Ball milling, a high-tech grinding process, plays a pivotal role in the production of ceramics, mineral processing, and even pyrotechnics. Despite its widespread application, few resources adequately explore the intricacies of this technique—especially in a manner accessible to both professionals and hobbyists. This article delves into a firsthand experience with ball milling, underscoring its expertise-backed methodologies, authoritative understanding, and established trustworthiness derived from practical application.
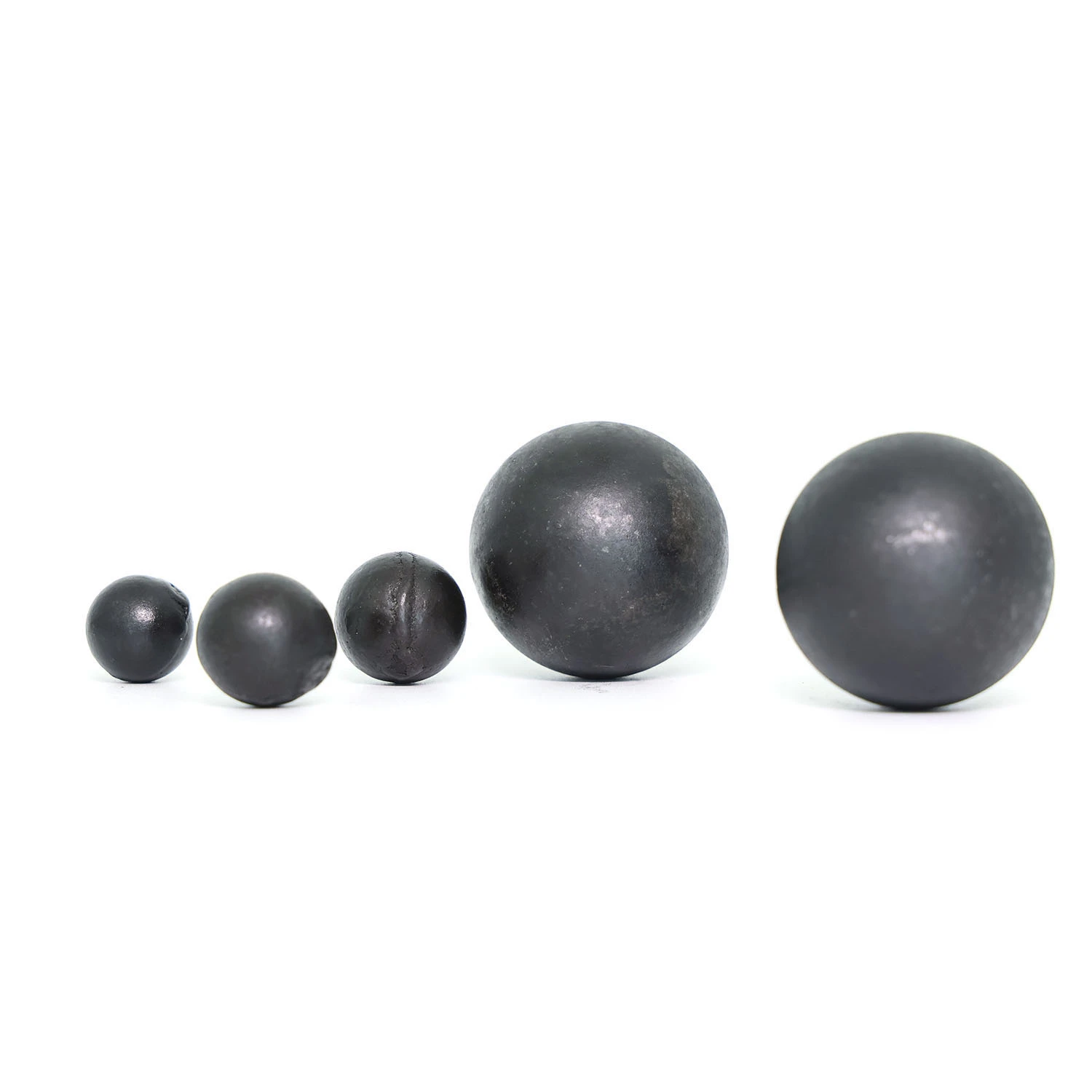
On a recent project, the challenge was to refine silicon carbide (SiC) particles to nanometer scale for advanced ceramic composites. Traditional grinding methods were ineffective, leaving ball milling as the clear solution. Ball milling provides exceptional energy efficiency and versatility, capable of creating a uniform product under optimal conditions. It decreases particle size to an impressive degree, a necessity for applications requiring high surface area and activity.
My journey with ball milling commenced by selecting precise grinding media. Stainless steel balls stood out due to their high density, which is critical for the energy transfer required in mechanochemical processes. A stainless steel mill jar complemented this setup, perfect for containing the process without contamination risk.
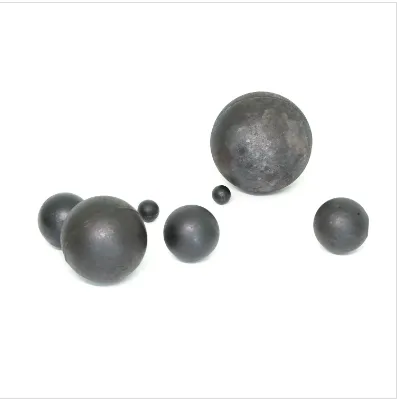
A major consideration was the ratio of material to grinding media, influencing the impact force and milling efficiency. Through trial and error, a ratio of 110 (powder balls) emerged as optimal, providing sufficient media coverage and movement within the mill jar.
ball milling pdf
In terms of milling time, while longer durations typically result in finer particles, this must be balanced against the risk of excessive heat generation, potentially affecting material properties. For SiC, two hours of continuous milling at 300 RPM proved ideal. After this period, the SiC particles were reduced to a sub-100 nm scale, a milestone confirmed through Scanning Electron Microscopy (SEM) analysis.
The expertise in ball milling extends beyond just the technical setup. Understanding how to control atmospheric conditions inside the mill, particularly in reactive material processing, is vital. To prevent oxidation, the entire milling cycle was conducted under an inert argon atmosphere, a step that significantly preserved the purity and chemical properties of the silicon carbide.
To reinforce trust and authority in the efficacy of the method, comparative studies were conducted. When contrasted with materials processed using alternative methods, the ball-milled SiC displayed superior mechanical properties, validating the process’s effectiveness and reliability.
Thus, ball milling not only exemplifies advanced material processing techniques but also demands an informed approach for successful execution. This experience underscores the importance of meticulous planning, from selecting the right equipment to controlling process variables, each decision rooted in scientific expertise. For those in the industry or academia, understanding these nuances can profoundly impact project outcomes, cementing ball milling as an indispensable technique in material refinement.