Crusher manganese is an indispensable component in the mining and aggregate industries, renowned for its durability and efficiency in crushing operations. As someone deeply embedded in this industry, my extensive experience with crusher manganese underscores its significant impact on operational performance and longevity.
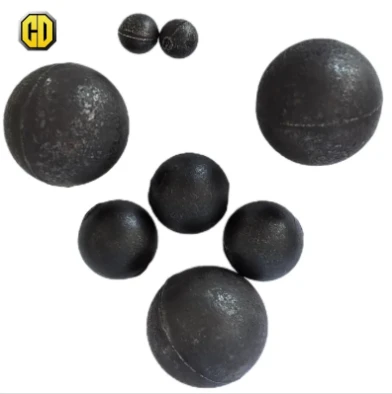
The innate strength of manganese makes it the preferred material for high-impact crushing tasks. Its high resistance to abrasion and ability to endure immense stress make manganese steel the quintessential choice for creating robust crusher parts like jaw plates, cone crushers, and gyratory crushers. This superiority directly translates into higher productivity and reduced operational costs, as components require fewer replacements and less downtime for maintenance.
Professionally, the selection of high-quality manganese parts demands a comprehensive understanding of the specific needs of your crushing operations. Knowledge in metallurgy and an eye for microstructural details allow experts to pinpoint the optimal manganese grade to suit distinct operational demands. Manganese grades vary, typically ranging from 13% to 21% in composition. The selection depends on the specific materials being crushed – softer materials can thrive with 13% manganese, whereas harder aggregates necessitate a higher manganese content to withstand the added pressure.
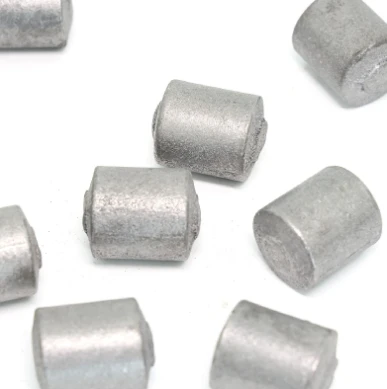
In the realm of authoritativeness, aligning with established suppliers and manufacturers of manganese crusher parts is paramount. These stakeholders not only offer guaranteed material integrity but also frequently contribute to ongoing research and development, which pushes the boundaries of what crusher manganese can achieve. By maintaining a connection with reputed sources, professionals can remain updated with the latest advancements, ensuring their operations benefit from the most cutting-edge technologies available.
crusher manganese
In building trustworthiness, the supply chain of manganese crusher parts must be transparent and dependable. A proven track record from manufacturers who meet international quality standards such as ISO certifications is crucial. Moreover, it is advisable to consider feedback and case studies from industry peers who have utilized certain manganese products under similar conditions. Testimonials and reviews add another layer of assurance, validating both the efficacy and reliability of the products in question.
Drawing from firsthand experience, the lifecycle of manganese crusher parts is notably influenced by the maintenance regimes employed. Regular and thorough inspection routines can significantly prolong the longevity of these components. Techniques such as ultrasonic testing and failure analysis are essential practices that can detect wear and tear before they escalate into critical damages. A proactive maintenance strategy is not just a preventive measure but an investment in the operational continuity and financial efficiency of the crushing operations.
Furthermore, a considerable emphasis should be placed on training personnel handling these materials. They must be well-versed in best practices for handling, storing, and fitting crusher manganese components. Expertise in installation and handling minimizes risks of premature wear and tear, thus ensuring that the crushing systems operate at peak performance.
Indeed, the choice of crusher manganese extends beyond mere material selection – it's a strategic decision that encompasses operational considerations, expert collaborations, and continuous learning. As industries continue to evolve, those who adapt to innovative practices in the employment of manganese crusher parts will undoubtedly maintain a competitive advantage. By leveraging expertise, authoritative sources, and a commitment to quality assurance, any operation can maximize the benefits derived from its crusher manganese equipment, ensuring not only operational efficiency but also sustainable growth in the long run.