Grinding media steel spheres, commonly employed in various industrial milling processes, are vital components in the manufacturing sector. Their primary role is to aid in the breakdown of materials, enhancing production efficiency and product quality. This article dives into the intricacies and benefits of using steel spheres in milling applications, pinpointing key aspects that affirm their indispensability and utility across industries.
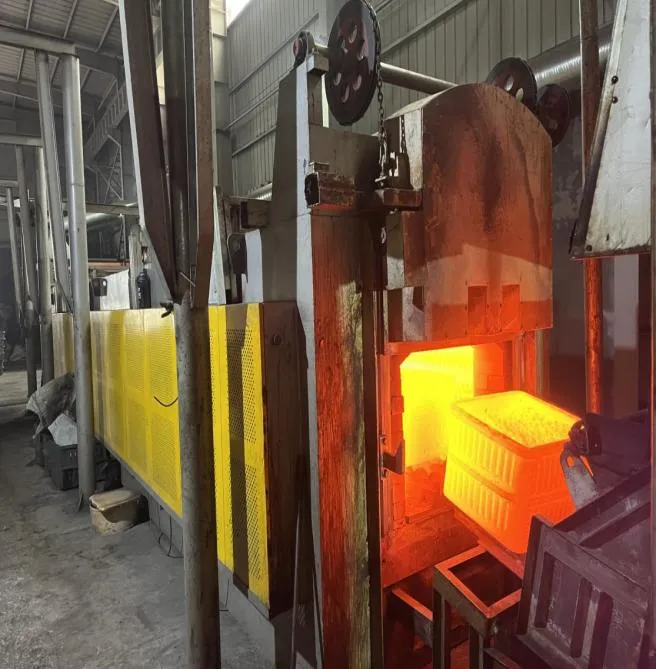
Precision and efficiency hallmark the production of grinding media steel spheres. Manufacturers employ cutting-edge technologies to ensure these spheres meet stringent industrial standards. The spheres' dimension, density, and wear resistance significantly influence the grinding process. In industries such as cement, mining, and chemical processing, the uniformity of the grind dictates the quality of the final product. Steel spheres contribute to this uniformity by offering consistent impact force and reduced energy consumption, making them an ideal choice for these demanding applications.
Steel's inherent properties—such as its strength, toughness, and resilience—make it a preferred material for grinding media. When employed in milling processes, steel ensures longevity and robustness, factors critical for withstanding the rigorous impacts within grinding mills. The hardened surface of these spheres stands up to the wear and tear of continuous operation, translating into longer service life and cost-efficiency for industrial operations. Manufacturers opting for steel media address both operational efficiency and bottom-line profitability, given the reduction in downtime and maintenance costs.
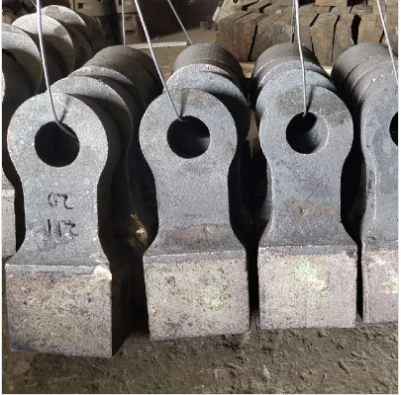
Real-life case studies further bolster the credibility of steel grinding media. For example, a leading cement production company reported a 15% boost in grinding efficiency following a transition from traditional ceramic beads to steel spheres. The steel grinding media not only enhanced the milling process but also brought about significant reductions in energy consumption and operational costs, adding to its merits as a dependable solution in material size reduction.
steel ball of grinding media
From an expertise standpoint, understanding the dynamic behavior of grinding media steel spheres is crucial. Specialists in metallurgy and industrial manufacturing continuously explore ways to optimize sphere formulations, tailoring them for specific applications or unique material characteristics. This ongoing research and development drive underscores the expertise manufacturers bring to the table, ensuring that customers receive products that align with the evolving demands of modern industrial processes.
In terms of authoritativeness, industry standards and certification processes validate the top-tier quality of steel spheres. Trusted organizations like the International Organization for Standardization (ISO) offer frameworks ensuring these products meet global safety and quality standards. Compliance with such standards attests to the manufacturer's commitment to delivering reliable solutions that meet the end-user's needs while setting a benchmark for quality in the industry.
Trustworthiness, an indispensable trait for any industrial product, is central to the value proposition of steel grinding spheres. Suppliers often establish longstanding relationships with clients, built on a foundation of delivering consistent quality and performance. Reliable customer service and warranty offerings further enhance trust, providing clients peace of mind that their processes are supported by dependable manufacturing tools.
The integration of grinding media steel spheres in industrial applications embodies the convergence of engineering excellence, material science, and industry acumen. Their versatility and proven effectiveness pave the way for optimized manufacturing processes, serving as a testament to their role as a backbone in the industrial production landscape. Businesses looking to enhance operational efficiency and product quality should consider the invaluable contributions of steel spheres to their grinding and milling needs.