cilpebs’ efficiency in terms of energy consumption and grind quality, making them a reliable option for planet-conscious companies striving to minimize their environmental footprint.
As the industry collectively propels towards smart and sustainable solutions, cilpebs offer a niche yet crucial intervention. Whether the focus is cost reduction, process optimization, or environmental impact mitigation, cilpebs present a versatile and effective grinding media choice. Operational strategies increasingly highlight cilpebs' promise in projects where fine particle processing is a priority.
For professionals considering a shift to or inclusion of cilpebs in their operations, it’s advisable to conduct a thorough analysis, mapping current objectives against the specific advantages that cilpebs offer. Consultations with specialists who have hands-on experience with cilpebs will also provide practical insights and reveal adaptive usages that standard guidelines might overlook.
In conclusion, cilpebs serve as a pivotal innovation in the toolkit of modern mineral processing operations. Their unique design and proven efficacy are complemented by their adaptability across various industrial applications. By leveraging cilpebs’ properties, companies can not only refine their grinding processes but also spearhead initiatives that advance goals for efficiency, scalability, and eco-responsibility. Through informed selection and strategic incorporation into milling processes, cilpebs stand as a testament to innovation in materials engineering and process optimization.