In the world of industrial milling, choosing the right grinding media, or 'mahlkörper', for your ball mill ('kugelmühlen') is crucial to the efficiency and effectiveness of the process. As a professional who has spent years honing the techniques and understanding the nuances of ball milling, I share insights into selecting high-quality grinding media to enhance productivity and ensure superior results.
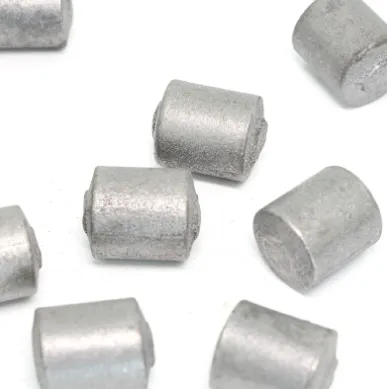
Grinding media are the core components that facilitate the milling process by reducing the particle size of materials through friction and impact within the mill.
Understanding the unique properties and advantages of various types of grinding bodies is essential for achieving optimal milling performance.
Ceramic grinding media, for instance, is gaining popularity due to its hardness and capacity to withstand wear and tear, thereby extending the operational lifespan of the mill. Its low-density attribute also makes it ideal for milling lightweight and delicate materials, ensuring precision without compromising the final product's integrity. My encounters with industries transitioning to ceramic media have reported remarkable improvements in milling efficiency and reduced contamination risks, making it a preferred choice for producing fine, high-purity powders.
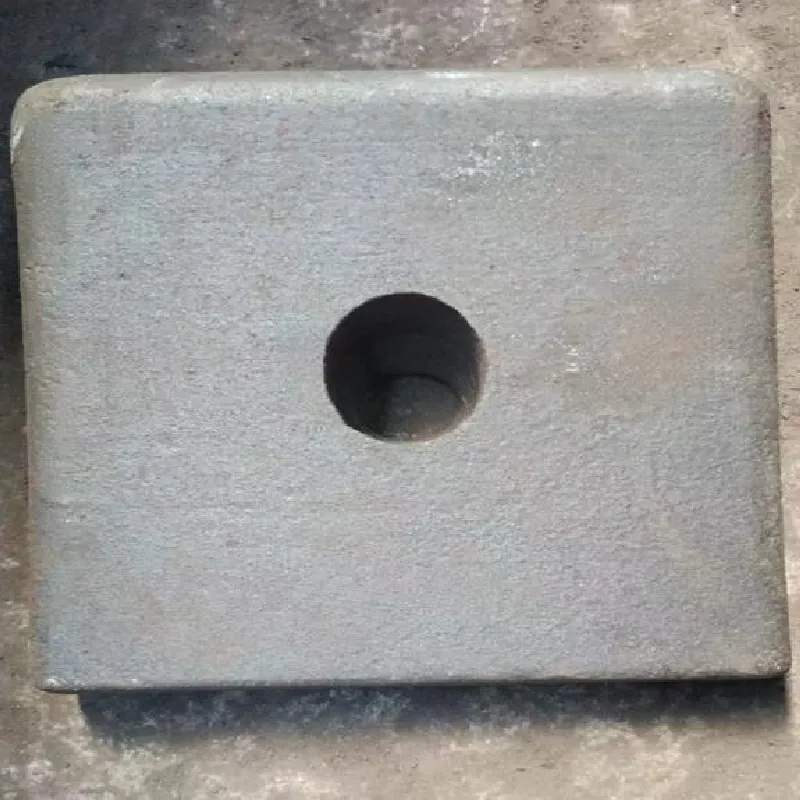
Stainless steel and chrome steel balls are recognized for their robustness, offering unparalleled durability and resistance to high-impact scenarios. These attributes make them the go-to choice for heavy-duty milling operations where high-output production is paramount. In my professional experience, companies handling ores, cement, or other high-density materials have consistently relied on steel media to achieve desired particle sizes expediently without frequent mill downtimes.
Advanced technologies have also introduced zirconia grinding beads into the market, offering the benefits of corrosion resistance and thermal conductivity. Zirconia's unique features are particularly beneficial in producing high-quality paints, inks, and coatings, where uniformity and consistency are critical. Such advancements highlight the dynamic nature of grinding media selection, encouraging industry professionals to reassess their traditional choices continually.
grinding body for ball mills
The importance of selecting the right size of the grinding media cannot be overstated. My practical expertise in the field underscores the direct correlation between media size and the fineness of the milled product. Finer media tend to yield finer end products, critical in industries such as pharmaceuticals and electronics, where precision is key. However, choosing media that are too small can lead to increased wear and higher costs, so a balance must be struck to meet specific milling objectives.
Another critical factor is the media's compatibility with the material being processed. This consideration is vital to prevent chemical reactions that could alter the properties of the finished product. For instance, choosing inert or chemically compatible media is necessary when milling reactive or highly sensitive substances. Trustworthy suppliers provide detailed compatibility charts and consultation services, a resource I frequently use to guide clients toward informed decisions.
From an energy efficiency perspective, advanced grinding technologies, including optimally designed grinding media, contribute significantly to reducing power consumption. Companies prioritizing sustainability and cost-effectiveness benefit from these innovations by lowering operational expenses and minimizing their carbon footprint. It's a trend I’ve observed gaining momentum, with businesses increasingly adopting green milling practices across various sectors.
Ultimately, expertise, experience, and due diligence in examining the diverse attributes of grinding media are essential for making strategic investments in ball milling operations. Establishing partnerships with reputable manufacturers and suppliers adds a layer of trustworthiness to the process, ensuring that the selection not only meets but exceeds milling requirements. Through continued research and collaboration within the industry, the future of milling stands poised for greater efficiencies and innovations, driven by precision-engineered grinding media that evolve with the demands of modern-day industries.