A grinding media ball factory is not just a production unit; it is a hub of technological advancement and precision engineering. The success of any grinding process lies in the quality and design of the grinding media utilized, making the focus on grinding media ball factories critically important for industries relying on this machinery.
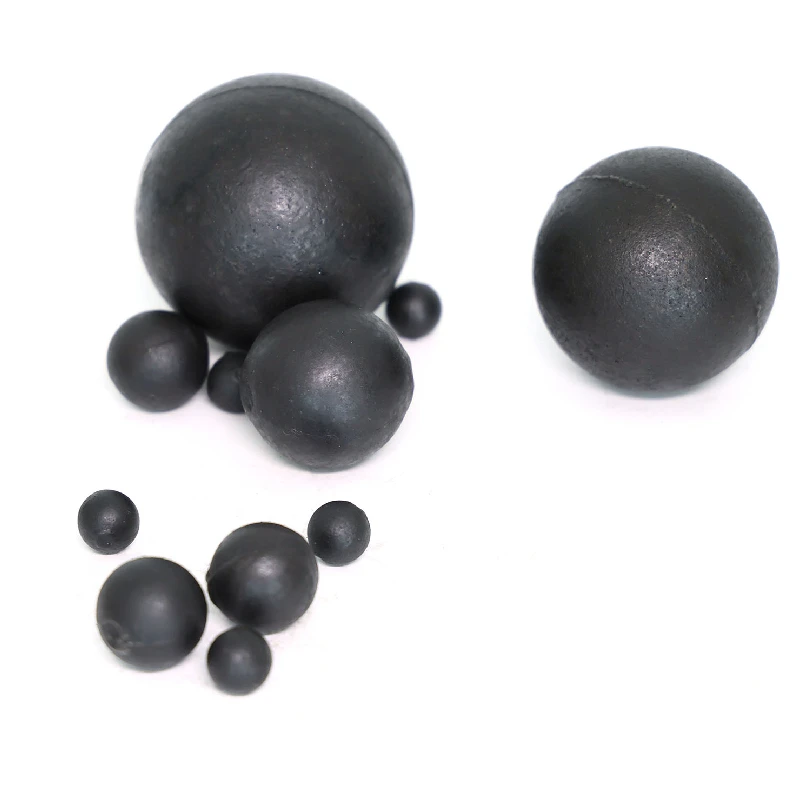
Located in industrial zones, these factories are equipped with state-of-the-art machinery capable of producing a wide variety of grinding media balls. These factories typically focus on producing high-quality balls, essential for the mining, cement, and chemical industries, among others. The production process of these balls involves numerous steps, including forging, casting, and rolling, each crucial in determining the quality and durability of the final product.
The expertise required in a grinding media ball factory is extensive. Professionals working in these factories are often seasoned metallurgists and engineers, who possess a deep understanding of material properties and metallurgical processes. This technical expertise ensures that the balls produced can withstand the heavy loads and abrasive environments they will encounter in various grinding applications.
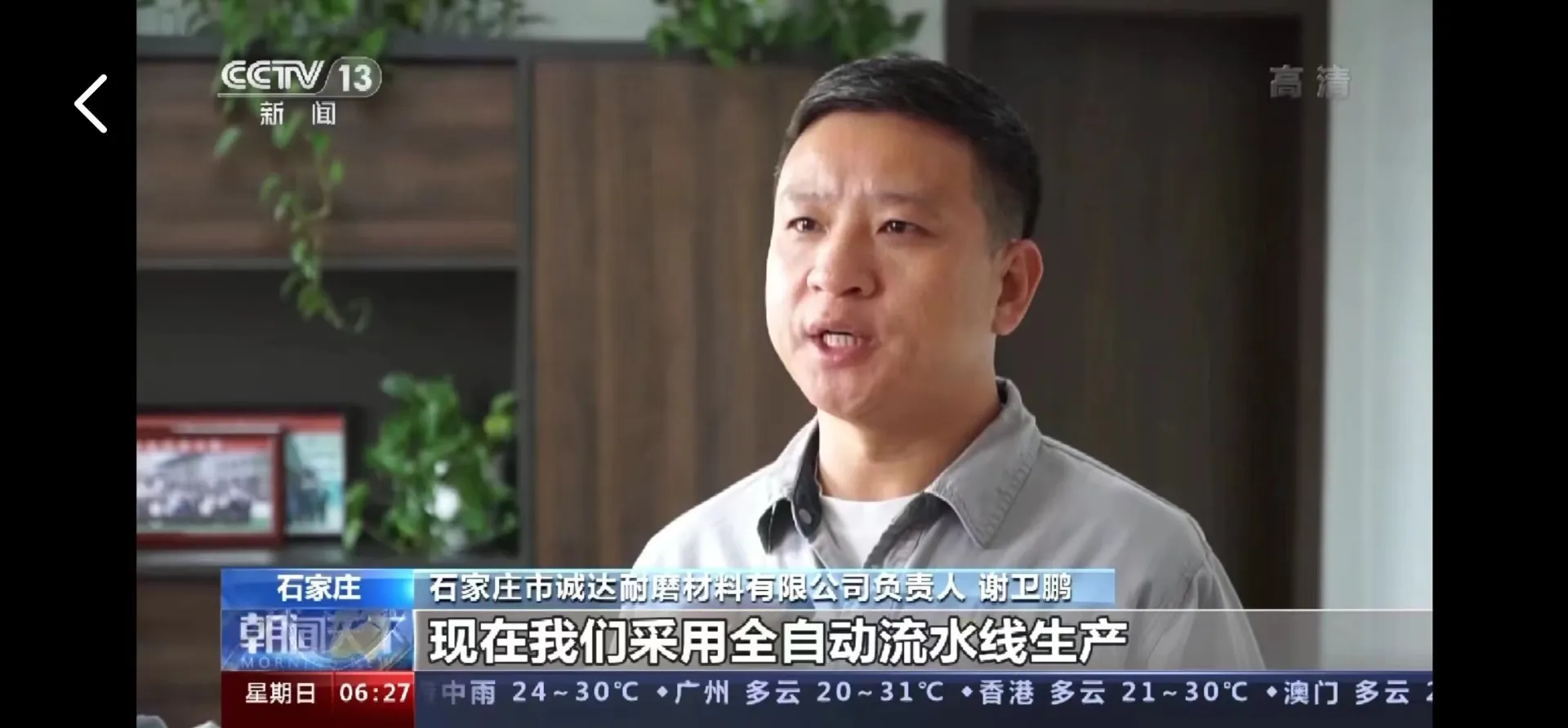
Factories strive to achieve the highest standards in their production processes, implementing stringent quality control measures. Each ball produced is subject to rigorous testing procedures, ensuring its consistency in size, shape, and hardness—factors that greatly affect grinding efficiency. These comprehensive quality checks are not only a testament to the factory's commitment to excellence but also a crucial element in building trust with their clients.
Authoritativeness in this field comes from years of accumulated research and practical experience. Leading grinding media ball factories invest heavily in research and development to continuously improve their products and adapt to the ever-evolving needs of the industries they serve. This investment in innovation reinforces their position as industry leaders and paves the way for new technologies that improve efficiency and reduce operational costs for their clients.
