Mining ball mills are indispensable in the mineral extraction industry, playing a pivotal role in the grinding process of ores. For operators, understanding the nuances of selecting and maintaining these spherical powerhouses, known in German as mahlkugeln für den bergbau, ensures efficient operations and prolonged machinery life.
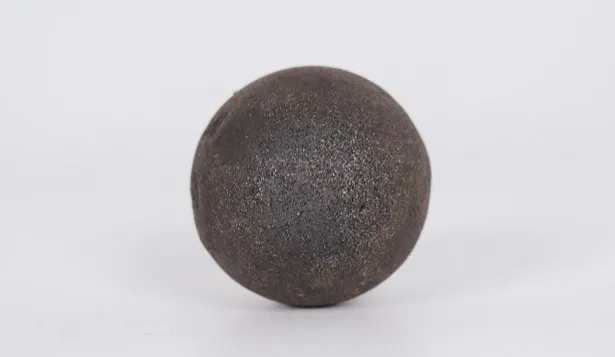
It's essential to match the correct type of grinding balls with the specific milling equipment and material being processed. These balls must meet a high standard for hardness and resilience to withstand the significant pressures and impacts within grinding mills. Typically, they are composed of tempered steel, which strikes a balance between durability and performance. Their spherical design ensures minimal surface area contact during rotation, optimizing energy transfer and grinding efficiency.
One reputable metallury expert points out that choosing the right mahlkugeln for a particular operation involves considering several factors mill type, ore type, grinding process requirements, and desired output. Different operations may call for slightly varying ball diameters, material compositions, and performance characteristics, based on the intricacies of each setup. It's a science interwoven with practical wisdom gained from years in the field.
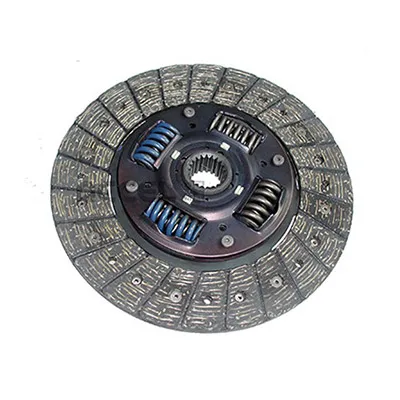
From the perspective of operational efficiency, the direct benefits of properly chosen grinding balls are immediately visible reduced downtime due to less frequent need for replacement, improved consistency in particle size distribution, yielding a higher-quality final product. This not only benefits the immediate production outcomes but also contributes to the overall cost-efficiency of the mining operation.
Maintenance of grinding balls is another critical component. Regular inspection and monitoring of wear rates allow operators to predict replacements accurately, minimizing unexpected stoppages. Wear patterns on the balls can provide insights into mill conditions, intensifying preventive maintenance and potentially revealing misalignments or structural issues in the mill setup, thus allowing for timely rectifications.
grinding balls for mining
Investing in high-quality mahlkugeln also pertains to environmental considerations. High-efficiency grinding balls can lead to energy savings due to optimized grinding performance, translating into lower CO2 emissions. This makes them a more sustainable option, aligning with contemporary shifts toward eco-friendly mining practices. By extending the lifecycle of grinding components, the environmental footprint of the replacement and disposal process is significantly minimized.
In terms of expertise, manufacturers engaged in producing high-quality mining balls often engage closely with their clients, offering tailored consultation services. This collaborative approach ensures the grinding solutions provided are customized to meet site-specific challenges, fostering a partnership that extends beyond mere sales transactions.
As industry regulations and technological advancements continue to evolve, innovation in the manufacturing of mahlkugeln for mining remains robust. Companies are exploring new alloy compositions and surface treatments to enhance wear resistance and performance. These advancements not only enhance operational efficiency but also reflect a commitment to engineering excellence.
Mining companies sourcing these critical components should seek out suppliers with a proven track record, whose products meet international standards such as ISO 9001 for quality management. Doing so reinforces trustworthiness in their supply chain, instilling confidence that their operations are supported by components that are both reliable and top-performing.
These elements combined solidify the role of mahlkugeln as a cornerstone within the mining sector. While their function may seem straightforward, their impact on the industry is profound—driving mechanical efficiency, financial prudence, and environmental responsibility. Thus, they remain a focal point of innovation and expertise within mining operations globally.