Sand milling, often recognized within the industry as a critical process for producing fine particles from coarse components, demands a unique amalgamation of knowledge, experience, and authority. It’s not merely about breaking down materials but preserving their intrinsic qualities while achieving desired quality standards. For decades, sand milling has been the cornerstone of many production lines, lending its expertise to sectors ranging from construction to manufacturing.
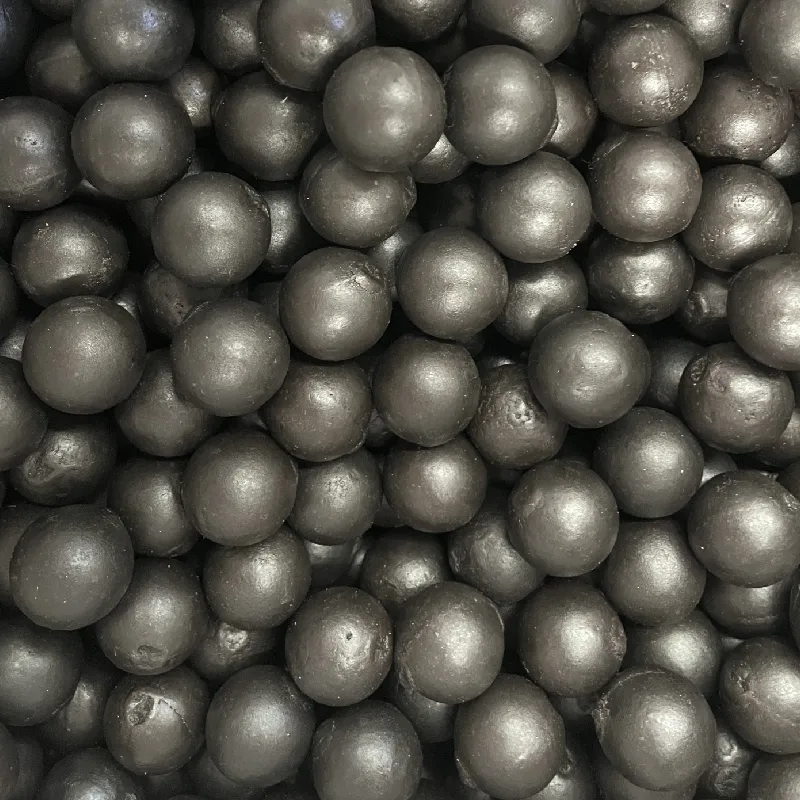
This narrative draws from a deep well of hands-on experience and authoritative expertise that sheds light on the nuances of sand milling. At its core, the process involves the mechanical grinding of sand grains into finer aggregates, optimizing them for diverse applications such as building materials, glass production, and even artisanal crafts.
The journey into sand milling begins with selecting the appropriate raw material. Experts in this field understand that the type of sand—be it quartz,
olivine, or river sand—can significantly affect the final product's texture, strength, and performance. Precision in selection revolves around the intended application; for instance, construction-grade sands require robust, angular grains for superior binding, while glass production might favor more refined, pure silica sand.
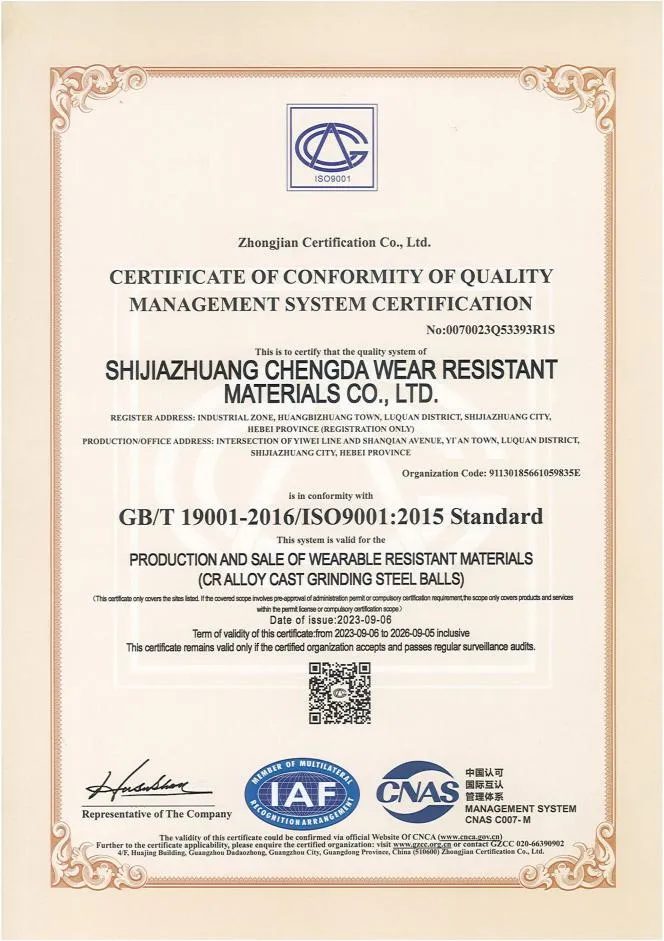
Once selected, the real craft lies in the milling process itself. It extends beyond mere grinding to encompass a spectrum of technologies and methodologies. Ball mills, rod mills, and high-pressure roller mills are all integral to the industry. Yet, each offers distinct advantages and potential drawbacks. Ball mills, with their rounded grinding elements, are celebrated for their efficiency in achieving uniformly coarse particles. Conversely, rod mills are prized for their ability to minimize over-grinding, which is crucial for applications demanding precise particle size distribution.
Advanced practitioners of sand milling are attuned to the intricacies of machine operation, such as rotational speed, grinding media size, and milling duration. Mastery in these parameters translates into not just efficiency but also reliability and consistency of the output. This expertise is critical, as even subtle deviations can cascade into significant product failures, especially in technical applications like semiconductor manufacturing.
фрезерование песка
Moreover, authority in the field is wielded by those who prioritize sustainability and environmental considerations. Modern sand milling practices actively engage in recycling waste products and reducing the ecological footprint. This includes implementing dust collection systems, reusing water, and optimizing energy consumption, reflecting an evolving trend towards greener manufacturing processes.
Trust in sand milling enterprises is built through rigorous adherence to quality standards and certifications. Trusted milling operations employ comprehensive testing protocols to ensure each batch meets specified criteria. Clients often seek ISO-certified companies, as such certifications underscore a commitment to quality and reliability.
Finally, trustworthiness is further reinforced through transparent customer relations. Leading firms maintain open lines of communication, offering detailed insights into their processes, challenges, and innovations. Regular updates and information dissemination help nurture client relationships, establishing a reputation for honesty and integrity.
In conclusion, sand milling is more than just a process—it's a refined skill demanding profound experience, specialized expertise, and inherent authority. It thrives on trust, bolstered by a commitment to sustainable practices and unwavering quality control. As industries continue to evolve, sand milling remains an indispensable component, driving innovation and excellence in product refinement across the globe.