grinding ball factory
Furthermore, the credibility of these factories is bolstered by certifications from international quality assurance bodies. Holding certifications such as ISO 9001 not only ensures that the production processes meet international standards but also confirms the factory’s commitment to continual improvement and customer satisfaction. Clients can trust these factories to offer products that meet the highest levels of safety and performance.
Taking a closer look into the manufacturing process, the use of modern technological advancements like computer-aided design (CAD) and computer-aided manufacturing (CAM) plays a vital role in the design and production of grinding media balls. These technologies enable factories to produce balls with superior geometric precision, which directly translates to improved product lifespan and grinding performance.
Experience, expertise, authoritativeness, and trustworthiness intersect seamlessly in grinding media ball factories, making them indispensable to their industrial clients. As these factories continue to evolve, their focus remains on producing premium products that not only meet but exceed industry standards. Collaborations with clients ensure that specific needs are addressed, leading to the customization of products that perfectly suit diverse applications.
The commitment to sustainability is another significant aspect of modern grinding media ball factories. Many of these factories are adopting environmentally friendly production processes, utilizing renewable energy sources, and implementing waste reduction techniques. This not only reflects their responsibility towards the environment but also their dedication to maintaining high ethical standards.
In conclusion, a grinding media ball factory, with its blend of advanced technology, expert knowledge, and commitment to quality, plays a pivotal role in supporting the efficiency and success of various industrial applications. Their unwavering dedication to innovation and sustainability ensures that they remain at the forefront of engineering excellence, providing clients with products they can trust to perform under the most demanding conditions.