The enigmatic allure of kugelmühlenkugeln, also known as grinding balls used in ball mills, continues to captivate industries striving for excellence in production processes. These spherical wonders, integral to efficient milling solutions, represent a fascinating intersection of engineering innovation and material science.
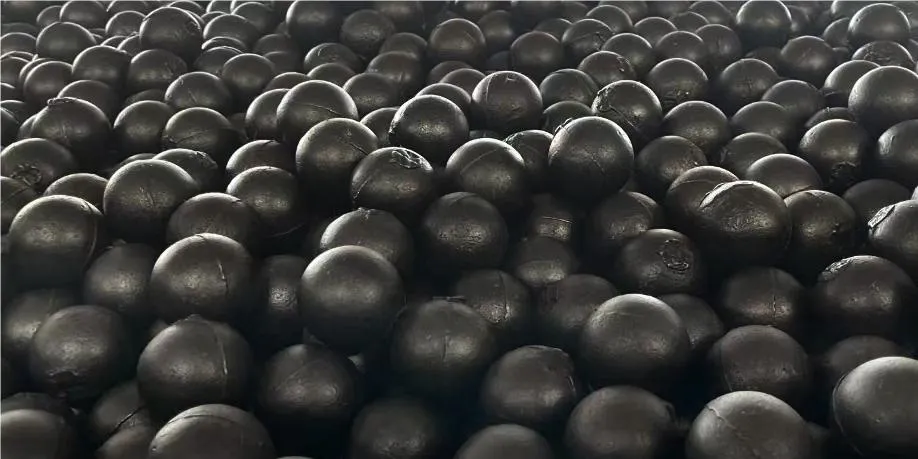
The precision engineering behind kugelmühlenkugeln is critical. Crafted from high-grade materials such as hardened steel, ceramics, or specific polymers, each ball undergoes rigorous manufacturing processes to meet the stringent standards of hardness and wear resistance. The exact composition selected impacts the performance of the milling process, affecting everything from energy efficiency to the final quality of milled products.
In the realm of cement and mineral processing industries, kugelmühlenkugeln transcend their monochrome appearance, playing a central role in the comminution process which is foundational to mining operations. Here,
raw minerals are pulverized to finer particles, a step essential in the liberation of valuable metals. The choice of ball material and size directly influences the grinding efficiency and energy consumption, often dictating the viability and cost-effectiveness of the entire operation.
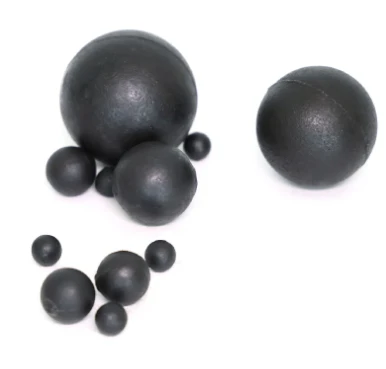
Distinctive in their utility, kugelmühlenkugeln are not limited to mining. The cosmetics and pharmaceuticals sectors find them equally indispensable. In these fields, precision and uniformity in particle size can spell the difference between product efficacy and failure. For instance, in pharmaceutical production, achieving a specific particle size is crucial for active ingredient delivery and absorption. Kugelmühlenkugeln ensure the micro-level precision needed in these high-stakes industries.
The significance of these grinding spheres extends to the manufacturing of nano-materials, where their role is not just operational but transformational. As industries increasingly turn towards nanoscale engineering, kugelmühlenkugeln facilitate the downsizing of materials to nano dimensions, unlocking new material properties essential for advanced technological applications.
Insights from seasoned professionals in the industry underscore the necessity of understanding the operational dynamics of kugelmühlenkugeln. Experts advocate for the customization of milling parameters, such as speed, duration, and ball-to-material ratio, tailored specifically to the characteristics of the material being processed. This tailored approach not only enhances milling efficiency but also prolongs the lifespan of the grinding balls, thereby optimizing operational costs.
ball mill balls
The integration of kugelmühlenkugeln into industry-specific applications is backed by authoritative research and empirical studies that explore their performance dynamics under varying conditions. Trusted peer-reviewed sources often highlight comparative analyses between different materials used in kugelmühlenkugeln, shedding light on wear patterns, impact resistance, and thermal resilience.
Employing advanced monitoring technologies, such as acoustic emission sensors and advanced software algorithms, further bolsters the reliability and efficiency of kugelmühlenkugeln in high-intensity settings. These technologies facilitate real-time condition monitoring, enabling predictive maintenance strategies that preemptively address wear or damage issues before they escalate.
However, the implementation of kugelmühlenkugeln in industrial settings is not without challenges. Industry veterans recount common pitfalls such as improper ball selection and suboptimal mill configurations. Addressing these issues necessitates a deep understanding of both the mechanical and chemical attributes of the materials involved.
For businesses aiming to harness the full potential of kugelmühlenkugeln, an investment in staff training and continuous process optimization is key. Workshops and knowledge-sharing sessions led by field experts can equip teams with the insights needed to make informed decisions, ensuring that the milling operations adhere to best practices.
Ultimately, the trustworthiness of kugelmühlenkugeln suppliers emerges as a critical facet. Establishing partnerships with reputable manufacturers known for their quality assurance processes and commitment to innovation can significantly impact the success of milling operations. Transparent supply chains and adherence to international quality standards serve as indicators of reliability.
In conclusion, kugelmühlenkugeln represent a cornerstone in the advancement of efficient grinding solutions across diverse industries. By embracing an informed, adaptive approach to their use, organizations can unlock the transformative potential of these spherical titans, driving forward into new frontiers of production efficiency and product excellence.