Navigating the complexities of the grinding cylpebs industry requires a comprehensive understanding of various aspects that relate to production, quality assurance, and market demands. A cutting-edge grinding cylpebs factory stands at the forefront of innovation and efficiency, producing high-quality grinding media optimized for a plethora of industrial applications across the globe.

The primary advantage of grinding cylpebs over traditional spherical grinding balls lies in their geometric design. Cylpebs have a larger surface area and a consistent shape that ensures more effective grinding processes. This characteristic translates directly into reduced energy consumption in milling operations—a critical consideration for industries looking to optimize cost while enhancing output. Scientific experts in materials engineering and metallurgy have analyzed these benefits, emphasizing the importance of precision in the manufacturing process to achieve uniform hardness and desired metallurgical properties.
A high-functioning factory incorporates sophisticated production technologies that leverage mechanized and automated systems. Each stage of the manufacturing process is defined by stringent quality control protocols that ensure consistency and reliability in the final product. Renowned factories harness advanced heat treatment techniques, which are pivotal in conferring the required physical properties to the cylpebs, such as toughness, durability, and resistance to breakage.
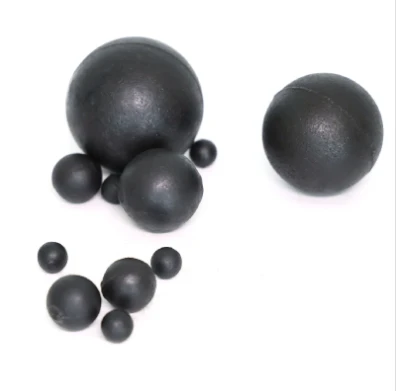
Incorporating experience into manufacturing practices also involves long-term partnerships with research institutes and continuous feedback loops from real-world applications. This synergy allows for ongoing refinement in the alloy compositions and heat-treatment processes employed during production. Expertise stems from a tireless pursuit of technological advancements and a deep commitment to adopting sustainable manufacturing practices. These elements appeal to environmentally conscious industries and contribute to stronger regulatory compliance related to the production and use of industrial media.
grinding cylpebs factory
Recognized authority in the field comes from certifications and adherence to international standards like ISO 9001, which assures clients of a manufacturing process that consistently meets the quality management requirements on a global scale. This guarantees customers not merely a promise of quality but a verifiable track record of delivering products that surpass expectations.
Trustworthiness is built through transparent business practices, where client education and continuous support are as important as product sales. Top-tier grinding cylpebs factories undertake rigorous testing both in-house and in partnership with independent laboratories to confirm that each batch meets specified performance criteria before reaching the customer. This level of due diligence fosters long-term client relationships characterized by reliability and trust.
In this fiercely competitive market, a grinding cylpebs factory that combines experience, expertise, authority, and trustworthiness positions itself uniquely. Providing clients with tailored solutions, based not just on current needs but also anticipating future demands, establishes a foundation for enduring partnerships. Whether it’s for mining operations, cement, or other industrial milling processes, a critical factor in choosing a supplier remains their commitment to continuous improvement and willingness to innovate.
Ultimately, what sets a foremost grinding cylpebs factory apart is its unwavering dedication to advancing its products and services in alignment with the evolving landscape of the industrial sector. As industries face increasing pressure to enhance efficiency and reduce operational costs, the need for a reliable and innovative partner becomes paramount. Factories that embody these qualities play a pivotal role in supporting the economic and operational goals of the myriad sectors they serve.