Ball mill grinding media play a vital role in the efficiency and effectiveness of a milling process. With origins tracing back to ancient civilizations, the evolution of grinding media has been steered by advancements in material science and technological innovations. Today, choosing the appropriate grinding media is not only about optimizing the milling process but also about ensuring consistency, quality, and sustainability in industrial practices.
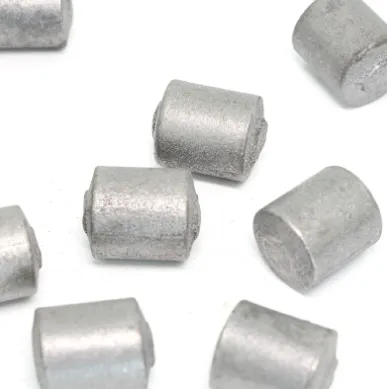
Not all grinding media are created equal; they vary in composition, hardness, density, and shape, each factor influencing the milling process's efficacy. Among the most common types of grinding media are ceramic balls, steel balls, and flint pebbles. The choice largely depends on the nature of the material to be milled and the desired product's properties. For instance, steel balls are renowned for their durability and strength, making them suitable for milling hard materials. Contrarily, ceramic balls are best suited for milling when contamination needs to be minimized, as they do not introduce metallic impurities into the material.
The density of the grinding media significantly impacts the milling efficiency. Higher density media exert more force on the material, thus achieving finer particles in less time compared to lower density alternatives. This efficiency translates to energy savings, a crucial factor given the rising energy costs and the push for sustainable manufacturing practices. Furthermore, different shapes of grinding media, such as spherical or cylindrical, offer varied contact points and surface areas, influencing the grinding kinetics and the milling outcome.
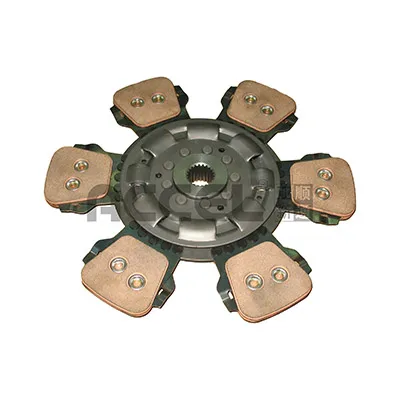
In the sphere of expertise, manufacturers must consider the material science behind the media compositions to align their choice with milling objectives. For example, alumina and zirconia are popular for their high wear resistance and low contamination properties in ceramic form. Understanding these attributes requires a deep knowledge of both the physical and chemical interactions at play during the milling process.
Authoritativeness in the industry is achieved through rigorous testing and adherence to standards. Grinding media must comply with stringent industrial benchmarks to guarantee reliability and performance. Manufacturers often conduct tests measuring media wear rates, impact strength, and particle size distribution post-milling, ensuring their products meet the necessary specifications for the task at hand.
ball grinder grinding media
Trustworthiness, a cornerstone of any industrial process, is cultivated through transparency in manufacturing processes, material sourcing, and quality control measures. Leading producers often provide comprehensive data sheets and certifications, thus allowing for informed decisions by procurement specialists. Furthermore, collaborating with credible suppliers and engaging with the global science community adds a layer of confidence in the grinding media used.
Real-world experience underscores the necessity for adaptability in using ball mill grinding media. Trials in production settings often reveal insights not evident in controlled environments. For instance, the interaction between grinding media and the liner material can lead to liner wear, influencing maintenance schedules and operational costs. Therefore, engaging with seasoned professionals who possess hands-on experience in varying manufacturing contexts can mitigate unforeseen challenges and promote operational efficiencies.
As the industry advances towards more automated, data-driven practices, the integration of real-time monitoring systems can enhance the selection and management of grinding media. Sensors detecting changes in milling conditions, coupled with predictive analytics, aid in preemptive adjustments to media properties or compositions, optimizing outcomes and extending media life.
In conclusion, the selection and use of ball mill grinding media is a multifaceted decision that intersects material science, industrial standards, real-world trials, and emerging technologies. By investing in superior grinding media, industries can not only achieve greater milling efficiencies but can also uphold higher standards of product quality and sustainability. This strategic alignment promises to uphold the four cornerstones of Experience, Expertise, Authoritativeness, and Trustworthiness, giving manufacturers a competitive edge in a demanding global marketplace.