High-chromium grinding cylpebs have carved a niche in industry sectors ranging from mining to cement production, where their robust characteristics significantly enhance grinding efficiency. Through a blend of firsthand experiences and professional expertise, this article delves into the multifaceted benefits of high-chromium grinding cylpebs, underscoring their dominant role in improving operational outcomes.
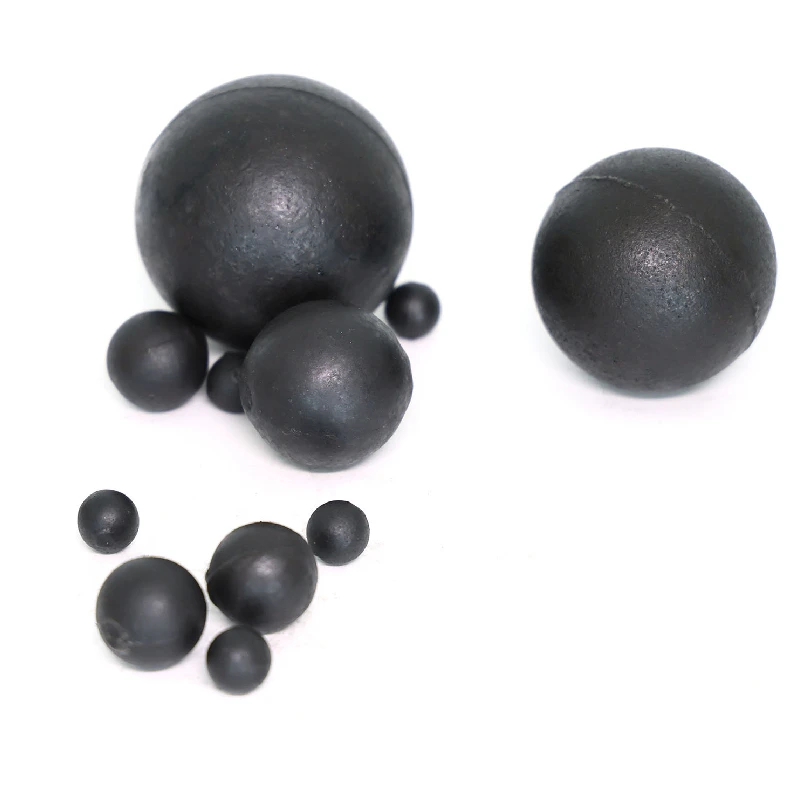
To envision their impact, consider the challenging environments of mining and cement industries. Both of these sectors demand high-intensity grinding processes that can effectively handle abrasive materials. High-chromium grinding cylpebs, known for their exceptional hardness and wear resistance, cater precisely to these rigorous demands. Engineers and plant managers have consistently reported a noticeable improvement in grinding efficiency and a corresponding decrease in operational costs upon switching to high-chromium variants.
The key to the superior performance of high-chromium grinding cylpebs lies in their material composition.
Rich in chromium content, these cylpebs exhibit enhanced durability. In practice, this translates to a longer service life compared to low or medium chromium alternatives. A comprehensive understanding of metallurgical properties allows manufacturers to tailor cylpebs for specific operational needs, enhancing their authority in industry applications.
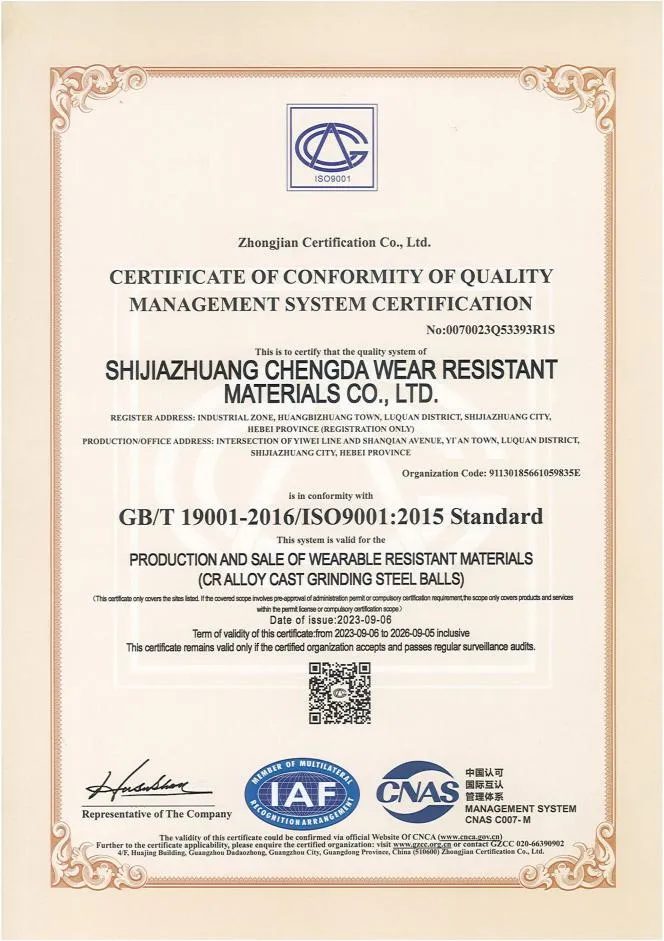
Moreover, their consistent performance has fostered trustworthiness among users who are assured of both the quality and reliability of the grinding process. Operators frequently express satisfaction with reduced downtime and improved throughput, as these cylpebs endure the harsh grinding environment, maintaining their integrity over extended periods. This reliability not only boosts productivity but also reinforces the operational trust plant managers place in their machinery.
High chromium grinding cylpebs
Experts in the industry often accentuate the advanced production techniques involved in crafting high-chromium grinding cylpebs. Highly controlled casting processes ensure uniform hardness throughout each cylpeb, maximizing their efficiency in breaking down materials. This process illustrates the expertise inherent in their manufacture, as even slight deviations can significantly impact performance.
Additionally, the environmental impact of choosing high-chromium grinding cylpebs should not be overlooked. Their durability reduces the frequency of replacement, thereby minimizing waste and contributing to sustainable operations. In contexts where environmental concerns are paramount, such as regulated mining operations, this characteristic is notably advantageous.
The authoritative stance established by reputable manufacturers in the field is another critical aspect, as evidenced by certifications and compliance with international standards. This adherence to rigorous quality controls underscores the credibility of high-chromium grinding cylpebs, ensuring they meet the demanding expectations of various applications.
In summary, the adoption of high-chromium grinding cylpebs aligns with industry movements towards efficiency, reliability, and sustainability. Their superior performance, derived from expert material selection and advanced manufacturing processes, reinforces their position as indispensable assets in critical grinding operations. As industries continue to evolve, the role of high-chromium grinding cylpebs in optimizing operational processes will undoubtedly become even more pronounced, guided by a foundation of experiential success and expert validation. Embracing these cylpebs is not merely a choice for immediate performance enhancement but an investment in long-term operational excellence.